Neue Enteisungstechnik für Flugzeugoberflächen
Fraunhofer Forscher entwickeln gemeinsam mit Partnern aus Europa und Japan eine neue Technik zur Enteisung von Flugzeugoberflächen. Flieger der neuen Generation, die aus leichten carbonfaserverstärkten Kunststoffen (CFK) gebaut werden, sollen künftig damit ausgestattet werden.
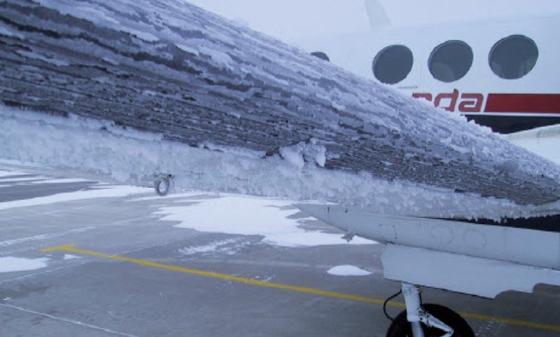
Vereiste Tragflächen: Fraunhofer Forscher entwickeln gemeinsam mit Partnern aus Europa und Japan eine neue Technik zur Enteisung von Flugzeugoberflächen.
Foto: Fraunhofer IGB
Auf dem Weg zum Flugziel befinden sich Flugzeuge in Höhen von 10 000 Metern, wo extrem niedrige Temperaturen bis zu -50 Grad Celsius herrschen. Dort oben in der Atmosphäre sind sie den Wolken und Niederschlägen ausgesetzt, durch die sich Eis an den Flügeln bilden kann.
Da dies zu massiven Problemen führen kann, werden schon jetzt enorme Anstrengungen unternommen, um der Eisbildung entgegenzuwirken. Insbesondere dort wo die Aerodynamik negativ beeinflusst wird oder das Gewicht des Flugzeugs stark zunimmt, kann es sehr gefährlich werden. Derzeit wird die Abwärme der Triebwerke zum Aufheizen der Flügelvorderkanten verwendet. Aber auch die mechanische Eisentfernung mit den sogenannter „rubber boots“ kommt zum Einsatz. Dies sind Gummimatten, die Luftkammern enthalten und sich bei Bedarf aufpumpen lassen. Auf diese Weise wird das Eis von der Oberfläche abgesprengt.
Vereisungsbedingte Vorfälle bis zu 80 Prozent reduzieren
Besonders wichtig ist es jedoch, eine Eisbildung frühzeitig zu erkennen und zu verhindern. Dafür startete im November 2012 das japanisch-europäische Projekt „JEDI ACE“ (Japanese-European De-Icing Aircraft Collaborative Exploration), an dem das Fraunhofer-Institut für Fertigungstechnik und Angewandte Materialforschung IFAM beteiligt ist. Ziel ist es, ein System zu entwickeln, das bereits während des Fluges vereisungsbedingte Vorfälle bis zu 80 Prozent reduzieren kann und zudem deutlich weniger Energie benötigt. Dafür sollen neue Enteisungstechnologien und Echtzeitsensoren miteinander kombiniert werden. Der Schwerpunkt der Entwicklung liegt auf den Sicherheits- und Effizienzaspekten.
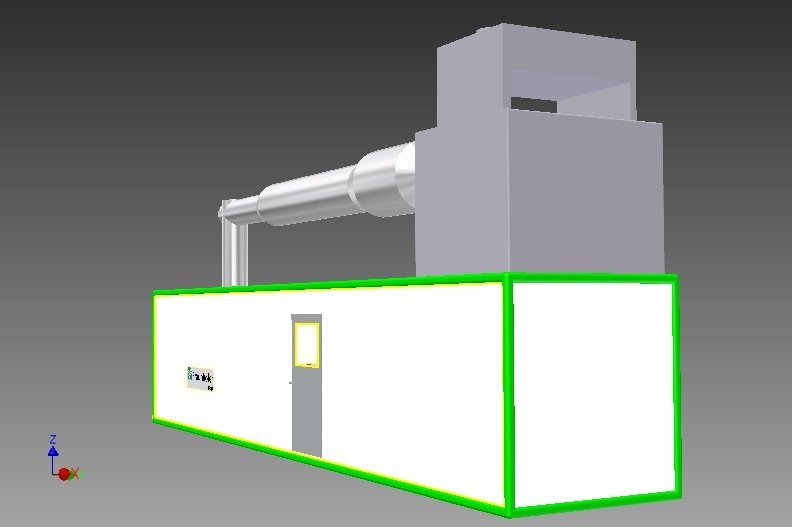
Skizze des Fraunhofer IFAM Windkanals, in dem zukünftig Vereisungstests unter realitätsnahen Bedingungen durchgeführt werden können.
Quelle: Fraunhofer IFAM
Im Rahmen des „JEDE ACE“ Projekts entwickelten die Fraunhofer-Forscher einen Windkanal, in dem das neue Enteisungssystem getestet werden kann. Mit Temperaturen bis zu -30 Grad Celsius und Windgeschwindigkeiten bis 350 Stundenkilometer schaffen sie realitätsähnliche Verhältnisse für ihre Untersuchungsarbeiten.
Neue Technik besteht aus drei synergistischen Komponenten
Eine aktive Enteisungstechnik, die funktionale Beschichtung zur Unterstützung der Enteisungsfunktion und eine Sensortechnik, die nicht nur die Vereisung, sondern auch die Enteisung in Echtzeit überwacht: Diese drei Komponenten bilden das neue Enteisungssystem.
Die funktionale Beschichtung soll auf thermischem oder mechanischem Wege eine Enteisung unterstützen und durch Reduktion der Eis-Haftung eine Entfernung vereinfachen. Die Forscher des Fraunhofer IFAM führen daher umfangreiche Tests zum Vereisungsverhalten auf den Oberflächen durch. „Die Herausforderung hierbei ist, dass die Beschichtungen ihre Funktion trotz der am Flugzeug auftretenden hohen Belastungen wie Erosion und UV-Strahlung über mehrere Jahre behalten müssen. Hierzu arbeiten wir derzeit an Lacksystemen, die diese Dauerbeständigkeit erreichen“, erklärt Nadine Rehfeld, Lacktechnik-Expertin und wissenschaftliche Leiterin des internationalen Projekts.
„Shape-Memory-Materialien“ für einfachere Eisentfernung
Eine Veränderung der Flugzeugoberflächen mit den sogenannten „Shape-Memory-Materialien“ als mechanische Aktuatoren könnte die Eisentfernung um ein Vielfaches vereinfachen.
Erste Ergebnisse dieser Tests wurden bei einem Projekttreffen im Mai 2013 in Tokio vorgestellt. Dort diskutierten die Projektpartner aus Frankreich, Spanien, Japan, über das weitere Vorgehen bei JEDE ACE.
Mit dem neuen Enteisungssystem hoffen die Forscher auch das Sicherheitsrisiko einzuschränken, das durch CO2-Emissionen entsteht. Nach Angaben der Datenbank der US-amerikanischen Zulassungsbehörde Federal Aviation Administration (FAA) gab es im Zeitraum von 1998 bis 2007 insgesamt 886 Vorfälle, die mit Vereisung zusammenhingen.
Die Europäische Kommission und das Japanische Ministerium für Wirtschaft, Handel und Industrie (METI) fördern dieses Projekt. Koordination und wissenschaftliche Leitung obliegen dem Fraunhofer IFAM in Bremen.
Ein Beitrag von: