Lithium-Ionen-Batterien deutlich billiger durch neues Herstellungsverfahren
Ein Schub für die Energiewende? Forscher am Karlsruher Institut für Technologie haben das Verfahren zur Herstellung von Energiespeichern etwa für E-Autos deutlich beschleunigt. Damit soll die Technologie wesentlich billiger werden.
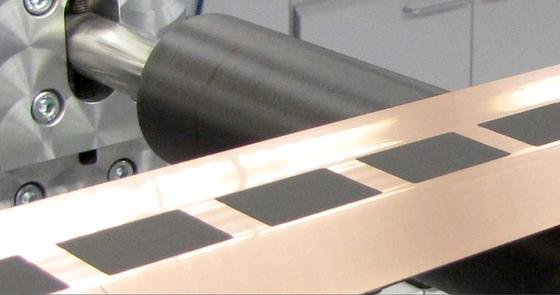
Das KIT hat ein Verfahren entwickelt, mit dem man Elektrodenfolien besonders schnell und präzise beschichten kann. Dadurch könnte sich die Herstellung von Lithium-Ionen-Akkus deutlich verbilligen.
Foto: KIT
Mit dem neuen Verfahren lassen sich pro Minute 100 Meter Elektrodenfolie herstellen. Diese beschichteten Materialien sind die eigentlichen Energiespeicher in Lithium-Ionen-Batterien, wie sie beispielsweise in Elektroautos eingesetzt und auch als Speichermedium für Erneuerbare Energien verwendet werden. Damit verdreifacht sich nach Angaben des Karlsruher Instituts für Technologie (KIT) das Produktionstempo – und das bei fast gleich bleibenden Kosten.
Wenn die Herstellung der Folien deutlich billiger wird, könnte das einen Schub für die Energiewende bedeuten. Derzeit entstehen weltweit beispielsweise immer mehr große Speicherkraftwerke, die gewaltige Mengen Energie aufnehmen und so als Ausgleich für die schwankenden Netzeinspeisungen aus Wind- oder Sonnenenergie dienen können – auch sie arbeiten mit Lithium-Ionen-Akkus.
Eine Arbeitsgruppe im KIT-Forschungsbereich „Thin Film Technology“ hat drei Jahre lang an dem Verfahren gearbeitet. Ein flexibles Düsensystem ermögliche nun, „beliebige Muster mit großer Präzision auch bei hohen Geschwindigkeiten zu erzeugen“. Diese Muster, die sogenannte absatzweise Beschichtung, ist wichtig für die Speicherfähigkeit der Folien.
Beschichtung mit Start- und Stoppkanten
Für die Herstellung einer Elektrodenfolie wird zunächst ein so genanntes Slurry, eine Art zähflüssiger Paste, erzeugt. Es besteht aus Aktivmaterial, das an der elektrischen Reaktion beteiligt ist, dazu Ruß, Lösungsmittel und weitere Bestandteile. Das Material wird auf eine Folie aus Kupfer für die Anode beziehungsweise Aluminium für die Kathode aufgetragen.
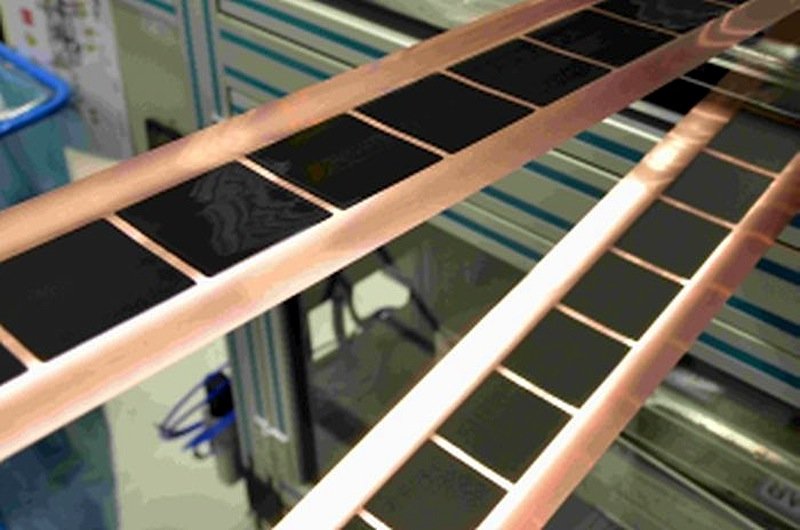
Bei der „intermittierenden“ Beschichtung kommt es darauf an, dass die Start- und Stoppkanten auch bei hohen Frequenzen sauber verlaufen.
Quelle: KIT
Das einfachste Verfahren ist, die Beschichtung durchgehend aufzubringen. Besser aber sei es, sie für nachfolgende Verfahrensschritte zu unterbrechen, erklärt Prof. Wilhelm Schabel vom KIT. Bei dieser „intermittierenden“ Beschichtung komme es dann aber darauf an, „dass die Start- und Stoppkanten auch bei hohen Frequenzen sauber verlaufen“, sagt der Forscher.
„Dies erreichen wir bei unserem Verfahren durch eine Membran, die sich im Auftragswerk, das heißt in der Düse, schnell und gesteuert hin- und her bewegt.“ Die Fließeigenschaften der Paste könnten dann auch noch im Herstellungsprozess angepasst werden.
Zielvorgabe weit übertroffen
Der Verband des Deutschen Maschinen- und Anlagenbaus (VDMA) hatte erst vor wenigen Wochen eine „Roadmap“ vorgestellt, die 15 wesentliche Herausforderungen für eine kostengünstige Batterieproduktion beschreibt, die den steigenden Bedarf decken kann. Eine davon war das Ziel einer Beschichtungsgeschwindigkeit von 100 Metern pro Minute. Mit den vorhandenen Technologien schien dieses Maß kaum erreichbar.
Der Verband zeichnete ein recht pessimistisches Bild, weil Versuche mit Bedampfen, Pulverbeschichtung oder Tintenstrahlverfahren bereits gescheitert seien. Dementsprechend großzügig setzte der VDMA als Zielvorgabe das Jahr 2030 an – kurz danach melden die KIT-Wissenschaftler Vollzug.
Ein Beitrag von: