Sensoren finden winzige Risse im Stahl
Berliner Wissenschaftler haben ein System zur automatisierten Endkontrolle von großen Bauteilen aus Stahl entwickelt. Damit können selbst kleinste Risse entdeckt werden. Bisher geschieht die Materialprüfung in Handarbeit.
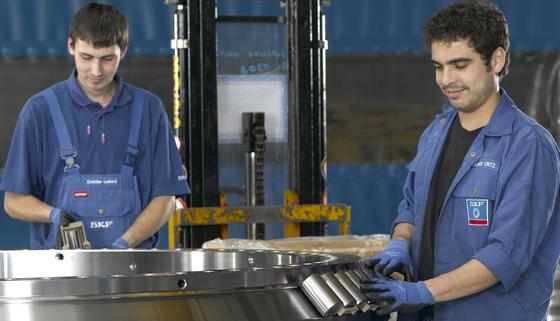
Eine stählerne Angelegenheit: die Herstellung eines Kugellagers für einen Windgenerator.
Foto: SKF
Wenn ein Bauteil fertig ist, etwa der Außenring eines gewaltigen Kugel- oder Wälzlagers, wie es in Windkraftanlagen, großen Maschinen und Lokomotiven eingesetzt wird, stellt sich die Frage, ob es sich auch in einwandfreiem Zustand befindet. Oder gibt es irgendwo tief im Inneren Risse, die die Lebensdauer drastisch reduzieren? Die müssen gefunden werden, und das dauert. Der fertige Ring, der einen Durchmesser von bis zu 3,5 Meter haben kann, wird in Handarbeit mit magnetischem Pulver bestäubt. Dort, wo sich tief im Inneren ein Riss befindet, sammeln sich besonders viele Teilchen, was unter ultraviolettem Licht besonders gut ins Auge fällt.
An einem Riss verändert sich das Magnetfeld
Ingenieure der Bundesanstalt für Materialforschung und -prüfung (BAM) in Berlin haben jetzt ein Prüfverfahren entwickelt, das erheblich schneller zum Ziel führt und weitaus präziser ist als das bisher gebräuchliche. Die neue BAM-Technik basiert auf dem Phänomen, dass sich an einem Riss ein Magnetfeld verändert. Sie nutzt Sensoren, die ihren elektrischen Widerstand ändern, wenn sie in ein Magnetfeld geraten. Das nennt man Magnetoresistenz. Die Berliner setzen besonders empfindliche Sensoren ein, die auf dem Prinzip der „Giant Magnetoresistance“ (GMR) beruht, ein Begriff, der mit Riesenmagnetowiderstand übersetzt wird. Diesen Effekt entdeckten 1988 Peter Grünberg vom Forschungszentrum Jülich und Albert Fert von der Universität Paris-Sud unabhängig voneinander. Dafür erhielten sie 2007 den Physiknobelpreis.
Materialfehler werden markiert
Der GMR-Effekt entsteht, wenn zwei Schichten aus ferromagnetischem Material durch eine nicht magnetische Schicht voneinander getrennt werden. Diese Schichten sind nur Millionstel Millimeter dick. Das Feld der beiden Magnetfolien ist unterschiedlich ausgerichtet. Schon das kleinste Magnetfeld, in das der GMR-Sensor gerät, wirbelt das System durcheinander, sodass sich sein Widerstand deutlich verändert. Bisher werden solche Sensoren in Leseköpfen von Festplatten und in Autos eingesetzt. Hier informieren sie das Antiblockiersystem über die Drehzahl der Räder.
Der BAM-Prüfkopf, der das fertige Bauteil abscannt, enthält außer 48 GMR-Sensoren eine stromdurchflossene Spule, die für eine lokale Magnetisierung sorgt. Beim Passieren eines Risses verändert sich das induzierte Magnetfeld. Das registrieren die Sensoren auf tausendstel Millimeter genau. Die Widerstandsänderungen der Sensoren werden mit Hilfe eines Computerprogramms zu einem Bild zusammengesetzt, auf dem die Fehler markiert sind. „Wir können sogar sagen, in welcher Tiefe sich ein Riss befindet“, sagt Projektleiter Marc Kreutzbruck. Ihren Prototyp stellt die BAM auf der Hannover Messe vor.
Ein Beitrag von: