Bosch eröffnet eine der modernsten Chipfabriken der Welt
Endlich ist es so weit: Die Chipfabrik der Zukunft ist fertig. So nennt sie zumindest Bosch. Tatsächlich hat das Werk in Dresden einiges zu bieten. Über eine Milliarde hat der Bau gekostet, im Juli soll es losgehen mit der Serienproduktion der 300-Millimeter-Halbleiter. Die Fertigung ist hochmodern.
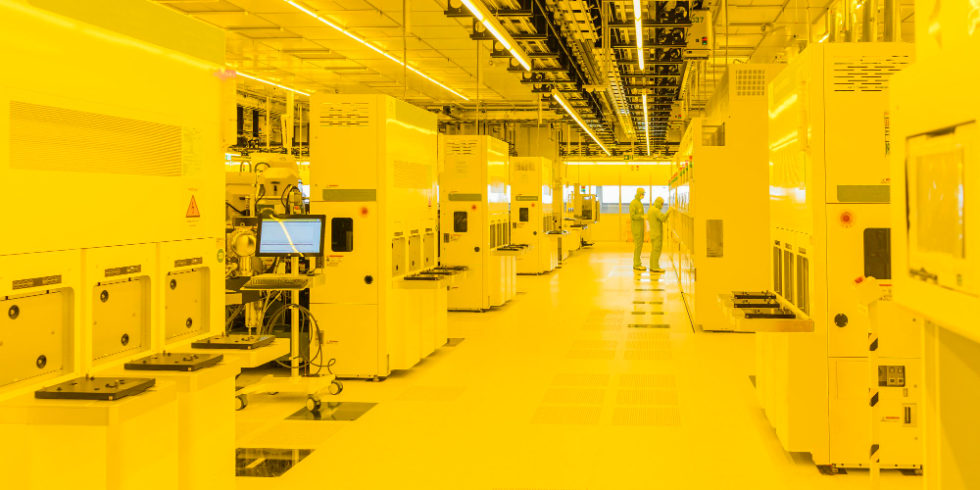
Im Reinraum der neuen Chipfabrik werden sämtliche Daten gesammelt, um eine vernetzte Produktion zu ermöglichen.
Foto: Robert Bosch GmbH
Büro und Fertigung der neuen Chipfabrik von Bosch nehmen eine Fläche von etwa 72.000 Quadratmetern ein. Bis zu 700 Mitarbeiter sollen hier Halbleiterelemente herstellen. Bei so einer Größenordnung drückt der Chef natürlich nicht einfach nur auf den Startknopf, damit es läuft – schon seit Beginn des Jahres werden die ersten Siliziumchips in Dresden produziert. Gedacht sind sie in erster Linie für die Automobilbranche. In einem mehrstufigen Prozess sind die Produktionsschritte immer komplexer geworden. Jetzt ist die Chipfabrik offiziell eröffnet und die Testphase damit beendet.
Denn im Juli soll es losgehen mit der Serienproduktion, die offizielle Eröffnung des Werks in Dresden ist bereits am 7. Juni – Bosch sucht noch in vielen Bereichen Mitarbeiter, unter anderem spezialisierte Ingenieurinnen und Ingenieure. Das Team erwartet ein hochmoderner Arbeitsplatz, wenn man Bosch glaubt: Das Unternehmen nennt das neue Werk selbst die „Chipfabrik der Zukunft“, und das hat gute Gründe.
Durchgängige Industrie 4.0 Lieferkette bei der HEGGEMANN AG – MES macht´s möglich
Bosch praktiziert in seiner Chipfabrik die vernetzte Produktion
Bosch reagiert mit der Chipfabrik auf die rasant steigende Nachfrage nach Halbleitern – und Dresden hat sich als Standort einen Namen gemacht – ist nachgerade zu einer Art Marke geworden. Die sächsische Großstadt samt Umland ist als Zentrum für Mikroelektronik bekannt, der Spitzname „Silicon Saxony“ in Anlehnung ans Silicon Valley hat sich etabliert. Die Namensgebung beruht auf einem überraschenden Ereignis. Welche Herausforderungen auf Ingenieure und Ingenieurinnen warten, hören Sie in dieser Podcast-Folge von „Technik aufs Ohr“. CEO des Silicon Saxony e.V. Frank Bösenberg ist zu Gast:
Hier wird Ihnen ein externer Inhalt von Podigee angezeigt.
Mit der Nutzung des Inhalts stimmen Sie der Datenschutzerklärung
von youtube.com zu.
In der neuen Fabrik sind mehr als 100 Maschinen und Anlagen vollständig miteinander vernetzt. Das gelingt durch 300 Kilometer Kabel, die alle relevanten Informationen zu einer Datenzentrale leiten. Für jede Maschine werden bis zu 1.000 Datenkanäle erfasst, und das in Echtzeit. Bosch beschreibt diese Stufe der Digitalisierung als „eine der größten Stärken“ der neuen Chipfabrik. Ein paar Zahlen können die Datenmengen verdeutlichen, mit denen das Unternehmen die Fertigung automatisiert: Würden die Informationen ausgedruckt, bräuchte man dafür etwa 500 Textseiten pro Sekunde. Das wären mehr als 42 Millionen Seiten pro Tag – das Papier wöge etwa 22 Tonnen. Der Sinn dieses intensiven Datenaustauschs besteht vor allem darin, zu jedem Zeitpunkt ermitteln zu können, wo sich die einzelnen Wafer in der Fertigung gerade befinden und wie die folgenden Produktionsschritte aussehen. Der Transport ist natürlich ebenfalls automatisiert.
Bosch verbindet künstliche Intelligenz mit dem Internet der Dinge
Die Akürzung AloT wird in Zukunft immer wichtiger werden. Sie ist zusammengesetzt aus AI (Artificial Intelligence = Künstliche Intelligenz) und IoT (Internet of Things = Internet der Dinge). Bosch verbindet in seiner Dresdener Chipfabrik beides miteinander, um die Produktion dank entsprechender Algorithmen immer weiter verbessern zu können. Praktisch heißt das: Die enormen Datenmengen, die bei der Wafer-Fabrikation gesammelt werden, wertet eine künstliche Intelligenz aus. Sie soll selbst winzige Fehler entdecken und die Prozesse entsprechend anpassen. Außerdem sollen die KI-Algorithmen laut Bosch vorhersagen können, ob und wann eine Fertigungsmaschine oder ein Roboter gewartet oder nachjustiert werden muss. Dafür werden verschiedene Parameter herangezogen. Das könnte ein wesentlicher Fortschritt gegenüber der früher üblichen Vorgehensweise mit festgelegten Wartungsintervallen sein. Bosch will auf diese Weise erreichen, dass Maschinen überprüft werden, bevor es zu Problemen kommt.
Die Chipfabrik hat einen digitalen Zwilling
Für einzelne Produktionsprozesse werden häufig digitale Zwillinge eingesetzt, die beispielsweise die Arbeitsweise einer Maschine virtuell komplett simulieren können. Bosch ist für sein Halbleiterwerk einen Schritt weiter gegangen: Sämtliche Bereiche der Fabrik sowie alle relevanten Bauwerksdaten des Halbleiterwerkes wurden bereits während der Bauphase digital erfasst und in Form eines dreidimensionalen Modells visualisiert. Jetzt liegen auf dem Server Daten für über eine halbe Million 3D-Objekte. Sie betreffen nicht nur Maschinen und Fertigungsanlagen, sondern auch die Gebäude selbst, inklusive ihrer Infrastruktur, etwa Ver- und Entsorgungsanlagen, Kabeltrassen und Lüftungssysteme. Dieser umfassende digitale Zwilling soll es den Bosch-Experten erleichtern, Prozesse bei Bedarf zu verändern und sogar Umbauarbeiten zu simulieren.
Bosch hat seine Chipfabrik also vollständig auf die Industrie 4.0 ausgelegt. Da verwundert es nicht, dass die Mitarbeiter Daten auch über AR-Brillen (Augmented-Reality = virtuelle Realität) in der realen Fabrikumgebung eingeblendet bekommen und dass die Infrastruktur für den neuen Mobilfunkstandard 5G ebenfalls bereits vorhanden ist. All das kostet zwar ohne Frage eine Menge Energie, sorgt aber auch für mehr Effizienz. Außerdem hat Bosch für seine Chipfabrik auch die Klimaziele im Blick, etwa mit Ökostrom als wichtigem Energieträger.
Mehr lesen über Bosch:
Ein Beitrag von: