Lichtbogenverfahren erlaubt Auftragschweißen im Turbogang
Auftragschweißen soll zukünftig viel schneller gehen: Deutsche Forscher tüfteln an einem laserunterstützen Lichtbogenverfahren. Erste Testanlagen stehen in Lübeck und Hannover.
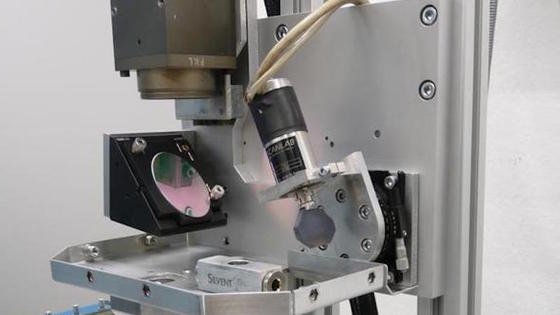
Das laserunterstützte Lichtbogenverfahren erreicht eine Auftragrate von 7,5 Kilogramm pro Stunde. Konventionelle Verfahren erreichen rund fünf Kilogramm. Für das Verfahren reicht ein preiswerter Diodenlaser.
Foto: LZH
Die Schaufeln der Turbinen von Flugzeugtriebwerken und Gasturbinen fransen mit der Zeit wegen der hohen Belastung aus. Auch die besonders gehärteten Schneidkanten von Pflugscharen verschleißen, vor allem bei Bearbeiten von steinigen Äckern. Die teuren Bauteile dann einfach einzuschmelzen, wäre eine gigantische Geldvergeudung. Deshalb werden sie repariert. Das gelingt mit Auftragschweißverfahren. Abgetragenes Material wird ersetzt.
Heute genutzte Verfahren sind zeitraubend
Beim konventionellen Verfahren des Auftragschweißens brennt ein Lichtbogen zwischen der Drahtelektrode und dem Werkstück und schmilzt beide auf. Da der Aufmischgrad bei etwa 30 Prozent liegt, müssen mehrere Schichten aufgebracht werden, bis die Schutzschicht ausreichend rein ist. Bisher erreichen konventionelle Verfahren beim Auftragschweißen eine durchschnittliche Auftragrate von fünf Kilogramm pro Stunde. Im Fall von großflächigen und mehrlagigen Schutzschichten kann der Vorgang über 24 Stunden pro Quadratmeter dauern.
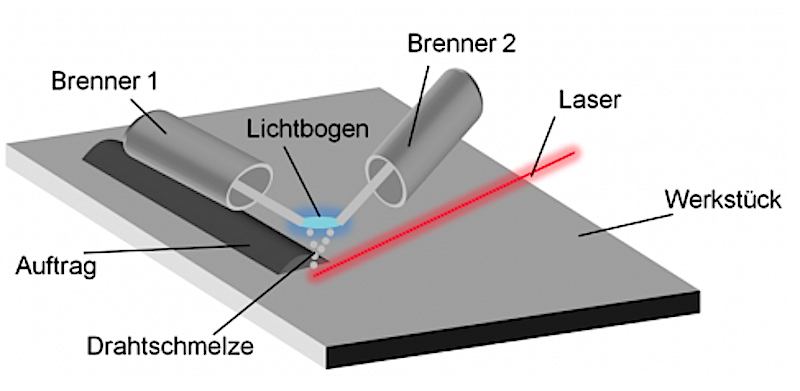
Aufbau des lasergestützten Auftragschweißverfahrens: Der Lichtbogen entsteht zwischen zwei Drähten und schmilzt diese auf. Dann werden sie über die zu reparierende Fläche geführt.
Quelle: LZH
Wissenschaftler des Laser Zentrums Hannover (LZH) haben nun im Rahmen des Projekts HoDopp ein laserunterstütztes Lichtbogenverfahren entwickelt, bei dem dies bereits mit einer Schicht in einem Arbeitsgang erreicht werden kann. Der Lichtbogen brennt zwischen zwei Drähten und schmilzt diese gleichzeitig auf. Die Drähte werden dann über die zu reparierende Fläche geführt. Das erhöht die Auftragrate auf 7,5 Kilogramm pro Stunde. Der zusätzlich eingesetzte Laserstrahl sorgt zudem für eine sichere Anbindung der Schicht und verbessert die Nahtform. Zudem wird die Schicht mit geringem Einbrand aufgebracht.
LZF-Forscher bauen zwei Versuchsanlagen auf
Für das Verfahren reicht ein preiswerter Diodenlaser, der ins Budget der meisten kleinen und mittleren Unternehmen passen dürfte. Die LZH-Wissenschaftler bauten die erste Versuchsanlage bei der Druckguss Service Deutschland GmbH in Lübeck auf. Die Zweite errichteten sie bei der der G+F Strate GmbH in Hannover, einem Spezialisten für die Reparatur von Metallteilen.
Ein Beitrag von: