Internet der Dinge: Wie IoT der Industrie beim Energiesparen hilft
Auch wenn sich die Lage etwas entspannt hat: Hohe Energie- und Rohstoffkosten fressen die Margen von Unternehmen auf – oder gefährden gar deren Existenz. Ihre Prozesse müssen nachhaltiger und effizienter werden. Jetzt! Wir sagen, warum für die Industrie die digitale Performance der entscheidende Hebel dafür sein kann – und noch untereschätzt wird.
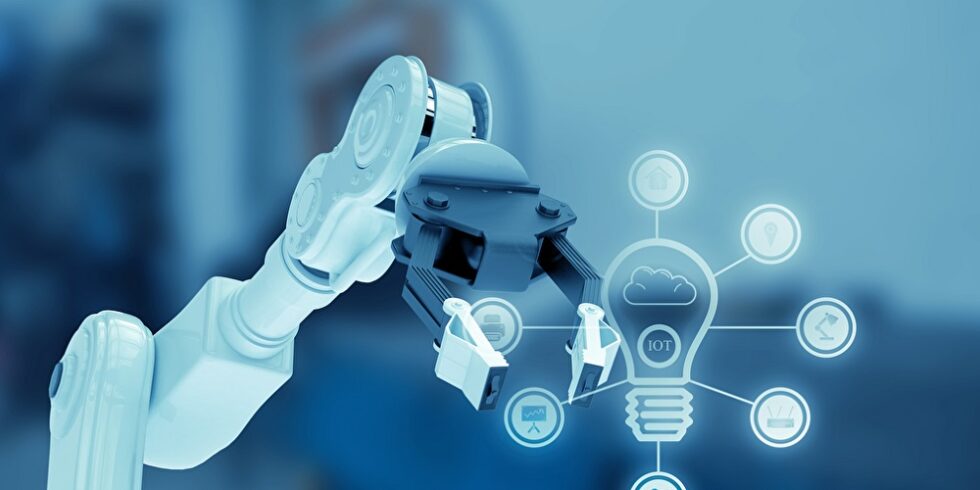
Das Internet der Dinge kann der Industrie beim Energiesparen helfen.
Foto: Panthermedia.net/WavebreakmediaMicro
Staatliche Entlastungspakete mögen für den Moment Linderung verschaffen, doch explodierende Energie- und Rohstoffkosten sind insbesondere für den industriellen Mittelstand hierzulande zu einem veritablen Problem geworden. Einem, das bleiben wird. Denn ein Zurück zu billiger Energie wird es nicht mehr geben. Unternehmen müssen also selbst dafür sorgen, ihre Verbräuche zu drosseln.
Warum Daten helfen, Rohstoffe und Energie zu sparen
Was viele dabei nicht auf der Rechnung haben: Die digitale Transformation kann dabei einen entscheidenden Beitrag leisten. Energieeffizienz ist einer der wichtigsten Treiber für die Einführung des Industrial Internet of Things (IIoT).
So ist in Fabriken der Energieverbrauch bestimmter Anlagen im Vergleich zu anderen überproportional hoch. Besonders diese gilt es, zu monitoren. Beispielsweise kann der Verbrauch von Kompressoren, Heizkesseln oder Notstromgeneratoren enorm sein. Und das abhängig von Betriebsanforderungen oder Umgebungsfaktoren wie der Außentemperatur. Allein daraus ergibt sich ein hohes Einsparpotenzial, wenn solche Anlagen stets am Betriebsoptimum gefahren werden. Wichtig ist zudem, den Maschinenpark möglichst vorausschauend zu warten, was nur möglich ist, wenn entsprechende Daten erhoben und analysiert werden.
Doch wie? Indem Maschinen einer Fabrik mit intelligenten Sensoren ausgestattet werden, die wiederum mit einer IIoT-Plattform wie ThingWorx des Technologieunternehmens Parametric Technology Corporation (PTC) kommunizieren. Mit der Software lassen sich auf Geräteebene bestimmte Muster beim Energieverbrauch identifizieren. Außerdem sind durch die Energie- und Ressourcenmanagementlösung exakte Einblicke in den Gesamtenergieverbrauch möglich. Auf diese Weise lassen sich wichtige Erkenntnisse zu übermäßigem Energiekonsum gewinnen, so dass gezielt gegengesteuert werden kann.
Das ist die Basis, um auf Anlagen- und Maschinenebene Energie zu sparen. Durch eine verbesserte digitale Performance mit zentraler Plattform zur Datenerfassung, -bereinigung, -orchestrierung und -auswertung lassen sich zudem Abfälle reduzieren, die Materialeffizienz erhöhen und der Emissionsausstoß verringern.
Denn durch Digital Performance Management (DPM) werden Ursachen für Ausschuss und Ertragsverluste, wie etwa Maschinenprobleme oder menschliches Versagen, aufgespürt. Mit diesen Informationen können Produktionsteams derartige Hindernisse abstellen und die Performance erhöhen. Damit werden direkt Energie sowie Ressourcen geschont und zugleich Abfälle vermieden.
Wie sich Energie smart nutzen lässt
Durch den Einsatz modernster Methoden zur Kombination und Analyse von Energieverbrauchsdaten mit Informationen aus dem Manufacturing Execution System (MES) und anderen wichtigen Anwendungen können zudem Produktionspläne optimiert werden, indem sie exakt mit Zeiten niedrigerer Energiekosten oder höherer Verfügbarkeit von Erneuerbaren abgestimmt werden.
Auch teure Spitzenlasten lassen sich auf diese Weise vermeiden. Denn eine einzelne Verbrauchsspitze kann die Energiekosten für ein ganzes Jahr deutlich in die Höhe treiben. Solche Analysen lassen sich auch nutzen, um autonome Betriebsprofile zu entwickeln: So können beispielsweise mit Sensoren ausgestattete Maschinen erkennen, wann sie eingeschaltet werden und in Betrieb bleiben müssen und wann sie durch Abschaltung Energie sparen können.
So lässt sich selbst produzierte Energie am besten nutzen
Ähnliche Ansätze können von Unternehmen angewandt werden, die eigene Anlagen für erneuerbare Energien auf ihrem Firmengelände nutzen, zum Beispiel Photovoltaikmodule oder Windturbinen. Fortschritte in der Batterietechnologie ermöglichen es dabei, intelligent lokal erzeugten Strom zu speichern und zu nutzen. Hierbei ist ebenfalls IIoT-Technologie hilfreich. Denn Solarmodule, Windturbinen und Batteriespeicher sind wie jede andere intelligente Fabrikanlage zu betrachten.
Daten, die sie über ihre Aktivitäten, ihren Status und ihren Zustand übermitteln, lassen sich sammeln, verwalten und analysieren. Auch hier transferieren IIoT-Plattformen wie ThingWorx all diese Daten aus verschiedenen Quellen zu einem einzigen, konsolidierten Ort, wo sie mit anderen Informationen kombiniert und von den Nutzern über Dashboards und Alerts eingesehen werden können.
Auf diese Weise können Betriebe nicht nur die Nutzung der Anlagen optimieren, die sie zur Energieerzeugung vor Ort einsetzen, sondern auch bestmöglich entscheiden, wann und wofür sie diese Energie nutzen. Hinzu kommt, dass die Industrie in den nächsten Jahren Klimaschutzziele erreichen muss. Auch hier können die durch digitale Transformation der Produktion erreichten Energie- und Ressourceneinsparungen dazu beitragen, nachhaltiger und klimaschonender zu wirtschaften.
Ein Beitrag von: