3D-Drucker fertigt Mini-Gegenstände aus Glas Mikrometer genau
So genau hat noch kein Drucker der Welt mit Glas gearbeitet: Mini-Burgen und kleine Bretzeln aus Glas mit einer Auflösung im Mikrometerbereich haben Ingenieure des KIT mit einem neuartigen Verfahren hergestellt. Doch den Forschern geht es nicht um Glas-Gimmicks, sondern um filigranste Bauteile für Computer der Zukunft, die mit Licht rechnen.

Mini-Burg aus Glas, mit höchster Präzision mittels 3D-Drucker gefertigt: Die gläsernen Strukturen erreichen eine Auflösung im Bereich weniger Mikrometer.
Foto: NeptunLab/KIT
Die Forscher des Karlsruher Instituts für Technologie (KIT) sind nicht die ersten, die Glas mit Hilfe eines 3D-Druckers verarbeiten. Doch bisherige Geräte kämpfen mit den Nachteilen der Düsentechnik. Die Objekte werden oft sehr ungenau, die Oberfläche rau, das Material porös. Oft entstehen Hohlräume, welche die Stabilität gefährden.
3D-Drucker druckt auf tausendstel Millimeter genau
Das Verfahren der KIT-Forscher hat diese Nachteile nicht. Ihnen sind so filigrane Glasstrukturen gelungen, dass man damit sogar Bauteile für die Computer der Zukunft produzieren kann. „Wir stellen eine neue Methode vor, die eine Innovation in der Materialprozessierung bedeutet“, sagt KIT-Maschinenbauingenieur Bastian Rapp, der das Verfahren entwickelt und im Magazin Nature vorgestellt hat. „Das Material des gefertigten Stücks ist hochreines Quarzglas mit seinen entsprechenden chemischen und physikalischen Eigenschaften.“
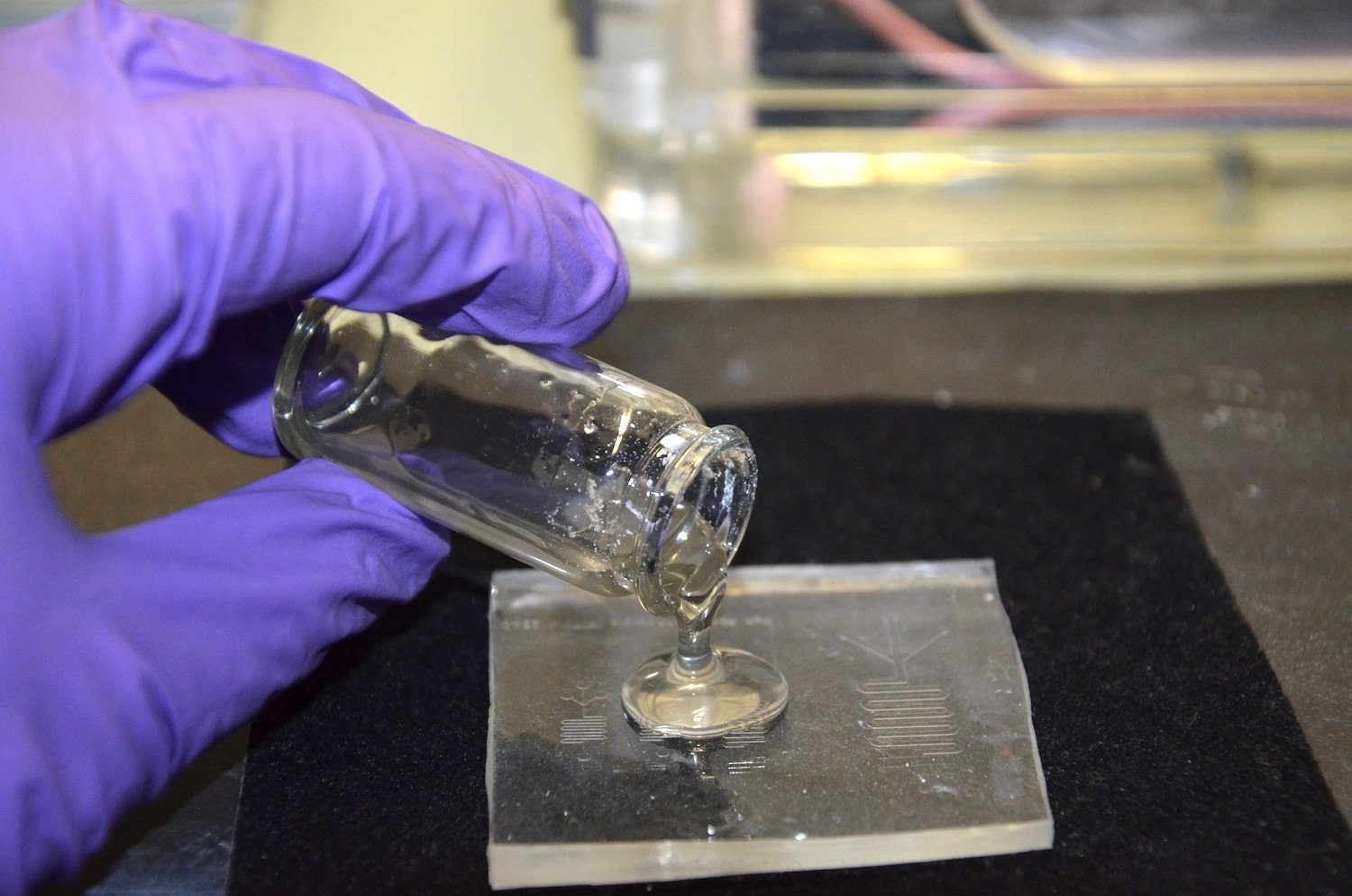
Herzstück der Technik ist das sogenannte Liquid Glas – eine dickflüssige Mischung aus Silikat-Nanopartikeln und Kunststoff.
Quelle: NeptunLab/KIT
Die Druckauflösung ist bislang unerreicht: Die gläsernen Strukturen weisen Auflösungen im Bereich weniger Mikrometer auf – ein Mikrometer entspricht einem Tausendstel Millimeter. „Die Abmessung der Strukturen kann aber im Bereich mehrerer Zentimeter liegen“,
3D-geformtes Glas für Computer der Zukunft
Bislang haben die Forscher Mini-Bretzeln und kleine Burgen aus Glas gedruckt. Prestige-Objekte. In Zukunft könnte 3D-geformtes Glas, das transparent, hitzebeständig und säureresistent ist, in der Datentechnik zum Einsatz kommen. „Die übernächste Generation von Computern wird mit Licht rechnen, das erfordert komplizierte Prozessorstrukturen“, sagt Rapp. „Mit Hilfe der 3D-Technik könnten beispielsweise kleine, komplexe Strukturen aus einer Vielzahl kleinster, unterschiedlich ausgerichteter optischer Komponenten hergestellt werden.“
Auch für die Medizintechnik ließen sich kleinste Analysesysteme aus Miniatur-Glasröhrchen fertigen. 3D-geformte Mikrostrukturen aus Glas könnten zudem in Brillen oder Kameralinsen zum Einsatz kommen.
Neues Verfahren mit höchster Präzision
Und wie funktioniert das neue Verfahren? Zum einen haben die KIT-Ingenieure am Drucker selbst gearbeitet, haben zudem ein neues Polymer entwickelt, das als Ausgangsmaterial dient, und setzen zudem einen Laser ein, der als Trockner arbeitet.
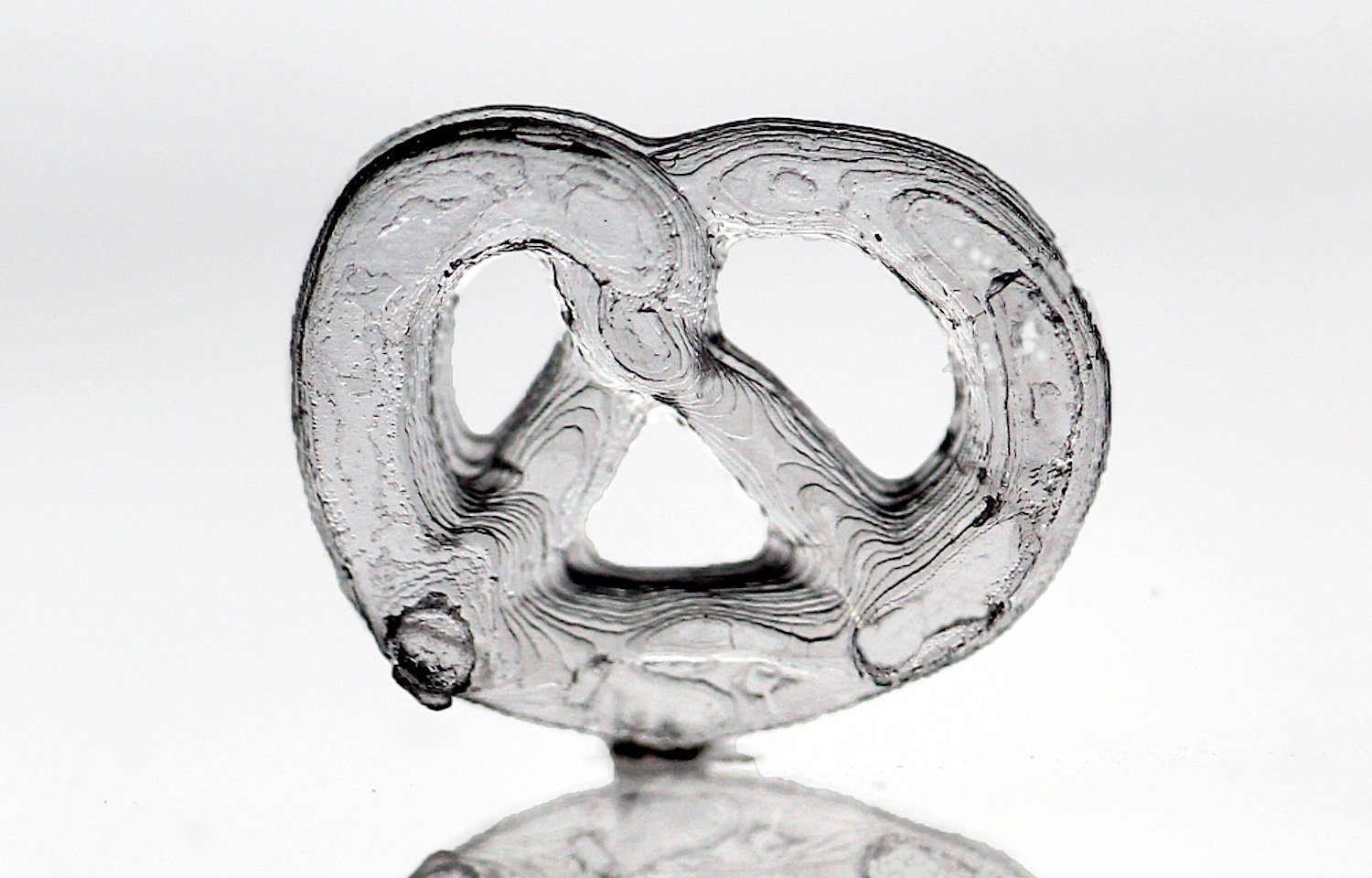
Glasbretzel aus dem 3D-Drucker: Solche Glasbauteile herzustellen, ist laut Forschern fast so einfach wie Kekse zu backen.
Quelle: NeptunLab/KIT
Aber der Reihe nach: Die Ingenieure mischen Nanopartikel hochreinen Quarzglases mit einer kleinen Menge flüssigen Kunststoffs und lassen diese Mischung durch Licht – mittels Stereolithografie – an bestimmten Stellen aushärten. Ein Laser bestrahlt die Oberfläche entsprechend der Kontur des Druckobjekts und härtet es zu einem festen Kunststoff aus.
Nach jeder Bestrahlung fährt die Bauplattform tiefer in das Bad – Schicht für Schicht, solange, bis das Objekt fertig ist. Der in dieser Glasstruktur noch eingemischte Kunststoff wird anschließend durch Erhitzen entfernt.
„Die Form ähnelt zunächst einem Sandkuchen, sie ist zwar geformt, aber instabil“, erklärt Rapp. „Deshalb wird das Glas in einem letzten Schritt gesintert, also so weit erhitzt, dass die Glaspartikel miteinander verschmelzen.“ Übrig bleibt das fertige Objekt aus hochreinem Quarzglas. Glasbauteile zu strukturieren sei fast so einfach wie Kekse zu backen, schreiben die Forscher.
Zu sehen ist die Technik auch auf der Hannover Messe 2017, die vom 24. bis 28. April stattfindet (Halle 2, Stand B16).
Weitere interessante Berichte zur Hannover Messe finden Sie hier.
Ein Beitrag von: