Dieter Schwarze: „64 Strahlquellen sind nicht wirtschaftlich!“
Dieter Schwarze ist Wegbereiter des selektiven Laserschmelzens und schildert Geschichte und Zukunft der Technologie.
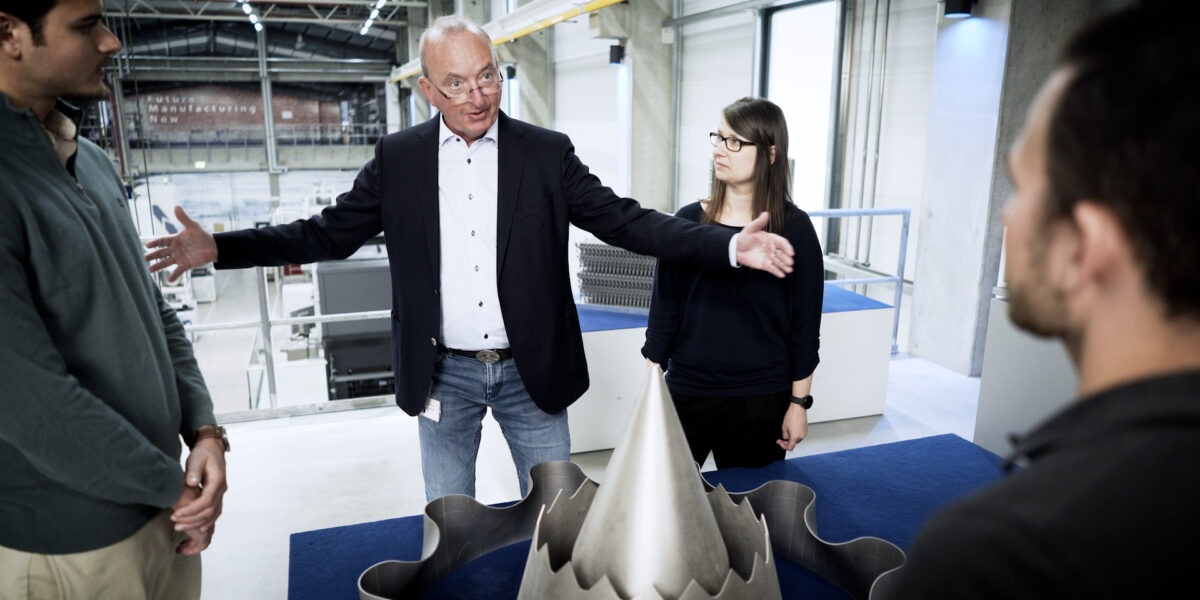
Großvolumige Metalldrucker – etwa für die Luft- und Raumfahrtfahrtindustrie – sind ein Steckenpferd von Dieter Schwarze (Bildmitte). Er hat das häufig verwendete SLM-Verfahren (Selective Laser Melting) maßgeblich vorangetrieben.
Foto: Nikon SLM Solutions AG
Inhaltsverzeichnis
Dieter Schwarze ist maßgeblicher Wegbereiter des industrieweit führenden Metalldruckverfahrens, des selektiven Laserschmelzens. Im Podcast – deshalb auch hier in Du-Form – hat er uns Geschichte und Zukunft der Technologie geschildert.
VDI nachrichten: Hallo Dieter, du hast das „Selektive Laserschmelzen von Metallen“ industrietauglich gemacht. Du hast dem Verfahren sogar einen Eigennamen verpasst: SLM. Bitte skizziere den langen Weg dorthin – gerne kurz.
Dieter Schwarze: 1989 haben mein damaliger Geschäftspartner und ich in einer Fachzeitschrift von der Stereolithografie gelesen. Wir waren zunächst begeistert. Unter der Firmierung Fockele & Schwarze wollten wir die Innovation, heute bekannt als SLA, nutzen. Uns störte aber schnell, dass die gedruckten Bauteile sehr spröde waren: Fielen sie vom Tisch, waren sie kaputt. Deshalb wünschten wir uns Objekte aus Metall.
Auf der Suche danach besuchten wir 1994 das Fraunhofer IFAM in Bremen. Drei Wissenschaftler hatten dort gerade die „Multiphase Jet Solidification“, kurz MJS, entwickelt. Dabei wurde ein kunststoffbasiertes Matrixmaterial, gefüllt mit Metallpartikeln, strangweise ausgebracht. Anschließend wurde das schichtweise aufgebaute Bauteil im Ofen entbindert und gesintert. Die Ergebnisse waren vielversprechend. Allerdings störte uns die Zweistufigkeit des Verfahrens. Also schauten wir uns nach Alternativen um. Fündig wurden wir 1995 am Fraunhofer ILT in Aachen. Die dortigen Experten schufen dichte Metallstränge ohne jeglichen Binder per Laser in einem Pulverbett. Uns war sofort klar: Das ist es! Dementsprechend haben wir all unsere Energie – und viel Geld – in die Weiterentwicklung der Idee investiert.
Das war also die Geburtsstunde des heute international als „Metal LPBF“, also Laser Powder Bed Fusion, bekannten Verfahrens?
Könnte man meinen … Das stimmt aber nicht ganz! Fairerweise möchte ich an Professor Jürgen Peterseim erinnern. Er hat in einem Forschungslabor von Krupp schon ab 1992 an einem Prototyping-Verfahren für Metallkomponenten gearbeitet. Sein Team hat damals eine Art Sandkiste, gefüllt mit Metallpulver, unter einem Infrarotlaser hin- und herbewegt. Ergebnis waren metallische Strukturen. Erstaunlicherweise wurden die Forschungen irgendwann eingestellt. Rückblickend kann ich sagen: Schade für Krupp, Glück für uns! Als wir Professor Peterseim Ende der 90er-Jahre von unseren Arbeiten erzählten, war er hellauf begeistert.
Dieter Schwarze: „Laserbasierte Verfahren werden noch viele Jahre führend bleiben“
Ist es nicht trotzdem langsam an der Zeit, dass das SLM-Verfahren abgelöst wird von jüngeren Alternativen?
Du kannst dir sicher sein: Mein heutiger Arbeitgeber, die Nikon SLM Solutions AG, beobachtet den Wettbewerb minutiös. Die Ergebnisse dieser Marktforschung interpretiere ich persönlich so: Die laserbasierten Verfahren werden noch viele Jahre führend bleiben.
Das ist in meinen Augen eine steile, mutige These …
Ok, zugegeben: Je nach Bauteilanforderungen kann das Binder-Jet-Printing, also das eben skizzierte, zweistufige und inzwischen natürlich modernisierte Verfahren, interessant sein. Aber es hat immer noch Defizite: Die Bauteildichte ist nicht so gut und die geometrische Freiheit ist eingeschränkt. Außerdem kann man damit kein Aluminium verarbeiten. Warum erwähne ich das? Weil Aluminium aktuell das am häufigsten gedruckte Metall ist.
Wie geht es denn mit der SLM-Technologie weiter?
Aktuell gibt es Bemühungen, den Bauprozess effektiver zu machen. Das maßgebliche Ziel: die Stückkosten senken. Die jüngsten Treiber dieser Entwicklung sitzen in China. Deren Rezept: mehr Laser! Der aktuelle Gipfel: stolze 64 Strahlquellen.
Das klingt für mich erst einmal sinnvoll. Zumal Nikon SLM Solutions mit der „NXG XII 600“ vor Jahren eine ähnlich klingende Kampfansage gemacht hat: In eurer Maschine sind gleich ein Dutzend Laser mit je 1 kW Leistung integriert …
Deine skeptischen Gedanken kann ich nachvollziehen. Um sie auszuräumen, müssen wir ins Detail gehen. Fakt ist: Mit 64 Lasern können pro Zeiteinheit immer nur kleinere Schichtstärken bearbeitet werden. Sonst entstünde schlicht zu viel Rauch. Ursache: Je mehr Material aufgeschmolzen wird, desto mehr Rauchschwaden entstehen.
Was folgt daraus? Entweder wird nun weniger Nebel erzeugt, indem weniger Material aufgeschmolzen wird – dann reden wir von dünneren Schichten.
Oder aber die Energie pro Laser muss reduziert werden. Warum? Stelle dir diesbezüglich einfach Scheinwerfer im Nebel vor: Selbst bei mehr Licht wird die Sicht nicht besser. Übertragen auf die additive Fertigung heißt das: Wenn die Laser ihr Ziel nicht mehr deutlich anvisieren können, entsteht nur noch Murks. Zwingende Konsequenz: eine reduzierte Laserleistung, um den Rauch zu verringern.
Übersetzt in die Praxis heißt das: Wir verschmelzen in unseren Anlagen mit ziemlich großer Leistung pro Laser Schichten von bis zu 120 µm Stärke. Möglich macht das unsere exzellente Rauchabsaugung. Die Chinesen beschränken sich bei 64 Lasern zwangsläufig auf geringere Schichtstärken von vielleicht 30 µm bis 40 µm, mit kleinerer Leistung pro Laser. Ergebnis: Unser Produktivitätswert – gemessen in cm3/h – ist immer noch deutlich größer als bei den fernöstlichen Wettbewerbern. Tendenz: Faktor zwei!
Und die Stückkosten sind bei den Wettbewerbern nach unserer Bewertung deutlich höher als bei uns. Denn die maßgeblichen Kostentreiber in den Maschinen sind die Strahlquellen und die ihnen zugeordneten Scanner.
Lesetipp: Nikon übernimmt SLM Solutions
Wie wäre es denn, wenn parallel zur Laserleistung der Bauraum vergrößert wird?
Tatsächlich machen die Chinesen genau das! Ihre Plattform bei der 64-Laser-Anlage misst aktuell 2 m x 2 m. Die Maschine ist also prädestiniert für große Bauteile. Aber wer braucht solche Dimensionen? Meine Antwort: Vor allem die Luft- und Raumfahrtindustrie! Sie stellt damit beispielsweise Triebwerkskomponenten her. Meist sind das zirkulare Körper mit geringen Wandstärken, die sich nach oben hin verjüngen. Der Bauraum ist also – pro Schicht – immer nur minimal belegt. Von den vielen Lasern sind im Zeitablauf dann auch immer nur wenige im Einsatz. Das ist in meinen Augen lediglich eine Demonstration des technisch Möglichen. Wirtschaftlich macht es aber keinen Sinn. Außerdem: Über die Probleme, die entstehen, wenn auch nur eine einzige Strahlquelle ausfällt, will ich hier gar nicht im Detail reden. Nur ganz kurz: Dann müssen die Aufgaben von jedem Laser und jedem Scanner neu verteilt werden …
Zurück zum Rauch: Wenn der das Problem ist: Warum wird der nicht einfach weggeblasen, etwa mit einem laminaren Luftstrom?
Eine naheliegende Idee – und so geschieht das auch in unseren Anlagen. Es ist aber sehr schwer, den laminaren Gasstrom über eine längere Strecke über das Baufeld mit dem sorgsam geglätteten Pulverbett aufrechtzuerhalten. Außerdem: Wenn der Rauch – etwa von links nach rechts – abgeführt wird, kreuzt er auf seinem Weg alle nachgelagerten Strahlquellen. Wenn man einfach nur immer mehr Laser zum Einsatz bringt, dann ist das Ergebnis ein Chaos.
Ich hörte unlängst von einer Lösung, an der ihr arbeitet. Jetzt mal Butter bei die Fische: Wie sieht die aus?
2023 haben wir die Technologie der Firma Adira aus Portugal übernommen. Sie funktioniert so: Die Strahlquellen sind in einer Phalanx angeordnet, also in einem einzigen Prozesskopf, in einer Reihe. Dieser Prozesskopf wird mittels eines Portalsystems über den Bauraum geführt. Mit an Bord: Gaszuleitung und die entsprechende Rauchabführung. Beide liegen eng beieinander. Es gibt also keine Probleme mit Luftströmen über große Distanzen.
Lesetipp: Boom beim Bauraum – 3D-Drucker werden immer größer
Das klingt, als wäre das beliebig skalierbar …
Das ist es. Genau deshalb arbeiten wir daran. Dabei werden wir darauf achten, dass im beliebig skalierbaren Bauraum beliebig viele Bauteile angeordnet und die dafür nötigen Laser und Scanner optimal ausgelastet sind. Denn: Das wird die Stückkosten wirklich senken …
Das gesamte Interview hören Sie in Folge 95 des Podcasts „Druckwelle“:
Hier wird Ihnen ein externer Inhalt von Podigee angezeigt.
Mit der Nutzung des Inhalts stimmen Sie der Datenschutzerklärung
von youtube.com zu.
Falls Ihnen der Podcast gefällt: gerne abonnieren!
Das Gleiche gilt für den neuen Newsletter der Druckwelle! Er erscheint alle 14 Tage und ist kostenlos.
Ein Beitrag von: