Geschnitten, nicht gedrückt
Strecken im Bergbau werden wie Tunnel in Abhängigkeit von Gesteinseigenschaften mit Bohr- und Sprengtechnik oder maschinell aufgefahren. Bei Letzterem konkurrieren Voll- mit Teilschnittmaschinen. Diese Konkurrenz hebt der „Mobile Tunnel Miner“ (MTM) der Aker Wirth GmbH, Erkelenz, auf, indem er die Flexibilität einer Teilschnittmaschine mit der Robustheit einer Tunnelbohrmaschine kombiniert.
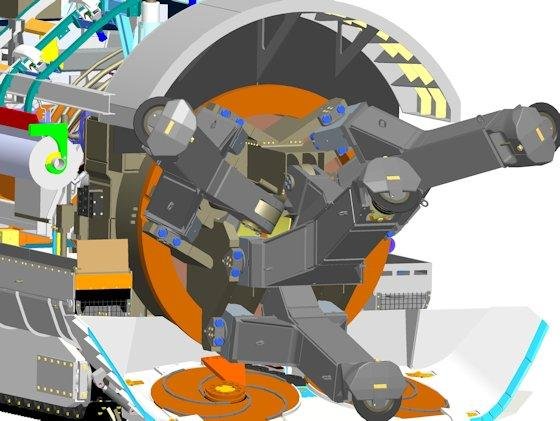
Mehrere hydraulisch frei bewegliche Arme tragen die Schneidrollen, die es erlauben, nahezu beliebige Querschnitte im Berg aufzufahren.
Foto: AW
Der Mobile Tunnel Miner kann im Hartgestein Röhren bis 6 m Durchmesser in nahezu beliebigen Querschnitten auffahren. Dies wird möglich durch hydraulisch bewegte Arme, an denen Rollenmeißel befestigt sind. Sie hinterschneiden das Gebirge, das dadurch auf Zug beansprucht wird und grobstückig abbricht.
Zur letzten Bauma, der internationalen Fachmesse für Bau-, Baustoff- und Bergbaumaschinen sowie Baufahrzeuge und -geräte, stellte Aker Wirth den Mobile Tunnel Miner in zwei Versionen vor, als MTM 4 und MTM 6 – und erhielt einen Innovationspreis für die Entwicklung. Beide Maschinen sollen in Kürze ihre Arbeit in Kupferbergwerken in Chile und Australien aufnehmen.
Der Maschinenbauer unterzeichnete mit dem weltweit größten Kupferproduzenten Codelco einen Vertrag über Lieferung und Erprobung eines MTM 4 im Bergwerk Chuquicamata in Chile. Hier soll die Vortriebsmaschine das untertägige Streckennetz auffahren.
Gemeinschaftsprojekt mit Rio Tinto
Gemeinsam mit Rio Tinto, einem der weltweit größten Bergbauunternehmen, wurde der MTM 6 entwickelt. Er ist Teil von Rio Tintos „Mine of the Future“-Programm und wird im Kupferbergwerk Northpark in Australien getestet.
„Bisher wurden Strecken in Kupferminen ins Gestein gesprengt“, erläutert Ulrich Frenzle, Vice President Mining & Construction bei Aker Wirth. „Mit dem MTM 4 werden sie erstmals maschinell angelegt, wodurch die Effizienz des Vortriebs und die Sicherheit in der Mine massiv verbessert werden.“
Der MTM 4 verfügt über vier, der MTM 6 über sechs hydraulisch bewegte Arme. Diese sind mit Rollenmeißeln ausgestattet, die schräg auf den Bohrarmen stehen, sodass sie die Ortsbrust hinterschneiden. Der Meißel muss dabei nur während des „Anschnäbelns“ die Druckfestigkeit des Gebirges überwinden.
Danach arbeitet er wie ein Stemmeisen, das schräg eingetrieben wird, wobei er nur noch die deutlich geringere Gesteins-Zugfestigkeit zu „stemmen“ braucht. Entsprechend kleiner sind die benötigten Kräfte: Der Energieaufwand für das Aufbrechen des Gesteins ist beim Hinterschneiden nur etwa halb so groß wie beim konventionellen Aufweiten, bei dem die Ortsbrust ausschließlich auf Druck beansprucht wird.
Weniger Werkzeugkosten
Dadurch, dass viel weniger Schneidrollen im Einsatz sind, ist der spezifische Energiebedarf für die Gesteinszerstörung kleiner, es entstehen weniger Werkzeugkosten und eine geringere Maschinenleistung ist nötig. Die Stückigkeit des gelösten Guts kann beeinflusst werden. Schonender Ausbruch und Wiederverwendung des Ausbruchmaterials sind möglich. Die Aufweitung des Uetlibergtunnels in der Schweiz hat die Funktionalität und Vorteile der Hinterschneidtechnik bewiesen.
Der Mobile Tunnel Miner kann in einem einzigen Arbeitsgang die gewünschte Querschnittsform auffahren, auch rechteckige und hufeisenförmige Querschnitte mit bis zu 6 m Bohrdurchmesser, wohingegen beim Einsatz einer konventionellen Tunnelbohrmaschine häufig der untere Teil des Kreisquerschnitts wieder verfüllt werden muss.
Der MTM ist äußerst mobil: Mit seinem Schreitwerk kann er sich flexibel vorwärts und mit einem Raupenfahrwerk auch rückwärts bewegen. Durch mehrere Drehgelenke in der Maschine beträgt der Kurvenradius des MTM 4 nur 24 m, derjenige des MTM 6 gerade einmal 30 m. Eine Tunnelbohrmaschine im vergleichbaren Einsatz benötigt circa 500 m Kurvenradius,
Aker Wirth erwartet, mit dem MTM neue Maßstäbe beim Aufschluss von Bergwerken zu setzen. „Die Entwicklung stand ganz im Zeichen des quantifizierbaren Kundennutzens und der Sicherheit“, erläutert Frenzle. „Im Vergleich zum Sprengvortrieb, der in diesen Gesteinshärten bisher üblich war, sollen mit dem MTM 4 bis zu 12 m Streckenvortrieb pro Tag erreicht und damit die heutigen Leistungen mehr als verdoppelt werden.“
Steuerkabine auf der Maschine
Gegenüber dem Vortrieb mit Bohr- und Sprengarbeit müssen sich bei der maschinellen MTM-Auffahrung deutlich weniger Personen an der Ortsbrust aufhalten. Der MTM wird von einer zentralen Steuerkabine aus bedient, die sich auf der Maschine befindet. Ein hoher Automatisierungsgrad minimiert den Kontakt von Personen mit beweglichen Teilen und Gestein. Zudem kann der MTM aufgrund seiner Flexibilität zur Wartung einfach von der Ortsbrust weggefahren werden, was ebenfalls die Sicherheit des Bedienpersonals erhöht.
„Mit dem Tunnel Miner werden wir die Sicherheit und Effizienz im Untertagebau nachhaltig revolutionieren“, ist Einar Brønlund, CEO bei Aker Wirth, überzeugt. „Mit dieser innovativen Technologie werden die Gesundheits-, Sicherheits- und Umweltschutzleistungen deutlich verbessert.“
Ein Beitrag von: