Deutsche Batterieproduktion soll internationalen Wettbewerb abhängen
Bei der Beschichtung der Elektroden von Lithium-Ionen-Batterien haben Karlsruher Wissenschaftler einen neuen Rekord aufgestellt: Eine Versuchsanlage schafft 100 Meter pro Minute und ist damit doppelt so schnell wie der Standard in der Industrie. Deutsche Hersteller sollen mit der Technologie im internationalen Wettbewerb aufholen.
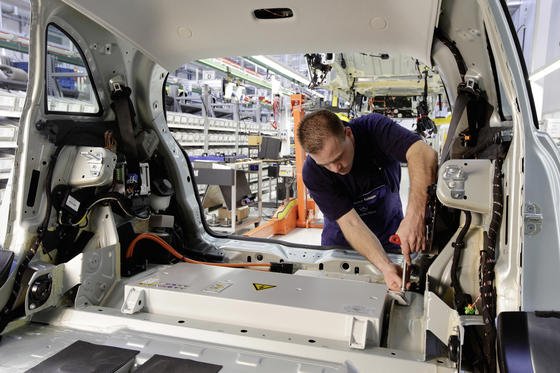
Montage eines Lithium-Ionen-Akkus. Mit neuer Technologie der Fraunhofer-Forscher soll deutschen Herstellern ein Sprung im internationalen Wettbewerb gelingen. An der Forschung beteiligt ist auch der Beschichtungsspezialist Kroenert.
Foto: Daimler
Lithium-Ionen-Batterien kommen nicht nur in Kleingeräten wie Smartphones und Tablet-PCs zum Einsatz, sondern auch in Elektroautos. Die Produktion dominieren derzeit Japan, Südkorea und China. Damit deutsche Hersteller aufschließen können, haben sich Wissenschaftler des Karlsruher Instituts für Technologie (KIT) mit dem Hamburger Unternehmen Kroenert zusammengetan, einem Spezialisten für Beschichtungsanlagen.
Versuchsanlage beschichtet mit 100 Metern pro Minute
Die Experten haben es geschafft, die Geschwindigkeit, mit der Elektroden beschichtet werden, in einer Versuchsanlage auf 100 Meter pro Minute zu verdoppeln. Üblich sind in der Industrie derzeit etwa 50 Meter pro Minute. Mit dem neuen Tempo ließen sich in der Praxis Herstellungskosten für Lithium-Ionen-Batterien deutlich senken.
„Die Asiaten haben einen deutlichen Vorsprung wegen ihrer großen Erfahrung“, sagt Philip Scharfer, einer der beteiligten Wissenschaftler am KIT. Aber: „Sie kochen auch nur mit Wasser“, so Scharfer.
Beschichtungsfolien sind nur wenige Mikrometer dick
Man müsse „deutlich an der Produktionstechnik arbeiten“, sagt Scharfer. Denn die Herausforderung ist groß. Die Folien aus Kupfer, die für die Anode verwendet werden, sind gerade mal acht bis zehn Mikrometer dick – ein Mikrometer ist ein Tausendstel Millimeter. Die Basis der Kathode besteht aus Aluminium und ist mit 20 Mikrometern ebenfalls hauchdünn.
Aus einem pulvrigen Gemisch aus Nickel, Mangan, Kobalt, Ruß und Lithium wird eine Paste hergestellt, die sogenannte Schlitzdüsen absolut gleichmäßig auf die vorbeiflitzende Aluminiumfolie auftragen. In einem langgestreckten, erdgasbeheizten Ofen trocknet die Paste, fertig ist die Kathode. Die Anode wird genauso hergestellt, allerdings aus einer Paste, die vor allem Graphit enthält. 20 bis 50 Meter lang ist eine solche Beschichtungsstraße. Die Folien haben üblicherweise eine Breite von 50 bis 80 Zentimeter. Nahziel sind 130 Zentimeter.
KIT und Kroenert haben strategische Allianz vereinbart
„Für uns eröffnet die Zusammenarbeit mit einem führenden Unternehmen der Beschichtungstechnologie die Möglichkeit, unsere Entwicklungsergebnisse unmittelbar in innovative Maschinen und Anlagen für die Elektrodenproduktion einfließen zu lassen und damit weltweit zu vermarkten“, so Wilhelm Schabel, Professor am Institut für Thermische Verfahrenstechnik des KIT, der das Forschungsteam leitet. „Wir wollen industrielle Prozesse weiterentwickeln mit Blick auf die Kosten.“ Das KIT und Kroenert haben dazu vertraglich eine strategische Allianz vereinbart.
Ein Beitrag von: