Rotorblätter mit immer neuen Längenrekorden
In der Windenergiebranche purzeln die Längenrekorde für Rotorblätter immer schneller. Aufgrund der gewaltigen Dimensionen rückt die Einzelblattmontage sowohl onshore als auch offshore in den Fokus. Die Sternmontage mit – üblicherweise – allen drei vormontierten Rotorblättern stößt an ihre Grenzen.
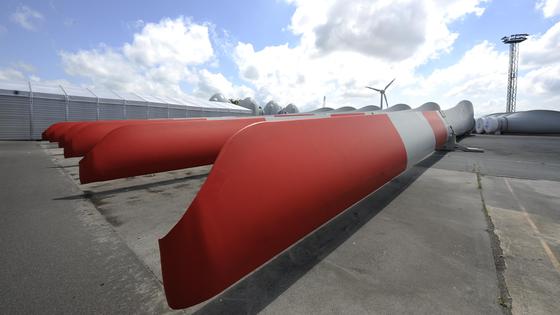
Windräder werden immer größer.
Foto: BARD-Gruppe
Die Gilde der Rotorblattbauer und Anlagenhersteller übertrumpft sich gegenseitig mit immer größeren Rotordurchmessern. Dieser Trend zeichnet sich sowohl an Land als auch auf dem Meer ab. Erst Mitte Oktober hatte Samsung mit 171 m Gesamtdurchmesser für einen dreiblättrigen Rotorblattstern nachgelegt. Der erste 83,5 m lange Einzelflügel stammt von der dänischen Firma SSP Technology und ist für die 7-MW-Offshoreanlage von Samsung gedacht.
Damit überholt der südkoreanische Konzern die gerade aufgestellten Prototypen von Siemens (154 m) und Alstom (150 m). Auf dem Meer sollen die gigantischen Flügel mehr Ertrag bringen und so die hohen Investitions- und Wartungskosten drücken.
Trend in der Windenergiebranche: kleine Generatoren, lange Rotorblätter
Die gleiche Rechnung zeichnet sich an Land ab. Hier liegt der Schwerpunkt auf kleineren Generatoren und großen Rotoren, um die Ernte im Teillastbereich zu optimieren. Für das Binnenland hat REpower eine Rotordurchmesser von 122 m angekündigt. Vestas will die Spannweite gar auf 126 m ausdehnen.
Allerdings machen schwere und windanfällige Rotoren den Aufbau nicht einfacher. Stand der Technik ist es bisher, vormontierte Rotorsterne in einem Rutsch hochzuziehen und zu montieren. Das geht aber nur bei Windgeschwindigkeiten von bis zu 6 m/s.
Offshore greifen einige Hersteller auch auf die sogenannte Bunny-Ears-Methode zurück. Dafür werden im Hafen zwei Flügel an der Gondel vormontiert und auf See das dritte Blatt separat installiert.
Die Einzelblattmontage ist eine dritte Option. Während diese Technik im Offshore-Segment kaum erprobt ist, gehört sie an Land schon zum Repertoire. Ein Beispiel ist Enercon. Das Unternehmen hat mit Traggurten ein eigenes System entwickelt. Weil sich bei Enercons getriebelosen „Direct Drive“-Systemen im Gegensatz zu Anlagen mit Getriebe die Nabe nicht ohne funktionierenden Stromanschluss bewegen lässt, nutzt Enercon laut Pressesprecher Felix Rehwald einen Ballastarm zum Weiterdrehen.
Lange Rotorblätter rücken Einzelblattmontage in den Fokus
Die Auricher haben ihre Einzelblattmontage konzeptionell optimiert. „Es gibt jetzt feste Anschlagpunkte in den Blättern, die sich hinterher verschließen lassen und einen automatischen Entriegelungsmechanismus für das Traggeschirr. Vorher musste dieses noch per Mannkorb entfernt werden“, erklärt Rehwald.
Deutliche Vorteile sieht Enercon bei den Faktoren Zeit und Kosten. Schließlich können so kleinere Kräne eingesetzt werden, die billiger und leichter zu bekommen sind als großes Geschirr. Zudem sind die Wetterfenster mit bis zu 12 m/s größer.
„Es hängt immer vom Standort und dem vorhandenen Platz ab. Wenn man den kompletten Stern ziehen kann, dann ist der Aufbau schneller abgeschlossen. Das ist bei den neuen Anlagenklassen und den auftretenden Windlasten aber kaum noch möglich“, erläutert Torsten Höllwarth, Projektmanager bei Juwi.
Virulent ist das Thema in Waldgebieten. Diese sollen vermehrt für neue Windparks genutzt werden. Bei einer üblichen Sternmontage müssten dort jedoch viele Bäume zur Vormontage erst gefällt und anschließend neu gepflanzt werden.
„Um die Eingriffe möglichst gering zu halten, nutzt Nordex seit Kurzem eine Einzelblatt-Travese. Sie hat zudem den Vorteil, dass nur noch ein Kran für die Errichtung notwendig ist“, erläutert Felix Losada, Unternehmenssprecher des Windkraftanlagenherstellers.
Auch offshore geht es ums Sparen. Die Errichterschiffe sind so ausgelegt, dass sie mehrere Anlagen übernehmen und auch errichten können. Schwierig wird dieses Unterfangen mit Rotorsternen, da sie sich nicht beliebig übereinanderstapeln lassen. Also müssten teure Leerfahrten oder zusätzliche Transporte auf Pontons in Kauf genommen werden.
Gegen den Rotorstern für die Offshore-Montage sprechen zudem der größere Flächenbedarf an den Kaikanten sowie Transportrestriktionen. In vielen Basishäfen könnten die Errichterschiffe mit ihrer überhängenden Fracht erst dann auslaufen, wenn sie den übrigen Schiffsverkehr nicht behindern.
Zum ersten Mal hatte Vestas im großen Stil das Einzelblattkonzept 2010 beim englischen Offshore-Windpark Thanet erprobt und die 100 Anlagen im Rekordtempo aufgebaut. Für den Transport der Blätter hatten die Ingenieure ein Stapelsystem für 27 Rotorblätter entwickelt. So konnte das eingesetzte Spezialschiff „MPI Resolution“ neun Anlagen samt der Rotorblätter laden und aufbauen.
„Es hat viel Zeit gespart, weil das Schiff nicht zwischen der Baustelle und dem Hafen pendeln musste. Das machte es möglich, jeweils neun Anlagen in sechs oder sieben Tagen aufzubauen“, schwärmt Jesper Fyhn Friis, Installationsmanager bei Vestas.
Auf den Zug springen viele Hersteller auf. Das notwendige Werkzeug kommt bislang überwiegend von Liftra ApS, einem dänischen Spezialisten für Hebewerkzeuge. „Nachdem wir 2010 das erste Werkzeug verkauft hatten, ziehen die restlichen Hersteller jetzt sehr schnell nach“, berichtet Jörg Richter von Liftra.
„Blade Dragon“ und „Blade Yoke“ erleichtern Montage langer Rotorblätter
Mit dem „Blade Dragon“ und dem „Blade Yoke“ wurden zwei Montagewerkzeuge patentiert. Beide lassen sich vom Boden aus bedienen und per Kamera überwachen. Die elektrischen und hydraulischen Systeme sind autark und jeweils redundant ausgelegt.
Welches der Werkzeuge zum Einsatz kommt, „hängt davon ab, ob sich die Nabe auch ohne Stromversorgung frei drehen und arretieren lässt. Wenn das geht, dann lassen sich die Blätter jeweils in waagerechter Position hochziehen und nacheinander auf 30 Grad mit dem
‚Blade Joke‘ montieren, wegen der Lasten aber auf keinen Fall vertikal“, erklärt Richter.
Diese flexible Lösung kostet rund 400 000 € je Werkzeug. Für Anlagen ohne drehbare Nabe ist der „Blade Dragon“ konstruiert. Er liegt preislich zwischen 1,5 Mio. € und 2,25 Mio. € „Es ist das bislang einzige Werkzeug, dass Rotorblätter um bis zu 330 Grad vertikal in der Luft drehen und aus jeder Position in die Nabe stecken kann“, sagt Liftra-Sprecher Richter.
Wichtig für Kunden ist der Nachweis, dass die Technik durch die auftretenden Lasten nicht leidet. Mit dem 17 m langen und 55 t schweren „Blade Dragon“ hat beispielsweise Areva Wind sechs Monate lang auf Nabenhöhen von 100 m und 120 m geübt. Eingesteckt werden die Blätter immer auf 6, 10 und 14 Uhr.
„Wir können noch bei 12 m/s installieren und brauchen für ein Blatt gut dreieinhalb Stunden. Diese Zeiten lassen sich aber noch verbessern. Sollte das Wetter umschlagen, passiert auch nichts, wenn nur ein oder zwei Blätter in der Nabe sind. Die sichere Montage ist durch Zertifizierungen nachgewiesen“, erläutert Mathias Müller, Projektleiter bei Areva.
Auch Areva hofft, mit der Einzelblattmontage die Logistikkosten zu drücken. Skeptischer ist Hendrik Stiesdal, Technologiechef von Siemens Windpower. Bisher ist die Einzelblattmontage Offshore nur bei Projekten mit sehr restriktiven Windbedingungen eine Option. „Offshore nutzen wir normalerweise die Sternmontage. Sie braucht weniger Zeit als die Installation einzelner Blätter und reduziert die Einsatzzeiten der teuren Errichterschiffe. Das ist der Schlüssel bei allen Offshore-Aktivitäten.“
Ein Beitrag von: