Bahnbrechende Idee vereinfacht Baumaschinen-Produktion
Fraunhofer-Forscher haben einen Weg gefunden, die Entwicklung von Nutzfahrzeugen und Baumaschinen erheblich zu erleichtern. Mit ihrem Verfahren „Hardware-in-the-Loop“ ermöglichen sie Rapid Prototyping. Sie testen also das Verhalten der Geräte, bevor sie tatsächlich gebaut sind.
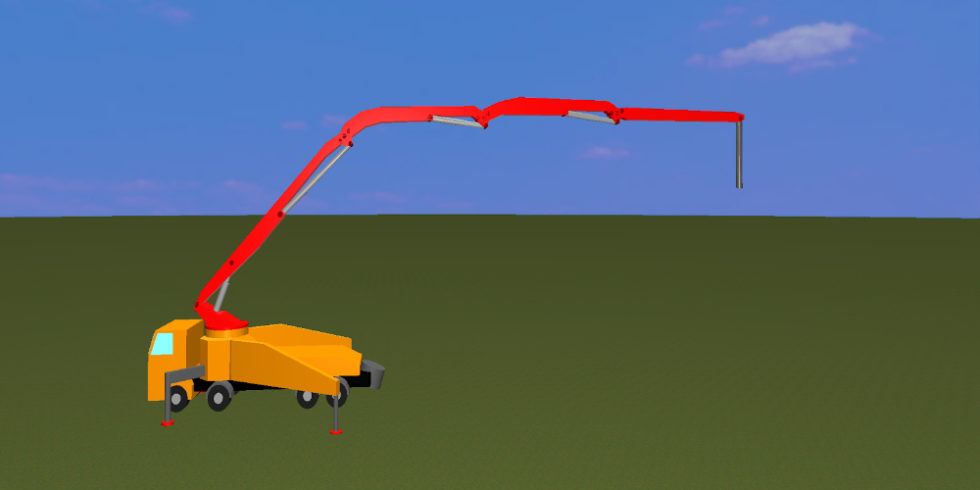
So sieht der digitale Zwilling am Monitor aus. Diese Betonpumpe lässt sich über die Steuereinheit bewegen.
Foto: Fraunhofer ITWM
Baumaschinen müssen sehr hohen Anforderungen genügen. Das betrifft nicht nur ihre Funktionen, sondern auch die Sicherheit. Wenn sie beispielsweise Erde für U-Bahn-Schächte ausheben oder tonnenschwere Lasten in schwindelerregenden Höhen über einer Straße manövrieren, muss jede Bewegung sitzen. Ein Turmdrehkran etwa kann einen tonnenschweren Werkzeugcontainer zentimetergenau auf der Plattform eines Hochhauses ablegen.
Bis es zu dieser Präzision kommt, ist viel Entwicklungsarbeit nötig. Das Bauen und Testen eines Prototypen ist jedoch mit hohen Kosten verbunden – vor allem, wenn sich herausstellt, dass nachgebessert werden muss. Forscher vom Fraunhofer-Institut für Techno- und Wirtschaftsmathematik ITWM in Kaiserslautern bieten jetzt an, dieses Verfahren zu unterstützen und gleichzeitig zu vereinfachen. Dafür haben sie ein Prinzip aus dem normalen Fahrzeugbau auf Nutzfahrzeuge und Baumaschinen übertragen.
Verkürzter Entwicklungszyklus bei Baumaschinen
Die Wissenschaftler haben einen Teststand entwickelt, dessen Herzstück ein sogenannter HiL-Simulator ist. Die Abkürzung steht für Hardware-in-the-Loop. Vereinfacht gesagt, lassen sich mit diesem Verfahren Maschinen und ihre Steuerung über eine Software virtuell testen. Das Prinzip ist nicht neu und bereits aus der Autoindustrie bekannt. Die Hersteller von Nutzfahrzeugen mussten bislang allerdings darauf verzichten. Der Bedarf schien nicht groß genug zu sein. Die Fraunhofer-Wissenschaftler schätzen diese Situation jedoch seit ein paar Jahren anders ein. Die Innovationszyklen bei Baumaschinen und Nutzfahrzeugen würden immer kürzer. Außerdem verändere sich die Bauweise. Sie sei zunehmend modular und digitalisiert. Deswegen sei der neue Teststand notwendig geworden.
„Mit unserem HiL-Simulator sind wir in der Lage, Baumaschinen aller Art zu testen, beispielsweise unterschiedliche Kran-Typen oder auch Betonpumpen. So helfen wir bei der Optimierung der Prototypen“, erklärt Projektleiter Christian Salzig. Die Unternehmen dürften dadurch viel Zeit und Geld sparen, denn auf eine reale Testumgebung können sie verzichten.
Der HiL-Teststand in Aktion
So funktioniert es: Aus den technischen Daten der neuen Maschine bauen die Experten ein Modell, allerdings keinen echten Prototypen, sondern einen digitalen Zwilling, in dem alle Informationen hinterlegt sind. Unter anderem sind das die Abmessungen der Maschine, die Leistungsdaten der Motoren, die Stärke der Stützstrukturen, die Gewichtsverteilung, die Winkel beim Bewegen der Ausleger, deren Länge und natürlich die Steuersignale. In der Software sind zudem alle notwendigen Angaben zu physikalischen Gesetzen der Mechanik, Hydraulik und Elektronik enthalten. Auf diese Weise können die Wissenschaftler zum Beispiel feststellen, welche Kräfte bei einer bestimmten Bewegung des Gerätes auf das Material einwirken.
Jetzt ist alles bereit für den Test: Der digitale Zwilling im Simulator wird an die realen elektronischen Steuereinheiten angeschlossen, mit denen die Baumaschine später bedient werden soll. Das Testen der Maschine wird dadurch vereinfacht, dass alle Bewegungen und Tätigkeiten auf einem Display als animierte 3D-Grafik dargestellt werden.
Komplexe Testreihen
Über den HiL-Simulator werden verschiedene Bereiche abgefragt. Zum Beispiel testen die Forschenden, wie gut die Maschine auf die Steuereinheit reagiert und wie sensibel sich Bedienelemente wie Joysticks verhalten. Ein wichtiger Faktor sind heutzutage außerdem die Sensoren. Unter anderem messen sie permanent Werte wie Drehmoment und Beschleunigung der Ausleger, Druck oder das Gewicht, das an Seilzügen zieht, oder die Neigung des Bodens unter der Maschine. Wieder stellt sich die Frage: Funktioniert alles tadellos? Reagiert die Maschine ohne wesentliche Zeitverzögerung auf die Messdaten? Dazu gehört es natürlich auch, Störungen zu simulieren, etwa ein defektes Kabel.
„Die Hersteller wollen wissen, was ihre Maschine in Grenzbereichen leistet und ab wann es kritisch wird“, sagt Salzig. Sicherheitsrelevante Szenarien gehören daher zwingend zu den Testreihen. Was passiert zum Beispiel, wenn eine Last anfängt zu pendeln oder Flüssigkeiten in einem Transportbehälter hin und her schwappen? Die Forscher können sogar virtuell ausprobieren, ob sich die Maschine neigt, wenn sie auf einem instabilen Untergrund steht. Der besondere Vorteil dabei: Wenn es zu einem Unfall kommt, weil die Baumaschine kippt oder die Last gegen ein nahestehendes Gebäude pendelt, passiert natürlich auch das nur im PC. Es kommt also zu keinen Schäden. Diese komplexen Testreihen führen die Fraunhofer-Experten in enger Zusammenarbeit mit den Herstellern durch.
Eine Erweiterung des Teststands ist übrigens auch schon geplant: Die 5G-Funktechnik soll integriert werden. Eine entsprechende Schnittstelle befindet sich in der Entwicklung.
Mehr lesen über digitale Zwillinge:
- Produktionsplanung mit dem digitalen Zwilling
- Mit Blick aufs Ganze: Digitale Zwillinge im mittelständischen Maschinenbau
- Blockchain sichert den Lebenszyklus „Digitaler Zwillinge“
Ein Beitrag von: