Ultraschallsystem aus dem 3D-Drucker lässt Knochen schneller heilen
Sie ist ein Wunderding, die neue Schiene für Knochenbrücke des türkischen Designers Deniz Karasahin: Sie fördert per täglicher Ultraschalldosis die schnellere Heilung, ist leicht, luftig und beseitigt sogar lästige Begleiterscheinungen von Gipsschienen wie das ständige Jucken. Und die Schiene aus dem 3D-Drucker sieht auch noch so gut aus, dass sie einen Designpreis erhalten hat.
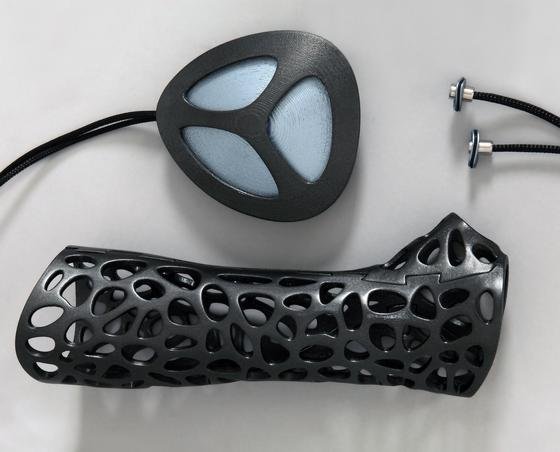
Der Designer Deniz Karasahin hat ein System aus Schiene, Sensoren und Ultraschallbehandlung entwickelt, das Knochenbrüche um 40 Prozent schneller heilen soll.
Foto: A' Design Award and Competition
3D-Drucker sind längst kein Spielzeug mehr: Das zeigt ein neues Projekt des Industriedesigners Deniz Karasahin. Der Inhaber des Dk Desıgn Studios mit Standorten in Izmir und Paris hat ein Verfahren entwickelt, Knochenbrüche auf angenehmere Weise als bisher zu schienen und darüber hinaus noch fast 40 Prozent schneller heilen zu lassen. Ein maßgebliches Werkzeug dabei: ein 3D-Drucker.
Ultraschallsensoren lassen sich direkt an löchrige Schiene anschließen
Um das Knochenwachstum anzuregen, beschießt Karasahin die Bruchstelle täglich etwa 20 Minuten mit Ultraschall. Diese kurze Zeit reicht aus, um die Knochenzellen ausreichend anzuregen – vorausgesetzt, die Sensoren des Lipus genannten Systems liegen genau über der Bruchstelle direkt auf der Haut.
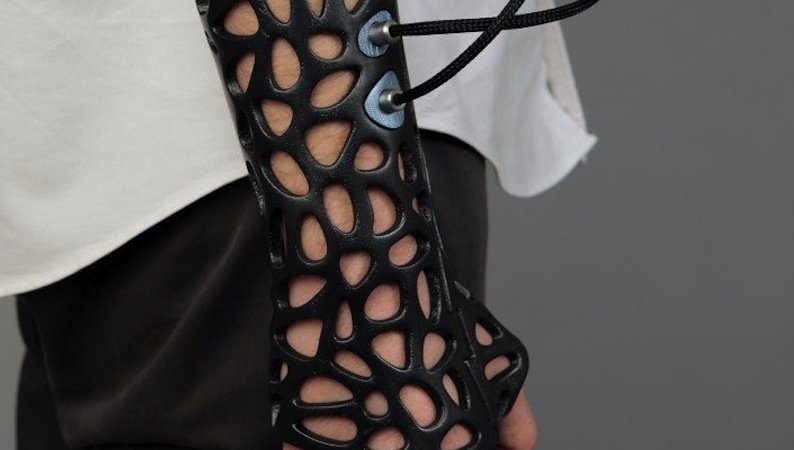
Schiene und Ultraschallsonden hat ein 3D-Drucker aus demselben Material gefertigt. Die Sonden lassen sich während der zwanzigminütigen Behandlungen einfach auf die Schiene aufstecken – genau über der Bruchstelle.
Quelle: A' Design Award and Competition
Genau hier befand sich bei ähnlichen Versuchen bisher der Knackpunkt: Wenn ein Bruch auf konventionelle Art geschient wird, ist die Haut von Zellstoff, Gips oder Kunststoff umschlossen – auf jeden Fall nicht mit Sensoren erreichbar.
Schiene und Knochenstimulator stammen aus dem 3D-Drucker
Deniz Karasahin hat dieses Problem jetzt mit dem Projekt Osteoid gelöst. Die neuartige Schiene, die nach der Knochensubstanz benannt wurde, umhüllt den verletzten Körperteil und stützt ihn. Sie bedeckt dank der filigran wirkenden Struktur aber nur so viel Haut wie unbedingt notwendig. Genau über dem Bruch sind die Löcher in der Schiene exakt auf die Ultraschallsensoren angepasst, so dass sie per Adapter bequem eingesetzt werden können.
Jede Osteoid-Schiene wird individuell angepasst. Möglich macht das ein 3D-Body-Scanner, der die verletzte Region aufnimmt. Die so gewonnenen Daten werden mithilfe einer Modelliersoftware verarbeitet. Die Größe der Schiene und die genaue Form richten sich dabei nach der jeweiligen Art der Verletzung.
Zum Schluss werden zusätzlich zu den Adaptern für die Ultraschallsonden Luftlöcher sowie ein Mechanismus zum Öffnen und Verschließen im Computer hinzugefügt, bevor die Schiene aus lebensmittelechtem Material gedruckt wird – in zwei Teilen, die wie Puzzleteile ineinandergreifen.
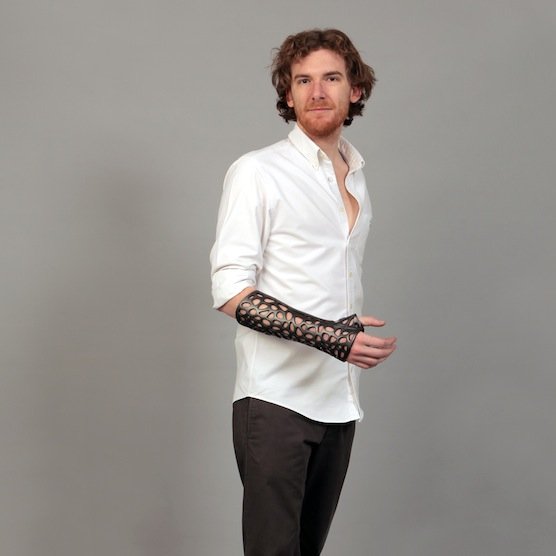
Für seine Schiene aus dem 3D-Drucker erhielt Deniz Karasahin den A’Design Award. Die Gipsalternative soll auch in verschiedenen Farben erhältlich sein.
Quelle: A' Design Award and Competition
„Die größte Herausforderung war es bei dem Projekt, einen voll funktionsfähigen Schließmechanismus zu entwickeln”, erklärt Deniz Karasahin. „Er musste stark genug sein, um das verletzte Körperteil zu schützen und einfach genug, um nicht die medizinisch sinnvolle Form zu beeinträchtigen.“
Ein Detail im Produktionsprozess verrät zudem, dass der Erfinder des Systems ein preisgekrönter Designer ist: Das Lipus Knochenstimulator-System wird mit dem 3D-Drucker aus demselben Material gefertigt wie die Schiene, damit beide Elemente auch optisch zusammenpassen.
Nerviges Jucken eines typischen Gipsverbands gibt es nicht
Ganz nebenbei löst Karasahin mit Osteoid ein Problem, das Generationen von Gipsträgern genervt hat: Konventionelle Verbände aus Gips oder ähnlichen Materialien fangen schnell an zu jucken, entwickeln oft einen unangenehmen Geruch und vertragen meistens kein Wasser – alles Dinge, die auf die luftige Kunststoffhülle aus dem 3D-Drucker nicht zutreffen. Außerdem gibt es sowohl Schiene als auch Stimulator in vielen verschiedenen Farben – möglich, dass manch ein Träger die Schiene gar nicht mehr ablegen will.
Das Konzept, das im Rahmen einer viermonatigen Studie in der Türkei entstand, ist mit dem A’Design Award in der Kategorie „3D Printed Forms and Products Design“ ausgezeichnet worden. Der Award ist der nach Angaben des Veranstalters weltweit größte Wettbewerb für Designs, Produkte und Konzepte.
Ein Beitrag von: