So lässt sich Korrosion mit Smart Pigments stoppen
Korrosion verursacht gigantische Kosten. Nach Schätzungen sind es weltweit knapp 2,7 Billionen Euro Korrosionskosten im Jahr. Konventionelle Beschichtungen enthalten jedoch oft giftige Schwermetalle. Potsdamer Forscher haben jetzt eine Technologie entwickelt, die nachhaltiger ist und viel länger schützt. Vorbild ist die menschliche Haut mit ihren Selbstheilungskräften.
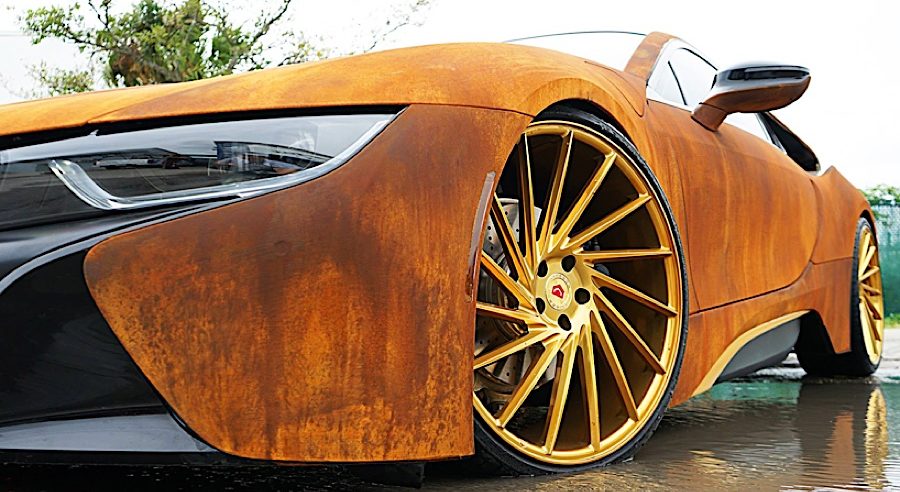
Der Rost auf diesem BMW i8 ist nicht echt, sondern hat das US-Unternehmen MetroWrapz nur durch Folie imitiert. Doch Rost ist für Milliardenschäden verantwortlich. Jetzt haben Max-Planck-Forscher einen Schutzmechanismus entwickelt, der Korrosion im Ansatz stoppen soll.
Foto: MetroWrapz
Korrosion ist extrem teuer: Korrosion soll für Schäden in Höhe von vier Prozent des Bruttoinlandsprodukt verantwortlich sein. In Deutschland wären das im vergangenen Jahr rund 130 Milliarden Euro gewesen. Und das sind nur die direkten Kosten. Hinzu kommen indirekte Kosten durch Personenschäden, Produktionsausfälle und Schäden durch das Auslaufen umweltschädlicher Flüssigkeiten.
Um Korrosion zu vermeiden oder zu bremsen werden Metalle derzeit beschichtet, vor allem mit Lacken, Emaille, Gummi- oder auch metallischen Deckschichten. Das Ziel ist immer das Gleiche: Es gilt, den Werkstoff vor den Kontakt mit korrosionsverursachenden Einflüssen wie Wasser und Luft zu schützen. Dieser konventionelle Korrosionsschutz hat aber zumeist einen Haken: Sie enthalten häufig gesundheitsschädliche Chemikalien wie krebserregende Chrom-6-Salze oder andere giftige Schwermetallverbindungen.
Vorbild des Korrosionsschutzes ist die Haut
Das Max-Planck-Institut für Kolloid- und Grenzflächenforschung in Potsdam hat jetzt ein Verfahren entwickelt, das Beschädigungen des Korrosionsschutzes selbstständig heilen kann. Das Vorbild für diese Technologie ist der Selbstheilungsmechanismus der menschlichen Haut. Wenn diese oberflächlich durch einen Kratzer verletzt wird, dauert es nicht lange, bis die Wunde wieder verschlossen ist. Der Trick der Potsdamer Forscher sind sogenannte Smart Pigments. Basis dafür sind winzigste Makro- und Nanobehälter, die mit organischen Korrosionsschutzmitteln befüllt sind und mit einer Polyelektrolythülle verkapselt sind. Diese Smart Pigments werden dann in eine Korrosionsschutz-Beschichtung eingebettet.
Wenn diese Schutzschicht Kratzer oder Risse bekommt und somit der Prozess der Korrosion beginnt, ändert sich an der defekten Stelle der pH-Wert. Durch diese pH-Wert-Änderung öffnen sich die eingebetteten winzigen Behälter und setzen das darin enthaltene Korrosionsschutzmittel frei. Die verletzte Stelle wird als Folge sofort wieder geschützt und die aggressive Korrosionsreaktion im Ansatz unterbunden. Dadurch normalisiert sich der pH-Wert wieder und die Polyelektrolythülle um die kleinen Behälter verschließen sich, so dass kein weiteres Korrosionsschutzmittel mehr austreten kann.

Auch dieser Truck von MetroWrapz sieht nur verrostet aus.
Quelle: MetroWrapz
Es ist also eine aktive Rückkopplung der Schutzschicht mit der Korrosionsreaktion. Die Vorteile sind klar. So wird das Rostschutzmittel ganz gezielt nur an der verletzen Stelle und auch nur in der zur Korrosionsvermeidung erforderlichen Menge freigesetzt. Der so erzielte Korrosionsschutz hält somit wesentlich länger als ein konventioneller Korrosionsschutz und ist auch sehr viel nachhaltiger. Zudem besticht diese Technologie durch ihre enorme Vielseitigkeit und Flexibilität. Die Größe der Behälter kann an die geplante Schutzanwendung angepasst werden, die Hülleneigenschaften lassen sich je nach Anwendung entsprechend modifizieren. Auch die Art der eingeschlossenen Substanzen und der Freisetzungsmechanismus kann für die Anwendung optimiert werden.
Neue Technik geht jetzt in Serie
Damit diese Technologie seinen Weg in den Markt finden, wurde sie jetzt von Max-Planck-Innovation, der Technologietransfer-Organisation der Max-Planck-Gesellschaft, exklusiv an die 1994 gegründete Firma Enviral Oberflächenversiegelung mit Sitz in Niemegk in Brandenburg vergeben.
Den klassischen Weg der Beschichtung geht dagegen der Ulmer Chemie-Professor Carsten Streb. Seine ionische Flüssigkeit soll nicht nur Metalle, sondern auch historische Gebäuden, Kirchen und Steinskulpturen schützen. Wie, das lesen Sie hier.
Ein Beitrag von: