Neues Raketentriebwerk mit Aerospike-Düse für Microlauncher
Wissenschaftler in Dresden haben ein neues Raketentriebwerk entwickelt. Das Besondere: Es wird Schicht für Schicht nach dem Prinzip der additiven Fertigung hergestellt. Als Einsatzgebiet sind mittelgroße Transportsysteme geplant.
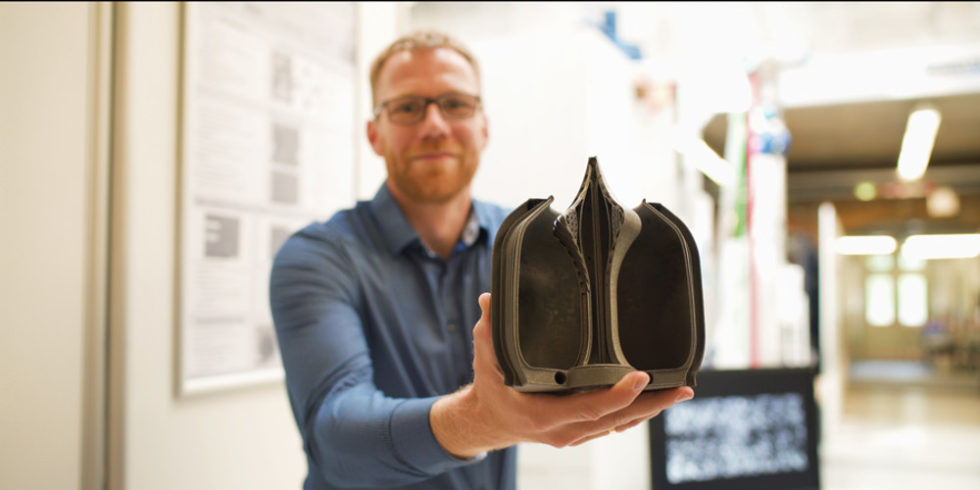
Dieser Prototyp könnte ein wichtiger Schritt auf dem Weg zu einem innovativen Raketenantrieb sein.
Foto: Tobias Ritz
Kleine bis mittelgroße Trägerraketen, auch Microlauncher genannt, sind derzeit sehr gefragt. Voraussichtlich wird sich der Markt auch weiterhin gut entwickeln. Zwei Beispiele: Großbritannien möchte im Norden Schottlands den ersten Weltraumbahnhof auf europäischem Boden errichten, und der Bundesverband der Deutschen Industrie (BDI) fordert einen Weltraumbahnhof für Deutschland. Hier kommen die Trägerraketen ins Spiel. Sie sind dafür gedacht, von solch einer Basis aus Forschungsinstrumente und kleine Satelliten ins All zu transportieren. Ihre maximale Nutzlast liegt dafür bei 350 Kilogramm. Umso wichtiger ist es, sie mit Triebwerken zu bestücken, die kein großes Eigengewicht haben und einen entsprechend geringen Treibstoffverbrauch.
Genau an diesem Projekt hat ein Forscherteam des Instituts für Luft- und Raumfahrttechnik der TU Dresden zusammen mit dem Dresdner Fraunhofer-Institut für Werkstoff- und Strahltechnik IWS gearbeitet. Herausgekommen ist dabei ein additiv gefertigtes Raketentriebwerk mit Aerospike-Düse. Der skalierte Prototyp aus Metall soll bis zu 30 % weniger Treibstoff als herkömmliche Triebwerke verbrauchen. Außerdem passt sich die Düse nach Angaben der Forscher den Druckverhältnissen im Orbit besser an. Dadurch sei sie effizienter, was neben dem geringen Gewicht zur Treibstoffersparnis beitrage.
Aus Metall-Pulver wird Schicht für Schicht ein Triebwerk
Das Raketentriebwerk besteht im wesentlichen aus Treibstoffinjektor, Brennkammer und Düse – jedes Bauteil wird über das additive Fertigungsverfahren Laser Powder Bed Fusion (L-PBF) in einzelnen Schichten hergestellt. Die Düse selbst besteht aus einem stachelförmigen Zentralkörper, der dazu dient, die Verbrennungsgase zu beschleunigen. „Die technologische Konzeption der Aerospike-Triebwerke ist erstmals in den 1960er Jahren aufgekommen. Aber nur durch die Freiheiten der additiven Fertigung und die Einbettung dieser in konventionelle Prozessketten ist es uns möglich, so effiziente Triebwerke überhaupt herzustellen“, sagt Michael Müller, wissenschaftlicher Mitarbeiter am Additive Manufacturing Center Dresden (AMCD), das gemeinsam von der TU Dresden und dem Fraunhofer IWS betrieben wird.
Für eine Triebwerksdüse sind die Anforderungen an das Material hoch. Metall ist ideal, weil es bei hohen Temperaturen fest bleibt und Wärme gut leiten kann. Das ist wichtig, damit die Kühlung funktioniert. Für die additive Herstellung wird das Material-Pulver zunächst klassisch Schicht für Schicht aufgetragen und anschließend selektiv per Laser aufgeschmolzen. So entsteht in vielen einzelnen Schritten das jeweilige Bauteile inklusive der benötigten Kühlkanäle. Sie sind einen Millimeter breit und entsprechen der Kontur der Brennkammer. Anschließend werden Pulverreste aus den Kanälen herausgesaugt.
Additive Fertigung ermöglicht verschlungene Strukturen
So einfach das Verfahren klingt, umfassende Vorbereitungen waren nötig, ehe die Wissenschaftler mit der Herstellung des ersten Triebwerks starten konnten. Zunächst passten sie das Design so an, dass die additive Fertigung in Schichten überhaupt möglich war. Anschließend wählten sie das Material aus. Per Laser Powder Bed Fusion druckten sie das Triebwerk schließlich aus zwei Komponenten und verbesserten die Funktionsflächen durch eine gezielte Nachbearbeitung. Dann konnten sie die Bauteile zusammenfügen, wofür sie das Verfahren des Laserstrahlschweißens wählten. Eine Computertomografie (CT) half ihnen am Ende dabei, die neue Düse auf mögliche Fehler zu überprüfen. Die CT zeigt unter anderem an, ob alle Kühlkanäle frei sind oder ob sich noch Pulverrückstände in ihnen befinden. Nach Angabe der Forscher wäre es nicht möglich gewesen, die verschlungenen Strukturen des Kühlsystems auf konventionelle Weise zu fräsen oder zu gießen.
Der spannendste Moment stand den Forschern aber ohne Frage auf dem Teststand des Instituts für Luft- und Raumfahrttechnik der TU Dresden bevor, wo sie den Prototypen des Aerospike-Triebwerks in Gang setzten. Sie erzielten eine Brenndauer von 30 Sekunden.
„Das ist ein besonderer Vorgang, denn bislang gibt es noch kaum Tests von Aerospike-Düsen“, sagt Müller. „Wir haben nachgewiesen, dass sich mittels additiver Fertigung ein funktionierendes Flüssigkeitstriebwerk herstellen lässt.“
Lesen Sie mehr zum Thema Raumfahrt:
Ein Beitrag von: