Neues Labor testet Ermüdung von Proben im Zeitraffer
In einem neuen Labor in Dresden wird die Lebensdauer von Bauteilen ermittelt, die wechselnden Belastungen ausgesetzt sind. Die Industrie nutzt die Ergebnisse, um ihre Produktionstechnik zu verbessern.
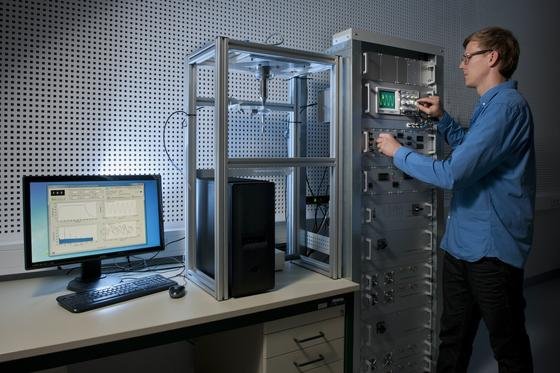
Einrichtung des Hochfrequenz-Ermüdungsprüfstandes.
Foto: Fraunhofer IWS Dresden/Frank Höhler
Der Drucker schweigt. Ganz plötzlich. Nichts bewegt ihn wieder zum Leben. Irgendein Bauteil in seinem Inneren ist wohl zerbrochen. Eine Reparatur lohnt sich nur bei teuren Profi-Geräten. Es schneit. Mehr als üblich. Überall türmt sich der Schnee. Plötzlich stürzt das Flachdach einer Sporthalle ein. Mindestens einer der vielen Tragbalken hat dem Druck nicht standgehalten. Im Drucker fand ein Ermüdungsbruch statt, im Balken ein Gewaltbruch. So charakterisieren Fachleute die ärgerlichen Ereignisse.
Forscher des Fraunhofer-Instituts für Werkstoff- und Strahltechnik (IWS) in Dresden wollen jetzt herausfinden, was man tun muss, um zumindest den Ermüdungsbruch in den Griff zu bekommen. Der ereignet sich nach unzähligen, manchmal auch nach überschaubar wenigen Belastungswechseln. Das simulieren die Wissenschaftler in Dresden jetzt in einem neu eingerichteten Hochfrequenz-Ermüdungslabor. Bauteile zerbrechen oft erst nach mehreren Jahren, zu lange, um die Ursachen in klassischen Versuchen herauszufinden. Die Dresdener machen das gewissermaßen im Zeitraffer. Bis zu 20.000 Verformungen pro Sekunde sind in dem Prüfstand nötig. In einem Ultraschallabor finden ergänzende Untersuchungen statt. Dabei werden die Bauteile heiß, weil die Moleküle gewissermaßen aneinander reiben. Das könnte die Aussagekraft der Versuche gefährden. Deshalb werden die Proben gekühlt. Damit sind Wärmeeinflüsse ausgeschaltet.
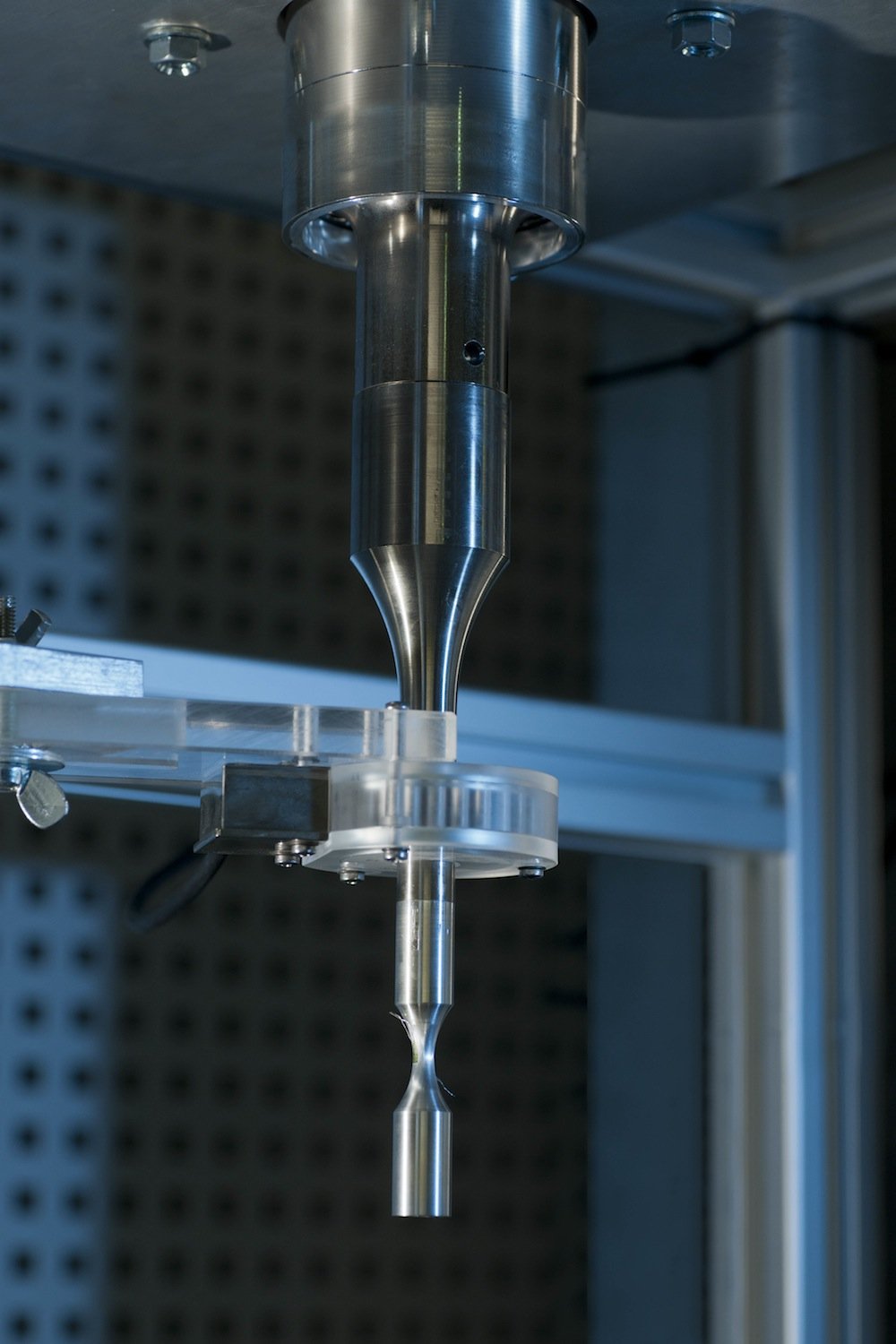
Einseitige Einspannung einer Ultraschall-Ermüdungsprobe.
Quelle: Fraunhofer IWS Dresden/Frank Höhler
„Bereits geringste Veränderungen in der Materialzusammensetzung und im Fertigungsablauf haben einen immensen Einfluss auf die Schwingfestigkeit eines sicherheitsrelevanten Bauteils“, sagt Professor Martina Zimmermann, auf deren Anregung hin der Prüfstand aufgebaut wurde. Je schneller die richtigen Werkstoffe und Herstellungsverfahren gefunden sind, desto preiswerter ist es, langlebige Güter zu produzieren.
Werkstoff, Fertigung und Konstruktion bilden eine Einheit
Proben, die im Versuch mindestens zehn Millionen Lastwechsel ohne Bruch oder Anriss ertragen, gelten als dauerfest. Mindestens zehn, manchmal auch 50 Proben müssen getestet werden, um die Dauerfestigkeit eines realen Bauteils mit ausreichender Sicherheit vorhersagen zu können. Statistisch abgesicherte Werkstoffkenndaten ließen sich bisher praktisch nicht ermitteln.
Bei der Hochfrequenzbelastung, die die Versuchsdauer um das Tausendfache verkürzt, werden die Schäden charakterisiert, indem Werkstoff, Fertigung und Konstruktion als Einheit betrachtet werden. Eine enge Verzahnung von mechanischer Prüfung, einer Schadensbeurteilung vor Ort und einem Labor, in dem die Werkstoffzusammensetzung akribisch ermittelt wird, sind feste Bestandteile der Erforschung der Werkstoffermüdung. Die meisten Versuche finden gemeinsam mit Industrieunternehmen statt, sodass Ergebnisse direkt in die Fertigung einfließen.
Ein Beitrag von: