Innovative Batterie-Produktion macht China Konkurrenz
Es gibt einen neuen Hot-Spot für die Batterie-Herstellung: Am Fraunhofer IPA hat das Zentrum für Digitalisierte Batteriezellenproduktion (ZDB) eröffnet. Zusammen mit dem Industriepartner VARTA AG bringen sich Forschende in Stellung. Ihr Ziel: Die Konkurrenz aus Asien überholen.
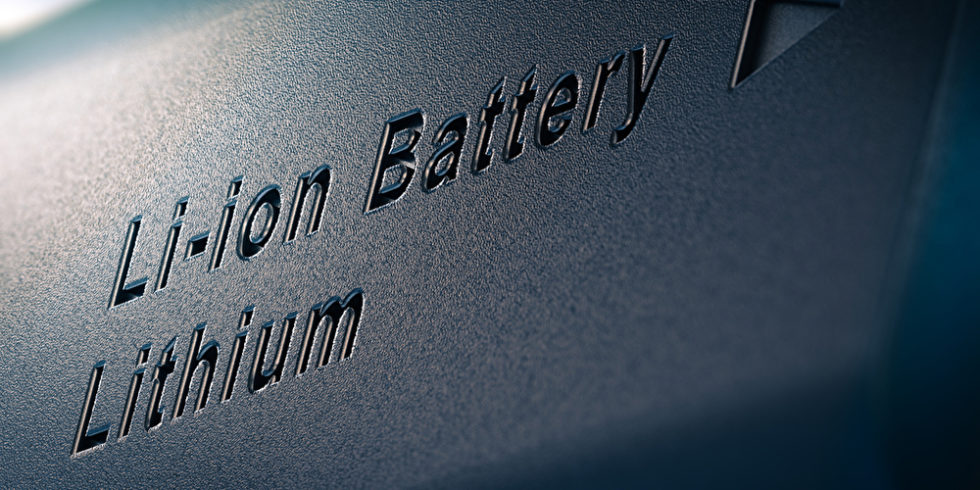
Von einer effizienten Batterie-Produktion wird in Zukunft viel abhängen.
Foto: panthermedia.net/Olivier26
Es geht voran mit der Elektromobilität, und daran trägt China einen bedeutenden Anteil. Das aber nicht wegen innovativer Technologie made in China, sondern wegen der Importbeschränkungen für Verbrennermotoren. Das hat unter anderem die deutschen Automobilhersteller aus der Reserve gelockt. Der Markt wird sich in den kommenden Jahren ohne Frage noch kräftig weiterentwickeln, wobei aber ein neues Problem entstehen könnte. Denn aktuell kommen die Batteriezellen für die E-Autos vor allem aus China, Südkorea, Japan und den Vereinigten Staaten. Das soll sich ändern.
Ganz neues Material sticht Lithium-Ionen-Akkus aus
„Wenn die deutsche Industrie künftig nicht mehr von asiatischen Batteriezellenproduzenten abhängig sein soll, müssen wir in Deutschland und Europa nicht nur unseren Rückstand aufholen, sondern die Technologieführerschaft übernehmen“, sagt Alexander Sauer. Er leitet das Fraunhofer-Institut für Produktionstechnik und Automatisierung IPA sowie das Institut für Energieeffizienz in der Produktion EEP der Universität Stuttgart. Das neue Zentrum für Digitalisierte Batteriezellenproduktion (ZDB) soll dafür der Grundstein sein.
Bedarf an Batterien birgt Chancen für Wissenschaft und Wirtschaft
Ist es für eine Aufholjagd nicht längt zu spät? Dem mag Kai Peter Birke nicht zustimmen. Er ist Professor für Elektrische Energiespeichersysteme an der Universität Stuttgart und leitet das neue ZDB: „Der Aussage, der Zug für Batteriezellfertigung sei abgefahren, kann man keinesfalls zustimmen. Im Gegenteil: Gerade, weil zukünftig viele Gigawattstunden an Batteriekapazität benötigt werden, ist Spielraum für neue Akteure und verbesserte Ansätze vorhanden.“
Sauer und Birke sind sich einig: Der Schlüssel für den Erfolg sei die Digitalisierung der Batteriezellenproduktion. Damit wäre der Pfad der nächsten Jahre für das ZDB gesteckt. Die wichtigsten Bausteine sind bereits vorhanden. Denn in den vergangenen drei Jahren haben Wissenschaftlerinnen und Wissenschaftler des Fraunhofer IPA gemeinsam mit Mitarbeitenden der VARTA AG die Hauptbestandteile der Prozesskette der Batteriezellenproduktion im Labormaßstab nachgebaut. Die einzelnen Stationen haben sie im Anschluss miteinander vernetzt.
Digitaler Zwilling bildet die Batteriezellen-Produktion ab
Bei dieser Vernetzung über die gesamte Prozesskette hinweg entstehen große Datenmengen (Big Data). Die Forschenden sammeln diese Daten und werten sie aus, um die Produktion weiter zu verbessern. Künftig wird das in Echtzeit passieren. Dafür richten die Wissenschaftlerinnen und Wissenschaftler einen sogenannten digitalen Zwilling ein, der die Herstellung virtuell abbildet. Ineffiziente Abläufe können auf diese Weise schnell identifiziert und abgewandelt werden. Ein gutes Beispiel ist dafür die Elektrolytbefüllung. Wenn dieser wichtige Arbeitsschritt während der Montage präziser ausgeführt wird, wirkt sich das später auf die Performance der fertigen Batteriezelle aus – sie wird leistungsfähiger.
Batterie voll oder leer? Dieser einfache Trick zeigt es in Sekunden
Ein wichtiger Ansatz im ZDB ist zudem eine große Flexibilität. Die Forschenden haben keinen Zweifel daran, dass sich die Fertigung von Batterien im Laufe der nächsten Jahre verändern wird. Deswegen planen sie Fabriken so, dass sie mit relativ wenig Aufwand umgestaltet werden können. Sie sollen also von vornherein wandlungsfähig sein, um Zeit und Kosten zu sparen. Neben dem verwendeten Material betrachten die Experten daher auch Energie- und Informationsflüsse in der Batteriezellenproduktion und setzen sie zueinander in Beziehung. Zu dem realen Fabriklayout können sie ein ideales Fabriklayout entwickeln und die Differenzen aufzeigen.
Batterien mit höherer Energiedichte sind das Ziel
Die Forschenden haben dabei starke Hilfe an ihrer Seite: Die VARTA AG hat viel Erfahrung mit der Produktion von Lithium-Ionen-Batterien. Gemeinsam wollen die Partner einsatzfähige Festkörperbatterien produzieren, die eine deutlich höhere Energiedichte aufweisen sollen als bisherige Batteriezellen. Wenn das gelingt, könnte die Technologieführerschaft wieder in Deutschland liegen. „Industrie und Forschung gehen im Zentrum für Digitalisierte Batteriezellenproduktion eine Symbiose ein, die beide Seiten weiterbringt“, sagt dazu Joachim Montnacher, der am Fraunhofer IPA das Geschäftsfeld Energie leitet.
Mehr lesen zum Thema Batterieforschung:
Ein Beitrag von: