Modulbaukasten soll Kosten für Offshore-Windenergieanlagen senken
Offshore-Windkraftanlagen sind weitgehend Einzelanfertigungen. Wissenschaftler arbeiten nun an Konzepten, die eine kostensenkende Serienfertigung ermöglichen sollen. Ein modulares Großmodell soll das auf der Husum Wind Energy verdeutlichen.
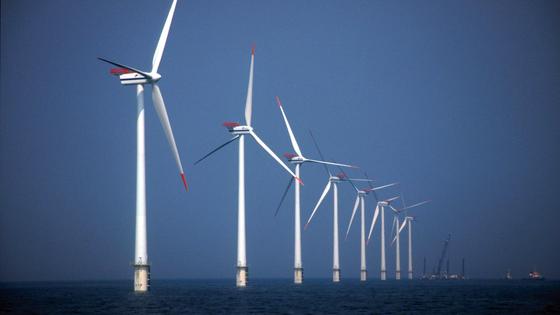
Offshore-Windenergieanlagen.
Foto: BWE
Vieles deutet derzeit darauf hin, dass getriebelose Windenergieanlagen die bevorzugte Lösung für Offshore-Anwendungen sein werden. „Das Konzept ermöglicht eine kostensparende modulare Bauweise und könnte wegen der geringeren Zahl von Komponenten auch weniger störanfällig sein“, macht Jan Wenske, stellvertretender Leiter des Fraunhofer-Institutes für Windenergie in Bremerhaven (IWES) deutlich. Auf der Husum Wind Energy, vom 18. bis 22. 9. , präsentieren IWES und das Forschungszentrum Windenergie der Hochschule Saarbrücken ein Großmodell dieser zukunftsträchtigen Windturbine.
Windkraftanlagen für den Offshore-Einsatz werden „praktisch in Einzelfertigung hergestellt und sind entsprechend teuer“, hat Wenske unter anderem bei den Herstellern vor seiner Institutstür in Bremerhaven beobachtet. Nach Ansicht Friedrich Klingers von der Hochschule Saarbrücken sucht die Industrie jedoch in der falschen Richtung nach einem Ausweg aus der Kostenfalle: „Man will die Leistung immer mehr erhöhen und erwartet dann, dass die Kosten pro erzeugter Kilowattstunde sinken.“
Das sei jedoch ein Irrweg, denn mit der Leistung stiegen auch die Massen von Generator und Rotor, damit auch die Anforderungen an Türme und Fundamente und letztlich insgesamt der Materialaufwand: „Eine Vervierfachung der Leistung bedeutet das Achtfache an gesamter Masse“, rechnet Klinger vor. Grundsätzlich sei es deshalb sinnvoller, kleinere Anlagen zu verwenden und deren Herstellungs- und Betriebskosten zu senken.
Forschungsprojekt entwickelt Windkraftanlagen mit modularer Bauweise und serieller Fertigung
Genau dies ist das Thema des Forschungsprojektes, das Wenske und sein Team in Bremerhaven verfolgen. Das Ziel sind direkt angetriebene Windturbinen im Leistungsbereich zwischen 3 MW und 8 MW, die durch eine modulare Bauweise eine serielle und damit kostengünstige Fertigung erlauben sowie den logistischen Aufwand für die Montage und die Wartung reduzieren.
Durch eine geringere Zahl von Komponenten könne zudem die Störanfälligkeit der Anlagen verringert werden. „Das würde hervorragend zu den Herausforderungen des Offshore-Betriebes passen: Kostensenkung und hohe Anlagenverfügbarkeit“, meint Wenske.
Das von Klinger für die Husum Wind Energy vorbereitete Großmodell weist bereits viele Merkmale auf, die zu diesen Anforderungen passen. Herz der getriebelosen Anlage ist ein Außenläufer-Vielpolgenerator, der sich in der Praxis bei zwei Herstellern bereits bewährt habe. Die Rotorblätter sind dabei nicht auf einer Nabe vor dem Generator angeflanscht, sondern direkt auf dem Außenläufer.
Die Mechanik zum Verstellen der Rotorblätter ist im ersten Blattabschnitt untergebracht, der als ein Gussteil mit dem Außenläufer gefertigt wird, erst an dessen Ende folgt der verstellbare Teil des Rotorblattes. Der Vorteil: Die beweglichen Teile des Blattes sind kürzer, damit wird weniger Material verbraucht, vor allem aber sind die Belastungen für die Pitch-Lager geringer.
Noch müssen viele Aspekte dieser Entwicklung erforscht und optimiert werden. Das Lastenheft umfasst z. B. die Detailkonstruktion der Pitch-Lagerung, die Optimierung der Aerodynamik sowie die Modellierung und Simulation des Gesamtanlagenverhaltens.
Wenske: In „Smart Wind Turbine Modules“ liegt die Zukunft des Windanlagenbaus in Deutschland
Wenske erkennt in dem Gesamtkonzept der Turbine aber bereits die Charakterzüge der „Smart Wind Turbine Modules“, die nach seiner Ansicht die Zukunft des Windanlagenbaus in Deutschland ausmachen werden. Der Windkraftmarkt könne schon bald einen Wandel vollziehen, der in der Entwicklung des internationalen Schiffbaus sein historisches Vorbild habe.
Obwohl deutsche Werften mit ihren hoch spezialisierten Einzelbauten weltweit Maßstäbe setzten, konnten sie sich letztlich nicht gegen die Konkurrenz aus Fernost behaupten. Unabhängig von den staatlichen Subventionen erreichten beispielsweise koreanische Werften durch die Standardisierung, Modularisierung und Automatisierung ihrer Fertigung Kostenvorteile, die ihren Wettbewerbsvorsprung sicherten. Eine derartige Entwicklung drohe auch den deutschen Windkraftanlagenbauern. Wenske: „Chinesische Anlagen kosten teilweise nur noch 400 000 €/MW und damit etwa die Hälfte wie Anlagen aus Europa.“
Um auf dem kommenden Massenmarkt für Windkraftanlagen bestehen zu können, müsste der Weg jedoch von einer großen Zahl unterschiedlicher Designs, Konzepte und Komponenten zu standardisierten Konstruktionen führen, deren Teile in entsprechend hohen Stückzahlen produziert werden können.
Basis für eine derartige smarte Anlage könnte die Turbine sein, die Wenske und Klinger auf der Husum Wind Energy vorstellen. Sie zeichne sich durch eine Reihe von Vorteilen aus: geringe Anzahl von Teilen, einfach und robust, hohe Effizienz und bei Serienfertigung niedrige Kosten. Wenske nennt es das KISS-Prinzip: Keep It Simple and Smart – erfolgreiche Anlagen sind einfach und ausgereift.
Ein Beitrag von: