Automatisierte Qualitätssicherung für Kleinserien
Durch den Vergleich von virtuellen mit realen Fotos lassen sich fatale Montagepannen vermeiden. Beide Bilder vergleicht eine neue Software und schlägt schon bei kleinsten Abweichungen Alarm.
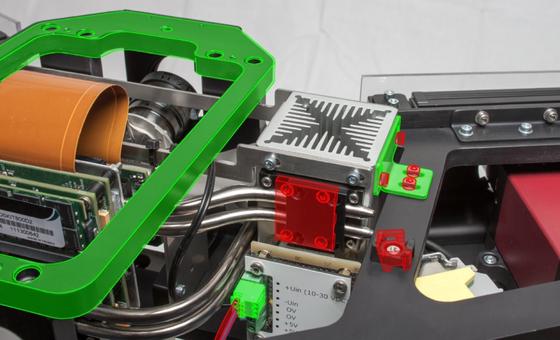
Bei der modellbasierten Montageprüfung werden die digitalen Solldaten montierter Bauteile mit dem realen Ergebnis durch eine Software miteinander verglichen. Fehler werden unmittelbar erkannt.
Foto: Fraunhofer IFF
Magdeburger Forscher fotografieren Dinge, die es gar nicht gibt. Noch nicht jedenfalls. Was sich eher nach einer Varieté-Nummer anhört hat einen sehr ernsthaften Hintergrund. Es ist ein Schritt auf dem Weg zur Null-Fehler-Produktion auch von Kleinserien und Einzelstücken, mehr noch: Die virtuellen Bilder verbessern die Sicherheit von Produkten, Flugzeugen etwa. Das Kunststück ist am Fraunhofer-Institut für Fabrikbetrieb und -automatisierung (IFF) in Magdeburg gelungen.
Automatisierte Qualitätskontrollen bei Massenware ist bereits gang und gäbe. Die Details, auf die es ankommt, werden beim ersten sehr sorgfältig von Fachleuten geprüften Produkt fotografiert. Die gleichen Ausschnitte werden bei den nächsten Produkten, Autos etwa, ebenfalls fotografiert. Beide Bilder vergleicht eine Software. Stimmen sie nicht hundertprozentig überein gibt es Alarm.
Bei Kleinserien wäre das zu teuer. Deshalb gehen die Forscher um Dirk Berndt vom IFF einen anderen Weg. Sie fertigen auf der Basis der Konstruktionsdaten virtuelle Fotos von sicherheitsrelevanten Montagegruppen etwa in Flugzeugen. Das gleiche Detail des realen Produkts fotografiert eine echte Digitalkamera. Wie in der Autoproduktion werden die Bilder von einer Software analysiert und verglichen. Ändert sich etwas bei den Konstruktionsdaten lassen sich die virtuellen Fotos per Mausklick aktualisieren.
Vertauschte Kabel
Vor allem im Flugzeugbau könnte diese Art der Qualitätskontrolle sehr viel Geld sparen und die Sicherheit verbessern. Heute kontrollieren die Monteure selbst, ob sie alles richtig gemacht haben. Besonders wichtige Montagegruppen werden zusätzlich von speziell geschulten Facharbeitern überprüft. Trotzdem sind Fehler nicht ausgeschlossen. So waren in einer Boeing 737, die 1989 kurz nach ihrem Erstflug abstürzte, die Kabel, über die Störungen an den Triebwerken gemeldet werden, vertauscht. Kurz nach dem Start erreichten Temperatur und Drehzahl des linken Motors kritische Werte, so wurde es jedenfalls im Cockpit angezeigt. In Wirklichkeit war es das rechte Triebwerk. Durch die vertauschten Kabel in die Irre geführt, schaltete der Kapitän den intakten Motor ab. Bei der Notlandung starben 44 der 126 Passagiere und Besatzungsmitglieder. Hätte es bereits eine automatisierte Qualitätskontrolle gegeben wäre der fatale Fehler sofort aufgefallen.
Berndt und sein Team stellen die Software, die bei beliebigen Produkten einsetzbar ist, auf der Messe „Control“ vom 14. bis 17. Mai in Stuttgart vor.
Ein Beitrag von: