Weniger Fehler durch Elektroden
Ein neues Verfahren entdeckt Produktionsmängel an Schmiedeteilen frühzeitig. Elektroden messen, ob der Schmiedeprozess korrekt verläuft. Die bisher notwendige Fehlersuche nach dem Abkühlen entfällt.
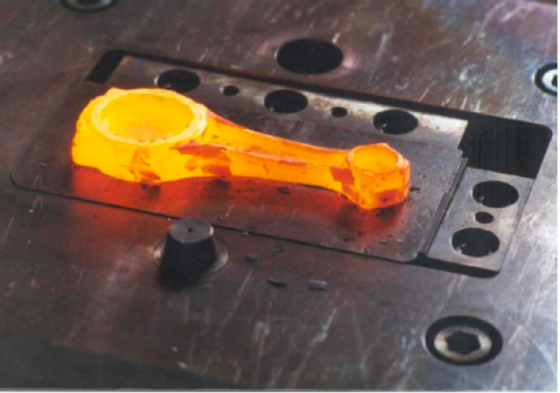
Ausschuss unmittelbar erkennen: Mit intelligenten Werkzeugen sollen unnötige Bearbeitungsschritte beim Schmieden vermieden werden
Foto: IPH
Anders als beim Freiformschmieden wird das Schmiedestück beim Gesenkschmieden vollständig vom sogenannten Gesenk umschlossen. In dieser zweiteiligen Hohlform aus Stahl befindet sich die Gravur, die dem Schmiedestück seine Form gibt. Gesenke sind teuer und ihre Herstellung lohnt sich nur, wenn größere Stückzahlen produziert werden.
Umso wichtiger wird die Kontrolle der einwandfreien Qualität der fertigen Schmiedestücke. Das war bisher nicht einfach. Die häufigsten Schmiedefehler sind Falten und Oberflächenrisse am Bauteil sowie Unterfüllungen der Gesenkgravur. Diese Fehler lassen sich nicht immer durch eine reine Sichtkontrolle erkennen.
Fehlerhafte Schmiedestücke werden spät oder gar nicht erkannt
Deshalb wurde das Schmiedeteil nach dem Abkühlen wärmebehandelt, um seine Beschaffenheit, das sogenannte Gefüge, festzulegen. Fehler wurden erst bei der anschließenden Qualitätskontrolle oder gar nicht erkannt. Eine Prozessüberwachung, die in das Umformwerkzeug integrierbar ist, gibt es derzeit nicht. Sensoren, die dem aktuellen Stand der Technik entsprechen, eignen sich bislang nicht für den direkten Einsatz in den Gesenken, da sie den extrem hohen mechanischen und thermischen Belastungen nicht standhalten.
In dem zweijährigen Forschungsprojekt „Intelligente Schmiedewerkzeuge zur Fehlerreduktion in der Massivumformung“ haben Wissenschaftler am Institut für Integrierte Produktion Hannover (IPH) jetzt ein Verfahren entwickelt, mit dem Fehler bereits während des Schmiedeprozesses erkannt werden können. Die korrekte Füllung der Form wird überwacht und die Prozessdaten gehen drahtlos zum Computer.
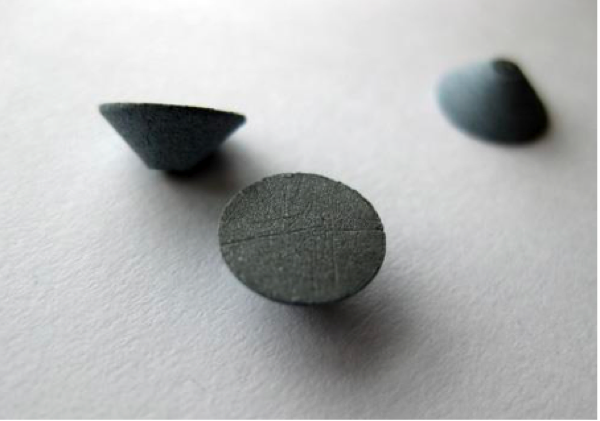
Elektroden wie diese Kegelelemente wurden am IPH in das Gesenk integriert, um frühzeitig mangelhafte Formfüllungen zu erkennen.
Quelle: IPH
Dazu integrierten die Forscher isolierte Elektroden an ausgewählten Stellen im Gesenk. Kommt das Werkstück bei der Umformung mit der Elektrode in Kontakt, schließt sich der Stromkreis und der Strom fließt. Das Stromsignal können die Mitarbeiter am Computer überwachen.
Kostenersparnis durch die Überwachung des Schmiedeprozesses
Mit der neuen Überwachung des Schmiedeprozesses soll die Ausschussrate und der Material- und Personaleinsatz reduziert werden. Das bringe, so die Wissenschaftler, den deutschen Schmiedeunternehmen einen Vorsprung an Know-how gegenüber der Konkurrenz aus dem Ausland. Die Anwendung sei einfach, robust und finanziell wenig aufwendig, so dass sie besonders auch für klein- und mittelständische Unternehmen interessant sei. Die konnten sich automatisierte Prozessüberwachungen bisher kaum leisten.
Auch für andere Bereiche der Metallwirtschaft sehen die Forscher Anwendungsmöglichkeiten. Als Hauptabnehmer von Schmiedeteilen profitiere auch der Fahrzeugbau von den Ergebnissen, da bestehende Bauteile zukünftig effektiver und kostengünstiger produziert werden könnten. Eine robuste und industrieerprobte drahtlose Datenübertragung sei zudem für weitere Bereiche des Maschinenbaus interessant.
Ein Beitrag von: