60 Jahre alte Fräsmaschine bekommt digitalen Zwilling
Forschende der Kaiserslauterner Technologie-Initiative „SmartFactory KL“ überführen einen spanenden Oldie in die Neuzeit. Das Zauberwort: Retrofitting.
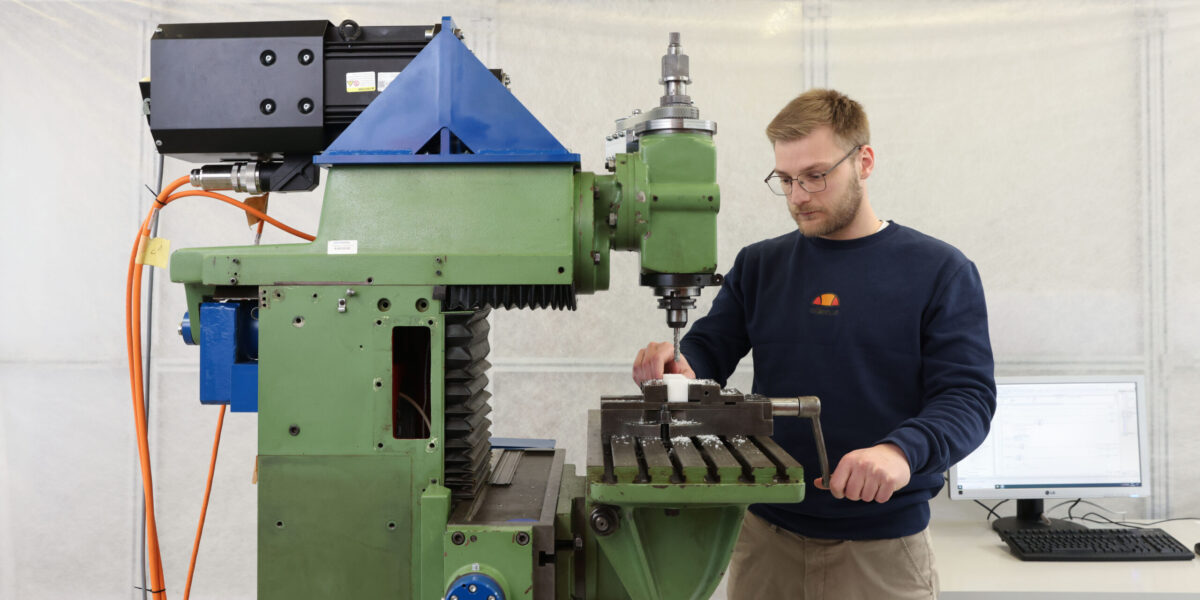
Andreas Wagner von der RPTU Kaiserslautern-Landau an der alten, jetzt modernisierten Fräsmaschine. Er liebäugelt schon länger mit der Idee des Retrofittings.
Foto: www.alexandersell.de
Grüner Schlaglack und 1,5 t schwer – eine Fräsmaschine, wie sie hundertfach in deutschen Unternehmen installiert wurde. Doch bei dem Exemplar, das aktuell in Kaiserslautern arbeitet, ist einiges anders. Der Originalhersteller, die Friedrich Korradi GmbH, würde ihr Produkt kaum wiedererkennen. Es wurden nämlich einige Hardwareumbauten vorgenommen. Außerdem wurde ein Digitaler Zwilling erstellt. Ergebnis: höhere Produktivität, verbesserte Präzision.
Die Maschine soll skillbasiert arbeiten
Der Kopf hinter dieser Aktion ist Andreas Wagner von der RPTU Kaiserslautern-Landau. Er liebäugelt schon länger mit der Idee des Retrofittings. Seine Idee: die Maschine so umzurüsten, dass sie skillbasiert arbeiten kann. Er selbst promoviert zu dem Thema Skills und sieht Retrofitting als günstige Option, um neueste Technologien mit alten Maschinen zu verbinden. „Viele Unternehmen nutzen die Möglichkeiten von Industrie-4.0-Technologien nicht, weil sie denken, sie müssen dann neue Maschinen anschaffen“, erklärt er. „Ich will zeigen, dass das nicht richtig ist. Die Digitalisierung kann überall Einzug halten und ihre effiziente Wirksamkeit entfalten.“
Der digitale Zwilling plant die Trajektorie

Dank digitalem Zwilling und einer CNC-Steuerung lassen sich Rechtecktaschen einfach umsetzen.
Foto: www.alexandersell.de
Die Maschine wurde mit Vorschubmotoren, einer CNC-Steuerung und einem digitalem Zwilling ausgestattet. Ihre Fähigkeiten sind als Skills aufrufbar, so zum Beispiel das Fräsen von Rechteck- oder Kreistaschen. Sie sind über eine einheitliche OPC-UA-Schnittstelle ansteuer- und parametrisierbar. Der digitale Zwilling kalkuliert vor Arbeitsbeginn unter anderem Kosten und Energiebedarf, plant die Trajektorie und prüft diese auf Kollisionen. Somit übernimmt er die Rolle eines CAM-Systems und gibt Informationen zurück, die z. B. zur Erstellung eines Angebots genutzt werden können. Der digitale Zwilling hilft somit, den gesamten Planungsprozess zu automatisieren und zu optimieren.
Zeitaufwendige Programmierarbeit wird eingespart
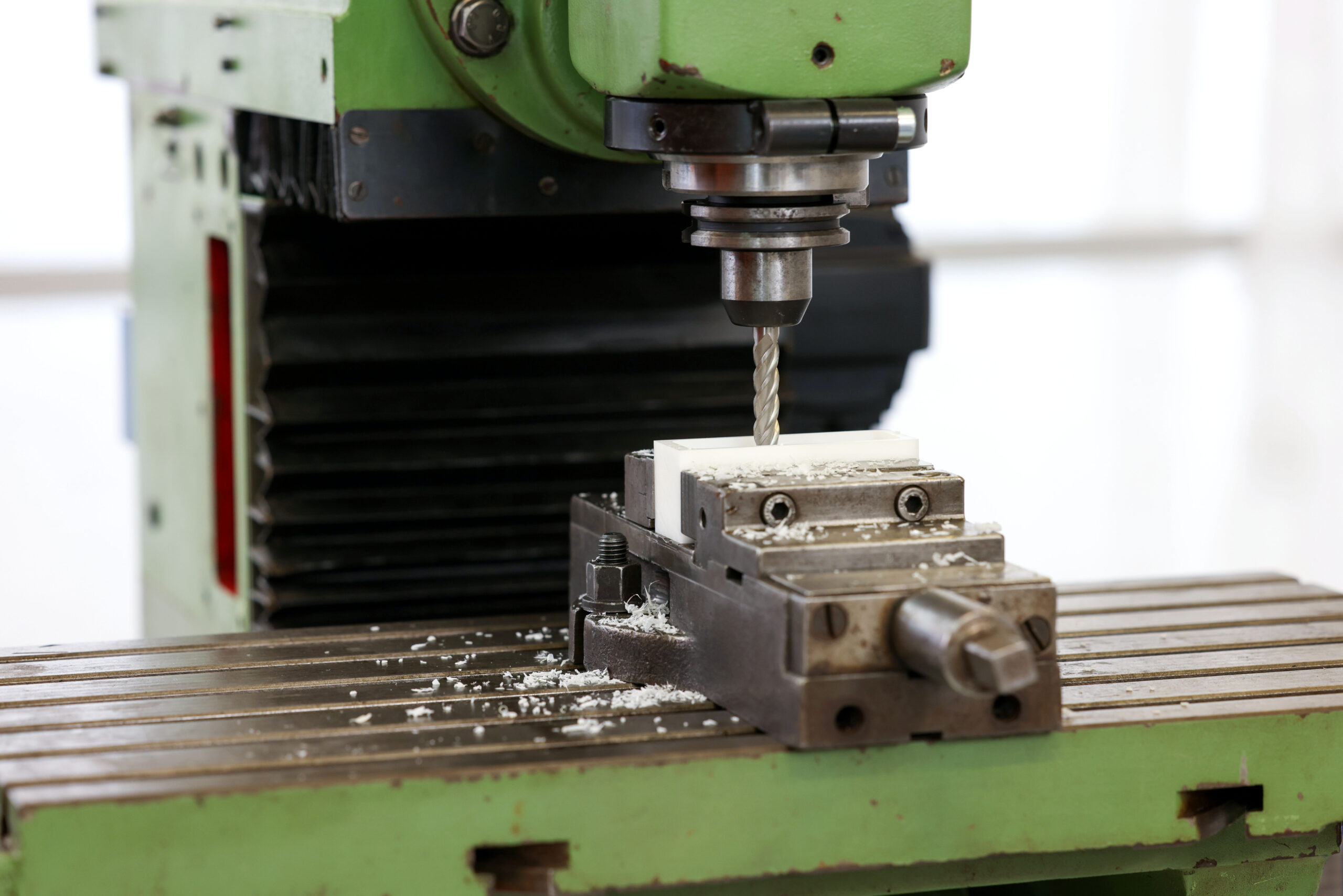
Alt, aber oho: Die „SkillMill“ ist über eine einheitliche OPC-UA-Schnittstelle ansteuer- und parametrisierbar.
Foto: www.alexandersell.de
Geometrische Features eines Bauteils können mithilfe aktueller Industrie-4.0-Paradigmen direkt aus dem CAD heraus gefertigt werden. Das spart zeitaufwendige Programmierarbeit. Bei der Suche nach passenden Maschinen für einen bestimmten Auftrag meldet sich die SkillMill wie auch alle weiteren Maschinen mit ähnlichen Fähigkeiten im Maschinenpark gemäß dem skillbasierten Ansatz automatisch zurück. Um sicher zu gehen, dass ein Skill mit seinen spezifischen Parametern ausführbar ist, führt der digitale Zwilling im Vorfeld einen Feasibility-Check durch, um die Machbarkeit des Arbeitsauftrags zu überprüfen.
Durch Retrofitting in die Zukunft transferiert
„Alte Maschinen stehen auch heute noch in Produktionshallen herum“, so Wagner. Das Beispiel zeigt, dass auch solche Maschinen durch ein Retrofitting in die Zukunft transferiert werden können. „Denkbar wäre, dass sie über den digitalen Zwilling in Datenräume eingebunden werden, wie sie mit Gaia-X oder Manufacturing-X angedacht sind“, erklärt Wagner weiter. „Dann könnte die Maschine ihre Skills dort anbieten und diese dann von anderen Unternehmen gemietet werden. So würde sie neue Aufträge bekommen und verstärkt genutzt werden.“ Durch den digitalen Zwilling kann die Maschine einen anfragenden Kunden exakt über die Arbeitsdauer, den CO2-Fußabdruck, den Energiebedarf oder den Preis informieren. So öffnet der digitale Zwilling das Tor zur Produktion der Zukunft.
Über die Technologie-Initiative SmartFactory KL e. V.
SmartFactory-KL bezeichnet ein Forschungs- und Industrienetzwerk, das auf drei Säulen ruht, einem Verein (Technologie-Initiative SmartFactory KL e. V. – SF-KL) und zwei wissenschaftlichen Forschungseinrichtungen („Innovative Fabriksysteme“ am DFKI und der Lehrstuhl „Werkzeugmaschinen und Steuerungen“ – WSKL – an der Rheinland-Pfälzischen Technische Universität Kaiserslautern-Landau). Seit 2019 fungiert Martin Ruskowski als organisatorische und inhaltliche Klammer. Er ist Vorstandsvorsitzender des Vereins, Leiter des DFKI-Forschungsbereichs und Inhaber des Lehrstuhls. Die SmartFactory-KL bringt Stakeholder aus Industrie und Wissenschaft in einem einzigartigen Industrie-4.0-Netzwerk zusammen, um gemeinschaftlich Projekte zur Fabrik der Zukunft zu entwickeln und umzusetzen. Auf dieser herstellerunabhängigen Demonstrations- und Forschungsplattform testen Wissenschaftler in Zusammenarbeit mit Industrievertretern innovative Fertigungstechnologien in einer realitätsnahen Fabrikumgebung.
Ein Beitrag von: