Neue Wirbelgeneratoren für Windkraftanlagen steigern die Stromerzeugung
Eine neue Generation von Wirbelgeneratoren soll die Aerodynamik und damit die Effizienz von Windkraftanlagen steigern. Die Anlagen werden dadurch leiser und ihre Energieleistung könnte jährlich um bis zu fünf Prozent steigen.
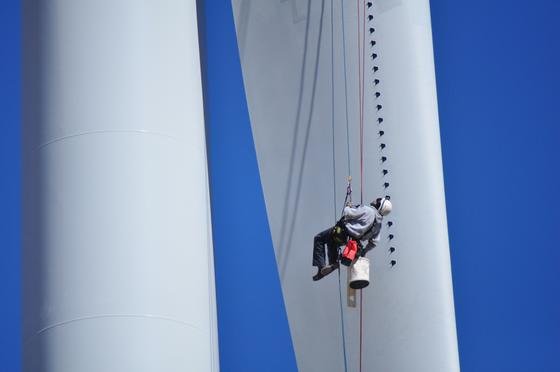
Eine neue Generation von Wirbelgeneratoren haben das Ravensburger Unternehmen Smart Blade, der Technologiekonzern 3M und die TU Berlin entwickelt. Aufgeklebt auf die Flügel von Windrädern verbessern sie die Aerodynamik und steigern die Stromerzeugung.
Foto: 3M
Ein durch die Luft fliegender Golfball wird von ihr umgeben, ebenso ein Flugzeug am Himmel und die Rotoren einer Windkraftanlage in Bewegung: Die Rede ist von der sogenannten Grenzschicht. Jedes massive Objekt, das sich durch die Luft bewegt, wird von dieser dünnen Luftschicht umhüllt.
Wirbelgeneratoren zögern den Abriss der Grenzschicht hinaus
Bei hohen Geschwindigkeiten, wie im Falle des Golfballs, des Flugzeugs und der Rotorblätter, trennen sich jedoch die Wege von Objekt und Grenzschicht. Diese ist langsamer, bleibt zurück und löst sich schließlich vom Objekt. Die dadurch entstehende Strömung bremst das Objekt ab.
Das bedeutet geringere Abschlagsweiten für den Golfer und einen höheren Energieaufwand für das Flugzeug, um den Auftrieb zu halten. Golfbälle haben aus diesem Grund die runden Dellen auf ihrer Oberfläche. Durch sie entstehen kleinere Turbulenzen, die der Grenzschicht mehr Energie geben. Sie bewegt sich schneller und kann dem Objekt länger folgen. Die sogenannten Wirbel- oder Vortexgeneratoren auf Flugzeugen und Windkraftanlagen haben denselben Zweck wie die Dellen im Golfball. Sie zögern den Abriss der Grenzschicht so lange wie möglich heraus.
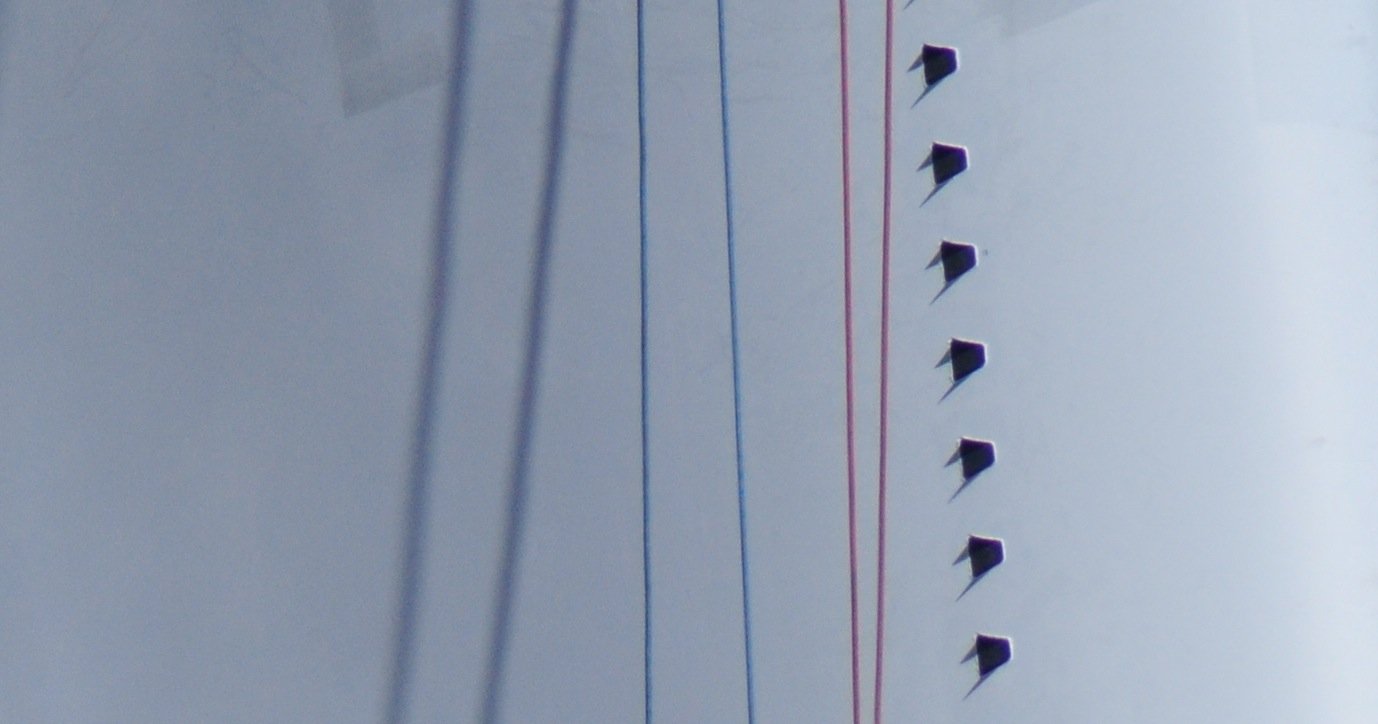
Die kleinen Wirbelgeneratoren werden mit einem Spezialkleber auf die Flügel aufgeklebt. Sie verzögern den Abriss der Grenzschicht der Luft und verbessern damit die Aerodynamik.
Quelle: 3M
Mit zunehmender Bedeutung der Windindustrie wird auch die Entwicklung von Wirbelgeneratoren vorangetrieben, denn ihr gezielter Einsatz kann die Leistung der Anlagen deutlich steigern. An den kleinen, meist dreieckigen Elementen entstehen Wirbel, die die Durchmischung der äußeren Strömung und der Grenzschichtströmung erhöhen. Wenn die Strömungsablösung dadurch verzögert oder gar verhindert werden kann, macht sich das ebenfalls positiv bemerkbar auf die Geräuschentwicklung der Anlage. Sie arbeitet wesentlich leiser.
Häufig tritt die Strömungsablösung im Innenbereich der Rotorblätter auf, weil dort der Anstellwinkel am größten ist. Hier ist Erfahrung und Fingerspitzengefühl gefragt. „Die Eigenschaften einzelner Rotorblätter sind sehr unterschiedlich“, erklärt Christian Claus von der Sparte Wind Energy des Technikkonzerns 3M. „Form, Größe, Anzahl und Position der Wirbelgeneratoren müssen auf jeden Anlagentyp individuell angepasst werden, um so entsprechend die Leistung der Windenergieanlage zu steigern.“ 3M hat nun eine neue Generation von Wirbelgeneratoren auf den Markt gebracht.
Belastungstests im Windkanal der TU Berlin
Als Forschungspartner hatte 3M die Ingenieure des Ravensburger Unternehmens Smart Blade mit ins Boot geholt. Dort wurden die eigentlichen Wirbelgeneratoren entwickelt und unter Realbedingungen im großen Windkanal der Technischen Universität Berlin getestet. Für die Tests verwendete Smart Blade mehrere Testflügel, deren Profile standardmäßig in Windkraftanlagen eingesetzt werden. Die Modelle wurden dann auf einer digitalen Waage, die vom Windkanal entkoppelt ist, montiert. Damit wurden alle auftretenden Luftkräfte präzise gemessen.
Als Experte für innovative Kunst- und Klebstoffe entwickelte 3M dazu einen besonders witterungsbeständigen Kunststoff als Material für die Generatoren sowie einen enorm haltbaren Spezialklebstoff, um die Wirbelgeneratoren dauerhaft auf dem Rotorblatt zu befestigen. Durch die richtige Platzierung auf dem Rotorblatt werden mögliche Turbulenzen verhindert und somit der Energie-Ertrag erhöht. Die Steigerung der Energieleistung soll je nach Anlage zwischen zwei bis fünf Prozent liegen.
Ein Beitrag von: