Gut für Brennstoffzellen: Neue Technik halbiert Kosten für Bipolarplatten
Bipolarplatten sind eine wichtige Komponente von Brennstoffzellen und Elektrolyseuren. Forschende des Fraunhofer IWU haben nun eine Möglichkeit gefunden, die Kosten für die Herstellung von Bipolarplatten zu halbieren.
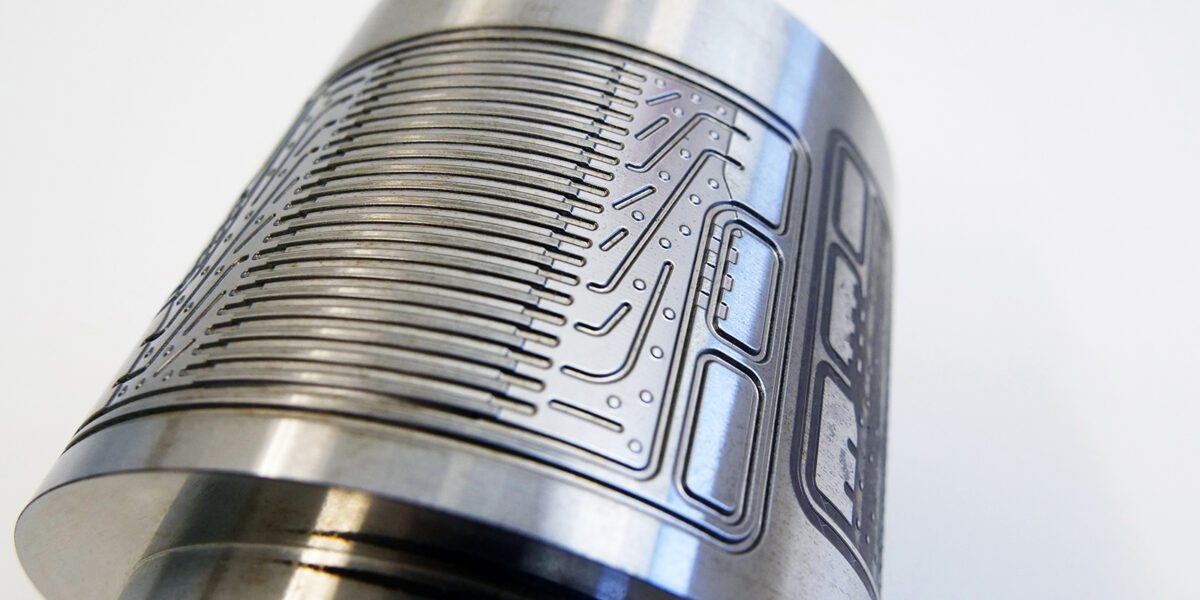
Dank hoher Prozessgeschwindigkeit lassen sich Bipolarplatten mit Hilfe von Hohlprägewalzen sehr viel günstiger herstellen.
Foto: Fraunhofer IWU
Umweltfreundliche Brennstoffzellensysteme, die zum Beispiel Autos antreiben könnten, sind bisher selten und teuer. Ein Grund dafür ist die teure Herstellung der Bipolarplatten. Diese wichtige Komponente wird sowohl in Elektrolyseuren als auch in Brennstoffzellen eingesetzt und spielt eine zentrale Rolle in vielen Wasserstofftechnologien.
Das Fraunhofer-Institut für Werkzeugmaschinen und Umformtechnik IWU hat nun mit der Entwicklung der BPPflexRoll, einer speziellen Hohlprägewalzanlage, einen wichtigen Schritt getan, um die Herstellungskosten zu senken und die Massenproduktion von Bipolarplatten zu ermöglichen. Auf Hannover Messe 2024 vom 22. bis 26 April stellt das Forschungsteam eine Komponente dieser Anlage vor.
Die Ausgangssituation
Wasserstoff-Brennstoffzellen zeichnen sich durch einen hohen Wirkungsgrad aus. Sie erzeugen elektrischen Strom aus Wasserstoff und Sauerstoff. Das macht sie ideal für umweltfreundliche Fahrzeuge. Elektrolyseure kehren diesen Prozess um. Sie spalten Wasser mit Hilfe von elektrischer Energie in Wasserstoff und Sauerstoff. Zentral für beide Systeme sind Bipolarplatten.
Bipolarplatten umschließen wichtige Teile wie die Membran-Elektroden-Einheit (MEA) und die katalytisch beschichtete Membran (CCM). In Brennstoffzellen ermöglichen sie den Transport von Sauerstoff und Wasserstoff sowie die Kühlung. Ein großes Hindernis ist die teure Herstellung der Bipolarplatten. Dies schränkt den breiten Einsatz von Wasserstofftechnologien ein, wie z.B. Brennstoffzellenautos.
Die Lösung: BPPflexRoll
Das Fraunhofer IWU in Chemnitz hat gemeinsam mit der Profiroll Technologies GmbH eine Lösung entwickelt: die BPPflexRoll. Diese Anlage zum Hohlprägewalzen verspricht eine kostengünstigere Produktion von Bipolarplatten. Die Anlage ermöglicht einen kontinuierlichen Fertigungsprozess. Sie ist schneller und kostengünstiger als bisherige Verfahren. Pro Minute können bis zu 120 Halbplatten hergestellt werden. Dazu sollen sich die Kosten für die Bipolarplatten durch die neue Technik halbieren.
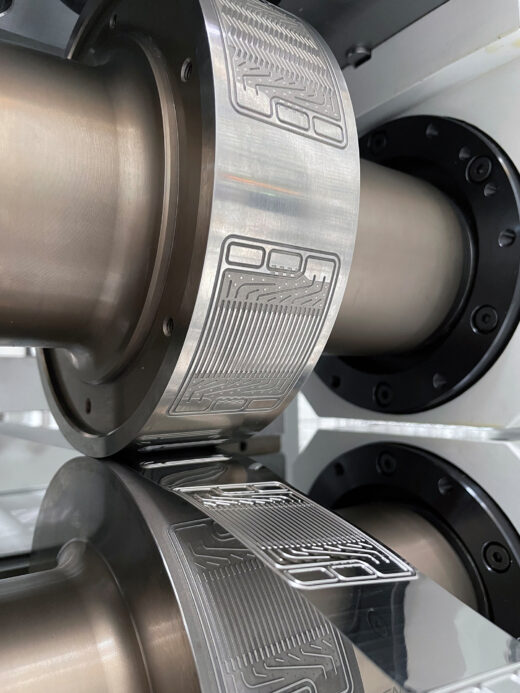
Hohlprägewalzen von Bipolarplatten mit der BPPflexRoll. In der neu entwickelten Technologie wird die Struktur der Bipolarplatte durch ein Walzenpaar geprägt.
Foto: Fraunhofer IWU
Und so funktioniert BPPflexRoll: Ein Walzenpaar prägt die Metallbänder. Dazwischen ist ein hauchdünnes Metallband eingespannt, das kontinuierlich läuft. Ein der Umformwalzen ist als Stempel, die andere als Matrize definiert. Laut Forschungsteam haben die Walzen zum Ausformen der Strömungskanäle mit dem Werkstück lediglich einen Linienkontakt. Dadurch lassen sich die Prozesskräfte erheblich reduzieren.
Darüber hinaus ist die Anlage flexibel und kann an unterschiedliche Bipolarplattengeometrien angepasst werden. Dadurch wird die Produktion effizienter und kostengünstiger. Die Anlage besteht aus drei Walzgerüsten und benötigt eine Aufstellfläche von 4500 mm x 3300 mm. Sie verfügt bereits über eine Steuerungstechnik und ein Bedienkonzept, die in wesentlichen Punkten einer industriellen Anlage entsprechen.
Überwachung in Echtzeit
Die Versuchsanlage ist ein Schritt hin zu intelligenteren Umformmaschinen. Sie überwacht den Produktionsprozess in Echtzeit und garantiert so eine hohe Qualität der Bipolarplatten. Erste mit dieser Technologie produzierte Bipolarplatten werden bereits getestet. Dies könnte die Nutzung von Wasserstofftechnologien in Zukunft erheblich verbreiten und vereinfachen.
„Anders als bei bisherigen Anlagen überprüfen wir künftig die Qualität der BPP im laufenden Prozess, indem wir die Prozessparameter mit Sensoren erfassen, zusammenführen und korreliert analysieren können“, erklärt Robin Kurth, Gruppenleiter für Umformmaschinen am Fraunhofer IWU.
Auf der Hannover Messe präsentieren sie vom 22. bis 26. April auf dem Fraunhofer-Gemeinschaftsstand in Halle 2, Stand B24 eine Anlagenkomponente mit einer Rolle sowie damit hergestellte Bipolarplatten.
Ein Beitrag von: