Grünschnitt wird erstmals in Halle carbonisiert
Biomasse ist derzeit neben der Wasserkraft der einzige grundlastfähige regenerative Energieträger. Doch sind die Potenziale nicht so unerschöpflich wie die von Sonne und Wind. Umso wichtiger ist die Erschließung neuer Nutzungsbereiche.
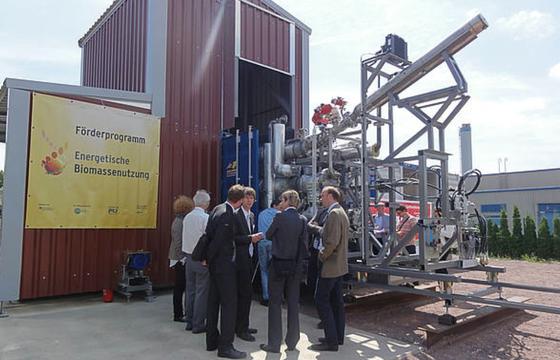
Diplom-Ingenieur Andreas Clemens (Mitte), erklärt die neue HTC-Demonstrationsanlage, die aus Bioabfällen hochwertige Brennstoffe herstellt. Clemens ist wissenschaftlicher Mitarbeiter des Deutschen Biomasseforschungszentrums DBFZ.
Foto: DBFZ
Auf der Großdeponie Lochau, wenige Kilometer östlich von Halle, ist in einem äußerlich eher unscheinbaren blau lackierten Normcontainer eine kleine Chemieanlage verstaut, die Regina Blümel mit einem Schnellkochtopf vergleicht. „Aus angemaischtem Grünschnitt wird hier bei 220 °C und 25 bar Druck binnen weniger Stunden Kohle, ein Prozess, für den die Natur Millionen von Jahren benötigt“, sagt die Projektleiterin für die nach neun Monaten Bauzeit in Betrieb genommene Anlage zur hydrothermalen Carbonisierung (HTC).
Das Verfahren, dessen Grundlagen bereits von Nobelpreisträger Friedrich Bergius gefunden wurden, wurde gemeinsam mithilfe des Deutschen Biomasse-Forschungszentrums (DBFZ) in Leipzig, der Stadtwerke Halle und des Spezialanlagenbauers Artec Biotechnologie GmbH aus Bad Königshofen für eine erste Pilotanlage genutzt. Zuvor hatte Artec seit 2009 im Labormaßstab erfolgreiche Tests mit einer Versuchsapparatur vorgenommen.
Aus 2500 Tonnen Grünnschnitt werden 1000 Tonnen Trockenkohle
2500 t Grünschnitt – vom einfachen Wiesenschnitt bis hin zu Holz – können in den waagerecht angeordneten Kolonnen aus Edelstahl pro Jahr verarbeitet werden. Das Ergebnis sind etwa 1000 t aufcarbonisierte Trockenkohle mit einem Kohlenstoffanteil von über 60 %.
Matthias Lux, Geschäftsführer der Stadtwerke Halle, sieht gute Chancen für den nun beginnenden Großversuch, den der Bund mit rund 500 000 € bezuschusst. „Wir haben, wie andere Stadtwerke auch, bislang kaum eine sinnvolle Verwendung für diese Art Biomasse. Zudem haben wir auf der Deponie aus dem hier laufenden Blockheizkraftwerk genügend Prozesswärme für den Trocknungsprozess“, berichtet Lux.
Das BHKW wird mit Deponiegas betrieben, rechnet sich aber für die alleinige Stromproduktion im Sommer nicht, wenn ein geringer Wärmebedarf der Betriebsgebäude anfällt. Das lässt sich gut ausgleichen, da der Grünschnitt, der vor dem Maischen auf eine Korngröße von 10 mm zerkleinert werden muss, vor allem in der warmen Jahreszeit anfällt.
Weitere Untersuchungen im Deutschen Biomasseforschungszentrum
Zunächst wird die produzierte Kohle, ein krümeliger, graubrauner Stoff, im DBFZ weiter untersucht. Bereichsleiter Marco Klemm will damit vor allem Zusammenhänge zwischen der Zusammensetzung der Ausgangsstoffe und dem Kohlenstoffgehalt, aber auch das Verhalten der HTC-Kohle im Verbrennungsprozess untersuchen, um den Wirkungsgrad der Kette zu erhöhen.
Mit konkreten Aussagen, wo dieser derzeit liegt, hält sich Klemm bislang zurück. Das sei maßgeblich von den Parametern einer Anlage und der Ausgangsstoffe abhängig. Allerdings, so räumt Klemm ein, ist vor allem der energetische Trocknungsaufwand hoch, auch wenn die nasse Kohle zunächst mit einer Schneckenpresse mechanisch entwässert wird. Allerdings stehe an den BHKW, wie hier in Halle, sehr häufig überschüssige Abwärme zur Verfügung, so dass die Kosten nicht von vornherein das Projekt der Biokohle scheitern lassen. Doch gibt es noch weitere Hürden zu nehmen.
Weiterverarbeitung zu Pellets angedacht
Bislang ist noch nicht klar, wie HTC-Kohle künftig normiert werden kann – ganz einfach, weil ein großer Vorteil des Verfahrens in seiner Robustheit gegenüber variierenden Einsatzstoffen liegt. „Ob Küchenabfälle, Trester, Gärreste aus Biogasanlagen, Gras oder Holz, ist der Anlage eigentlich egal, hier gibt es ja keine empfindlichen Bakterien wie in der Biomassevergärung“, berichtet Peter Wieczorek von Artec. Doch um HTC anschließend verkaufen zu können, müssen klare Zertifizierungsverfahren durchlaufen werden, zumal Regina Blümel über eine Weiterverarbeitung zu Pellets nachdenkt. Zumindest in Halle dürfte das kein Problem sein, weil hier eine große Konstanz in der Beschickung möglich sei, sagt sie.
Wieczorek sieht aber auch noch einen anderen denkbaren Vermarktungsweg. HTC könnte durchaus auch als Ersatz für Torf zur Bodenverbesserung und Humusanreicherung verwendet werden.
Noch doppelt so teuer wie Kohle
„Wir haben bisher das Problem, dass HTC rein kommerziell nicht gegen billige Braunkohle konkurrieren kann, es aber auch noch keine Förderung wie für Biogasanlagen gibt“, sagt er. Die Herstellung von HTC kostet nach seinen Schätzungen in einer kommerziellen Anlage mindestens 100 €/t, das ist gut das Doppelte von Kohle.
Torf hingegen, dessen Gewinnung zudem ökologisch höchst bedenklich ist, kommt je Tonne auf deutlich mehr als 200 €. „Ich kann mir gut vorstellen, dass HTC in der Breite vor allem die Gärschlämme von Biogasanlagen nutzen wird“, sagt er und verweist auf die bakteriell völlig neutrale Substanz – anders, als wenn die Schlämme direkt auf die Felder verbracht werden. Zudem sei mit der Carbonisierung eine Verbesserung der Humusbilanz zu erwarten.
Ein Beitrag von: