Simulation ermöglicht präzisere Herstellung von Keramikfolien
Keramikfolien präziser und kostengünstiger herstellen: Das ist das Ziel eines neuen Simulationsverfahrens des Fraunhofer-Instituts für Werkstoffmechanik. Es soll komplexe Prozesse während des Gießens der Folien vorhersagbar machen.
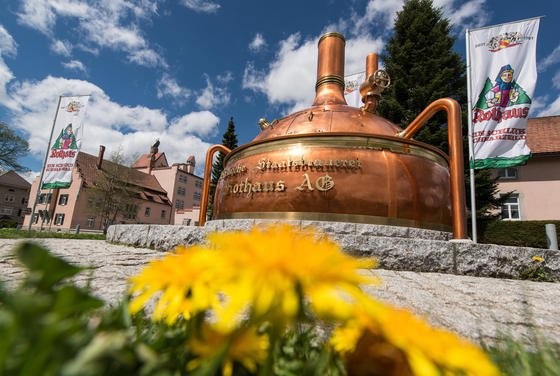
Baden-württembergische Staatsbrauerei Rothaus: In vielen Brauereien kommen Keramikfolien als Wasserfilter zum Einsatz.
Foto: Patrick Seeger/dpa
Autos, Flugzeuge, Druckmaschinen, Biogas- und Kläranlagen, Wasserfilter in Brauereien – die Liste der Einsatzgebiete von Keramikfolien ließe sich noch weit verlängern. Weil Keramik bekanntermaßen hohe Temperaturen aushält, beliebig formbar ist und als poröses Material auch unerwünschte Bestandteile lösen kann, sind der Anwendung kaum Grenzen gesetzt.
Die Eigenschaften der Keramikfolien ergeben sich während des Gießens – ein Spiel mit vielen Unbekannten, das sich bislang nicht exakt steuern lässt. Um grobe Erfahrungswerte durch präzise Erkenntnisse zu ersetzen, haben Forscher am Fraunhofer-Institut für Werkstoffmechanik (IWM) in Freiburg deshalb ein Simulationsverfahren entwickelt.
Am Computer imitieren die Wissenschaftler den Gießprozess der Folien. „Mit unserer Software können wir den Foliengießprozess auf verschiedenen Größenskalen betrachten und genau untersuchen, wie sich die einzelnen Parameter auf die Eigenschaften der Folie auswirken“, erklärt Pit Polfer, Wissenschaftler am IWM.
Schlicker kann im toten Winkel des Gießkastens hängenbleiben
Die Folien werden aus einem Keramikpulver hergestellt, das mit Lösungsmitteln und Zusatzstoffen vermischt wird. Daraus entsteht ein fließfähiger Schlicker, der in Gießkästen gefüllt wird. Daraus fließt das Material durch einen Spalt, dessen Größe die Dicke der Folien bestimmt, auf ein Förderband. Anschließend wird die Folie getrocknet. Ein im Prinzip einfaches Verfahren, bei dem sich die Hersteller bislang aber nur an die gewünschten Eigenschaften der Folien herantasten können, sagen die IWM-Forscher.
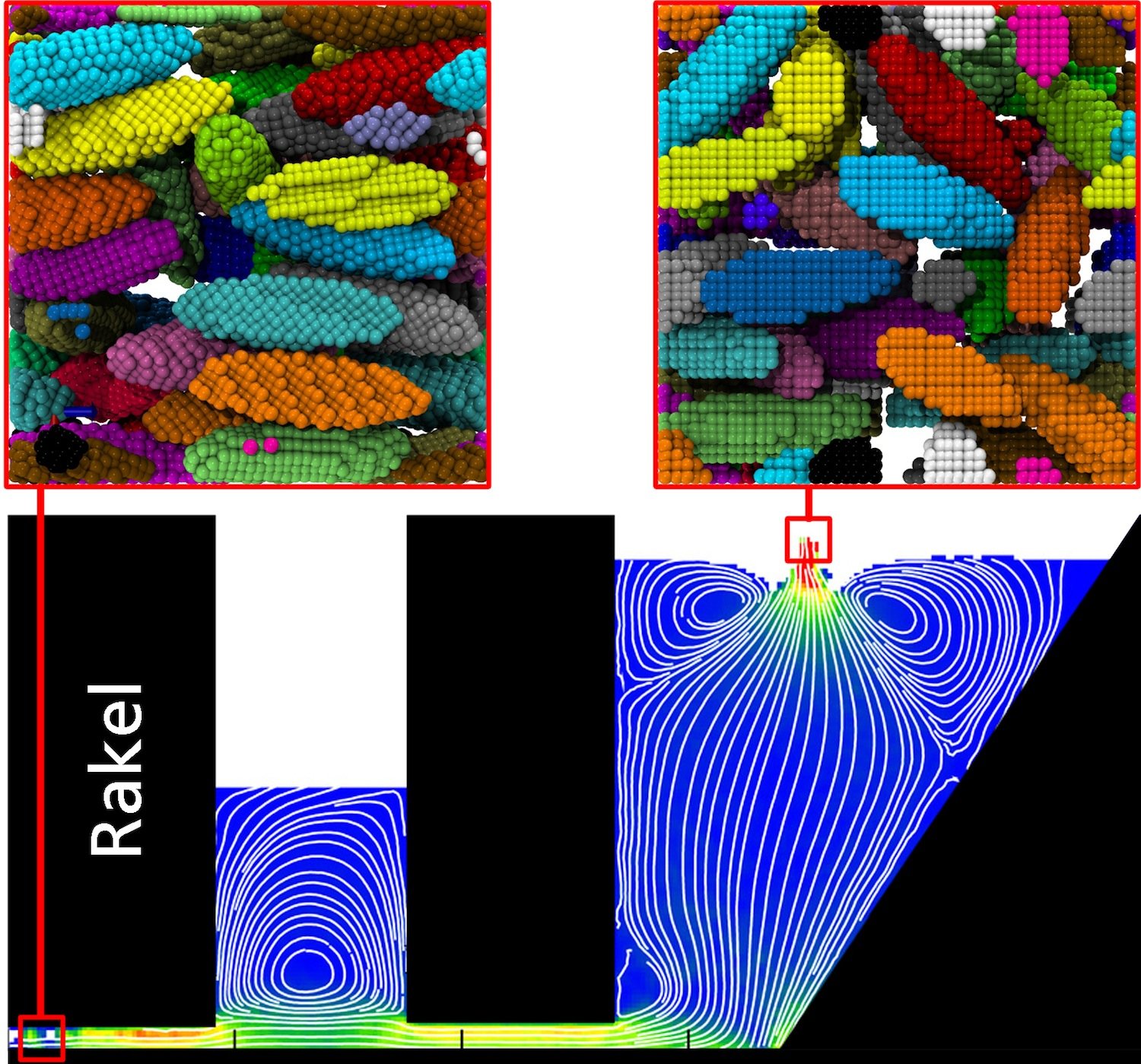
Makroskopische Simulation (unten): Stromlinien während des Gießprozesses, bei dem der Keramikschlicker rechts eingefüllt wird und links unten als Folie den Gießkasten verlässt. Mikroskopische Simulation (oben): Ausrichtung der Keramikpartikel an zwei Stellen im Prozess.
Quelle: Fraunhofer IWM
Ihre Simulation, die präzise Einstellungen der Maschinen ermöglichen soll, funktioniert in zwei Schritten: Zunächst berechnet sie, wie sich der Schlicker makroskopisch im Gießkasten verhält. Bleibt er irgendwo in toten Winkeln hängen, wo das Material altert und die Qualität des Produktes mindert, wenn es dann doch in die Folie gerät? Die Produzenten sollen dank der Analyse die optimale Geometrie für ihre Gießkästen entwickeln können.
Mikroskopische Analyse der Keramikteilchen
Zweiter Schritt ist die mikroskopische Analyse. Wie sind die einzelnen, unterschiedlich großen und unterschiedlich geformten Keramikteilchen angeordnet? Wie beeinflussen sie sich gegenseitig? Um den Aufwand für diese Untersuchung zu begrenzen, werden nur einzelne Flüssigkeitstropfen auf diese Weise analysiert. „Aus diesen Berechnungen können wir dann auf das Verhalten des gesamten Keramikschlickers rückschließen“, sagt Polfer. So sei es möglich, die Ausrichtung der Partikel oder Größengradienten in der Folie einzustellen, um etwa Spezialanwendungen gezielter herstellen zu können.
Für die Hersteller soll das Verfahren einen deutlichen Gewinn bringen. Sie könnten die Prozessführung optimieren, den nicht verwertbaren Ausschuss verringern und die Qualität des Produkts verbessern – letztlich also auch massiv Kosten sparen.
Ein Beitrag von: