Continentals konkrete Vision: So sieht die digitale Fabrik von morgen aus
In der Automobilindustrie haben sich die Rahmenbedingungen stark verändert und werden es weiterhin tun. Hersteller müssen sich darauf einstellen. Continental arbeitet derzeit an einer passenden Lösung: einer möglichst digitalen Fabrik, mit der sich Prozesse effizient steuern lassen.
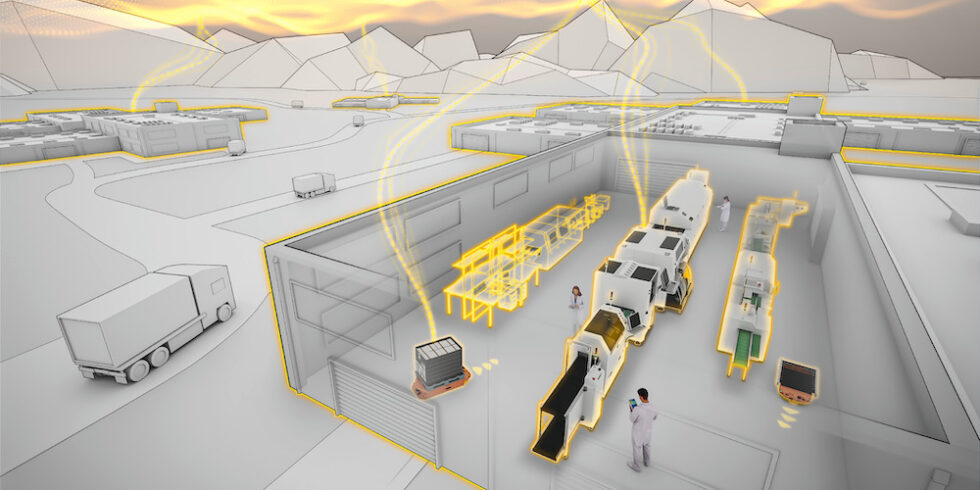
Basis für eine voll vernetzte Fabrik sind Daten. Sie müssen kontinuierlich gesammelt werden.
Foto: Continental
Stellen Sie sich vor, Sie planen Ihre Produktion künftig vor dem Start schon einmal komplett durch, simulieren sie und können so bereits im Vorfeld wichtige Optimierungen vornehmen. Klingt futuristisch, soll aber nach Abschluss des neuesten Projekts von Continental Realität werden. Und zwar wenn möglich, bereits in wenigen Jahren. So zumindest haben es sich die acht Partner in dem Projekt aus Industrie und Forschung vorgestellt. Continental übernimmt in dem Projekt, das den Namen „DIAZI“ trägt, die Leitung. Die Abkürzung steht für „Digitalisierung des Industrialisierungsprozesses in der Automobil- und Zuliefererindustrie“ und wird vom Bundesministerium für Wirtschaft und Klimaschutz gefördert. Innerhalb von drei Jahren haben sich die Projektpartner, darunter acht renommierte IT- und Prozessoptimierungsunternehmen, Universitäten und darauf spezialisierte Start-ups, vorgenommen, Produktionsprozesse möglichst vollständig zu digitalisieren.
Die Potenziale von Digitalisierung und Künstlicher Intelligenz
Die Branche muss sich zunehmend auf neue Rahmenbedingungen einstellen: Kundinnen und Kunden erwarteten schnellere Entwicklungszyklen, Lieferketten werden komplexer, Wünsche und Anforderungen veränderen sich. Um damit künftig noch besser umgehen zu können, müssten Produktionslinien nach Ansicht der Projektpartner digital geplant, simuliert und betrieben werden können. Nur auf diese Art und Weise ließen sich Effizienz, Flexibilität und Wirtschaftlichkeit der Automotive-Werke erheblich verbessern. „Schon heute sind wir führend in der Entwicklung digitaler Komponenten wie intelligenter Display-Lösungen. Jetzt sorgen wir dafür, dass Innovationen dank digitaler Simulationen, künstlicher Intelligenz und Datenmanagement in der Cloud über die gesamte Fertigung hinweg, schneller, effizienter, nachhaltiger und kostengünstiger auf den Markt gebracht werden. Erste Ergebnisse bescheinigen uns, dass wir auf dem richtigen Weg sind. Unsere Vision der ‚digitalen Fabrik‘ nimmt deutlich Gestalt an“, sagt Thomas Ebenhöch, Head of Operations des Geschäftsfelds User Experience (UX) bei Continental Automotive.
Continental setzt auf KI für die digitale Fabrik
Dank des Einsatzes künstlicher Intelligenz sei es künftig möglich, neue Fertigungsanlagen vor dem eigentlichen Produktionsstart virtuell anlaufen zu lassen. Das böte den Vorteil, Fertigungslinien digital vorab zu planen und Abläufe in der Produktion zu simulieren. Auf diese Art und Weise ließe sich ein Produktionsprozess schon vor Beginn optimieren und auch während des Prozesses sei eine kontinuierliche weitere Verbesserung möglich. Darüber hinaus könnten sogar exakte Vorhersagen hinsichtlich der Produktivität getroffen werden und eine detaillierte Analyse der Daten ermögliche es, Ausfallzeiten von Maschinen bereits im Vorfeld zu minimieren. Ziel sei es auch, unterschiedliche Werke eines Unternehmens miteinander zu vernetzen und sogar Fertigungsstandorte von Zuliefererbetrieben einzubinden. Davon versprechen sich die Projektpartner eine schnelle, skalierbare und absolut leistungsstarke Fertigung.
Im Januar 2023 sind die Projektpartner mit ihren Ideen gestartet. Das Bundesministerium erhofft sich von den Ergebnissen, dass diese von Unternehmen in deren Produktionslinien übernommen werden können. Man betrachte das Projekt als „Impulsgeber für volldigitalisierte und KI-gestützte Produktionsprozesse“. Die erste Projektphase liegt bereits hinter dem Projektteam. In dieser ging es darum, innerhalb diverser Digitalisierungsbereiche konkrete Demonstrationsmodelle festzulegen. Darauffolgend sollten die gesamte virtuelle Linienplanung und Inbetriebnahme betrachtet werden, inklusive datenbasierter Prozessoptimierung sowie Transfer in den Anwendungsbetrieb.
Erste Ergebnisse der digitalen Fabrik nutzt Continental bereits selbst
Die erste Aufgabe nannten die Projektpartner „Datenbasierte Prozessoptimierung“. Dabei visualisierten sie den gesamten Datenstrom aus verschiedenen Produktionslinien in einer dafür völlig neu geschaffenen Cloud-Umgebung. Zusätzlich bereiteten sie eine effektive Datenanalyse auf. Auf Basis dessen war es dem Team dann möglich, im Arbeitspaket „Virtuelle Linienplanung und Inbetriebnahme“ Fertigungslinien zu simulieren und außerdem bestehende Abläufe in der Produktion zu optimieren.
Diese ersten Ergebnisse fanden bereits Eingang in die Serienfertigung neuer Display-Lösungen bei Continental. Kundinnen und Kunden konnten also bereits von den ersten Erfolgen des DIAZI-Projektes profitieren. Zu den Projektpartnern gehören Expertinnen und Experten der Hochschule Landshut und der technischen Universität Braunschweig, sowie das Software-Start-up IFOX Systems, das IT-Management-Unternehmen Suse, der Intralogistik-Experte Naise, der Prozess- und Fertigungsbetrieb Dualis und das Unternehmen für Analysesoftware für automatisierte Fertigungsanlagen plus10.
Ein Beitrag von: