TU Dortmund entwickelt flexible Umformverfahren
Klassische Blechumformtechniken – wie das Tiefziehen – sind auf Massenproduktion ausgelegt. Das aber macht die Fertigung kleiner Losgrößen mit den herkömmlichen Verfahren teuer. Das Institut für Umformtechnik und Leichtbau (IUL) der TU Dortmund entwickelt deshalb flexible Umformverfahren, mit denen individuelle Werkstückgeometrien wirtschaftlich gefertigt werden sollen.
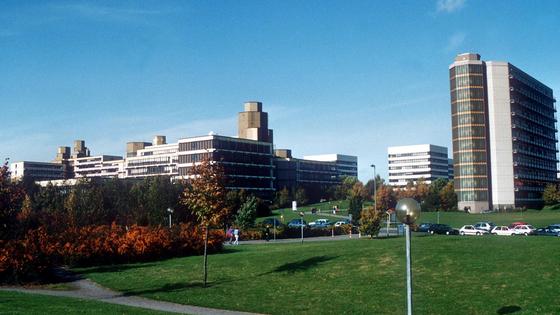
Blechumformung mittels CNC: An der TU Dortmund sucht man nach neuen Möglichkeiten.
Foto: Uni Dortmund
„Beim Blechumformen garantiert hohe Flexibilität auch ein Maximum an möglicher Gewichtsreduktion, da Konstrukteure einen größeren Handlungsspielraum bekommen“, so A. Erman Tekkaya, Leiter des IUL.
Beispielhaft für flexible Fertigungsprozesse sind für ihn die inkrementellen, d. h. stufenweisen Blechumformverfahren. Sie sollen ein Höchstmaß an Flexibilität garantieren, da die Werkstückkontur nicht durch das Werkzeug, sondern durch dessen Bewegung im Raum vorgegeben wird.
Diese Bewegungen können mittels CNC programmiert werden. Somit lassen sich laut IUL nahezu beliebige Werkstückgeometrien für Schalenprodukte wie Kotflügel realisieren. Die Werkzeuge selbst sind von einfacher Gestalt etwa in Form von Stiften oder Walzen.
„In technischer Hinsicht liegt die Herausforderung bei der inkrementellen Umformung darin, dass man den richtigen Werkzeugpfad für die CNC programmiert“, betont Lukas Kwiatkowski, Leiter der Abteilung Sonderverfahren am IUL.
Darüber hinaus wurde zur Reduktion der Fertigungszeit ein Werkzeug entwickelt und patentiert, das zwei Umformzonen besitzt. „Da die Umformzonen getrennt, aber gleichzeitig im Einsatz sind, ist theoretisch die Produktionszeit durch die Anzahl der Werkzeuge zu dividieren“, stellt Tekkaya fest. Praktisch seien allerdings noch kleine Überlappungszonen notwendig, so dass man bei dem zweifach wirkenden Werkzeug von 40 % bis 45 % Zeitersparnis ausgehen könne.
Als weiteres Verfahren wurde das Metalldrücken am IUL so ausgestaltet, dass Rohre, abhängig von der Geometrie, innerhalb von 10 s bis
15 s konturiert werden können. Kwiatkowski unterstreicht: „Dadurch dass wir keinen konturgebenden Dorn im Werkstückinneren verwenden, können wir problemlos mehrere Hinterschnitte und sehr hohe Umformgrade realisieren.“
IUL will Prozesse aus Massiv-Umformverfahren bei Blechwerkstoffen anwenden
Zudem läuft am IUL ein Projekt, das sich mit der inkrementellen Blechmassivumformung beschäftigt. „Hierbei geht es darum, Prozesse, welche bislang nur aus der Massivumformung bekannt sind, auf Blechwerkstoffe anzuwenden“, erläutert Kwiatkowski. Bei diesem von der Deutschen Forschungsgemeinschaft (DFG) geförderten Forschungsschwerpunkt arbeiten die Dortmunder mit weiteren Wissenschaftlern der Universitäten Nürnberg-Erlangen und Hannover zusammen. Hintergrund ist die wirtschaftliche Fertigung von Funktionsbauteilen. Normalerweise werden Bleche stets zu Hohlkörpern verarbeitet und Funktionsbauteile meist nur durch Scher- und Feinschneiden erzeugt.
Die Forscher wollen nun die vorteilhaften Eigenschaften der Massivumformung wie
Faserverlauf und Kaltverfestigung nutzen, um das Bauteilgewicht weiter reduzieren zu können. Im Rahmen des IUL-Projekts hat man sich darauf spezialisiert, Bauteile ganz individuell nach den geforderten Randbedingungen bzw. Belastungen im späteren Einsatzfall herzustellen. „Dazu haben wir zusammen mit dem Sondermaschinenbauer Schnupp Hydraulik aus Bogen in Bayern eine neue, hochpräzise Presse mit mehreren Bearbeitungsachsen entwickelt, mit der wir die gewünschte Flexibilität technologisch umsetzen können“, so Kwiatkowski.
Elektromagnetische Umformverfahren ermöglichen flexible Produktion
Flexibilität in der Produktion ermöglichen zudem elektromagnetische Umformverfahren: „Hierbei wird ein Magnetfeld verwendet, mit dessen Stärke die Kontur des Werkstücks beeinflusst werden kann“, berichtet Tekkaya. Solche elektromagnetischen Umformprozesse eigneten sich hervorragend für elektrisch gut leitende Werkstoffe wie Aluminium. Insbesondere bei schwer formbaren Legierungen lassen sich laut IUL dennoch beeindruckend hohe Umformgrade erzielen.
Neben der reinen Formgebung können Werkstücke mit dieser Technologie auch flexibel miteinander gefügt werden. Dabei seien kraft-, form- und sogar stoffschlüssige Verbindungen möglich. Anders als bei klassischen Schweißverfahren ist man in der Lage, verschiedene Metalle einfach und fast ohne intermetallische Phasen miteinander zu verschweißen.
Auch bei Biegeverfahren wird in Dortmund die Flexibilität großgeschrieben. Die Forscher in Dortmund entwickelten Umformmaschinen, mit denen Rohre und Profile beliebig dreidimensional gekrümmt werden können.
Bei der Massivumformung wurden zur Flexibilisierung des Strangpressens Technologien wie das Runden entwickelt, um Werkstücke während des Strangpressens gleichzeitig dreidimensional zu krümmen. „Diese Verfahren und Prozessketten sind vor dem Hintergrund leichter Tragwerkstrukturen entwickelt worden“, teilt Institutsleiter Tekkaya mit. Die Prozesse seien in der Regel alle bis zur Losgröße 1 einsetzbar.
Ein Beitrag von: