Neue Metalllegierung bereitet Weg für industrielle Thermoelektrik
Mit thermoelektrischen Modulen in Abgasanlagen von PKWs ließen sich jedes Jahr Millionen Tonnen CO2 einsparen. Bislang steckte die Technologie in den Kinderschuhen. Jetzt ebnet eine neue Metalllegierung den Weg zur industriellen Massenproduktion.
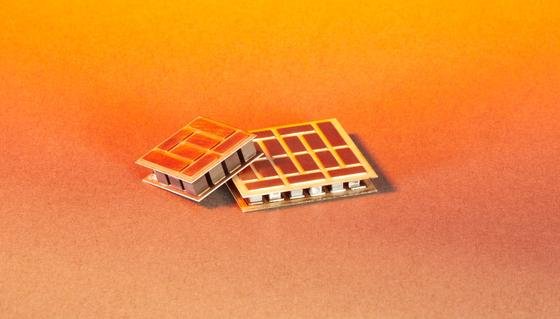
Halb-Heusler-Verbindungen eignen sich besonders gut, um thermoelektrische Module herzustellen. Mit diesen lässt sich aus Abwärme Strom gewinnen. Forschern ist es erstmals gelungen, einen kritischen Effizienz-Wert zu überschreiten und die Metalllegierung im Kilomaßstab herzustellen.
Foto: Fraunhofer-IPM/K.-U. Wudtke
Egal ob in Industrie, Heizungsanlagen oder Autos: Mehr als zwei Drittel der Primärenergien Öl und Gas gehen heute als Abwärme verloren. Um dieses Potential ausschöpfen zu können, arbeiten Forscher weltweit fieberhaft an thermoelektrischen Modulen, die beispielsweise in der Abgasanlage von PKWs Temperaturunterschiede in Strom umwandeln könnten.
„In Deutschland waren 2013 zu Jahresbeginn fast 60 Millionen Fahrzeuge registriert. Wären diese alle mit kleinen thermoelektrischen Kraftwerken an der Abgasanlage ausgerüstet, ließe sich theoretisch schon heute Energie in einer Größenordnung einsparen, wie sie ein Kernkraftwerk jährlich produziert“, erklärt Dr. Kilian Bartholomé vom Freiburger Fraunhofer-Institut für Physikalische Messtechnik (IPM). „Das entspricht in etwa einer Ersparnis von mehreren Millionen Tonnen CO2.“
Und obwohl die wesentlichen Prinzipien der Thermoelektrik schon seit fast 200 Jahren bekannt sind, steckt die Technologie immer noch in den Kinderschuhen. Bislang fehlen geeignete Materialien und Herstellungsverfahren. Jetzt allerdings ist ein entscheidender Entwicklungsschritt gelungen.
Halb-Heusler-Verbindungen sind Hoffnungsträger für Thermomodule
Thermoelektrische Module sind aus wenigen Millimeter großen Klötzchen zusammengesetzt, die aus zwei unterschiedlichen Typen thermoelektrischen Materials bestehen. Der sogenannte Seebeck-Effekt sorgt dafür, dass in einem Stromkreis aus zwei verschiedenen elektrischen Leitern bei einer Temperaturdifferenz zwischen den Kontaktstellen eine elektrische Spannung entsteht. Somit lässt sich Wärme in Strom umwandeln.
Forscher haben gezeigt, dass sich Halb-Heusler-Verbindungen wesentlich effizienter und kostengünstiger herstellen lassen. Diese Metalllegierungen eignen sich besonders gut für die thermoelektrische Anwendung und erfüllen fast alle dafür notwendigen Kriterien. „Sie bestehen aus weit verbreiteten Rohstoffen, zum Beispiel Nickel, sind wesentlich umweltverträglicher als bisher eingesetzte Materialien, verfügen über gute thermoelektrische Eigenschaften und halten hohe Temperaturen aus“, erklärt Dr. Benjamin Balke von der Universität Mainz. Der Experte für Materialentwicklung sucht im Rahmen des Forschungsprojekts „thermoHEUSLER“ nach dem perfekten Material für thermoelektrische Module. Sponsor ist das Bundesministerium für Wirtschaft und Technologie (BMWi).
Kritischen ZT-Wert erstmals überschritten
Der ZT-Wert gibt an, wie effektiv ein Material bei dieser Umwandlung ist. Damit die Industrie Massenproduktion überhaupt in Betracht zieht, muss das Material einen ZT-Wert größer eins erreichen. Mit 1,2 habe man diese kritische Schwelle für Halb-Heusler-Verbindungen erstmals überschritten, sagt Bartholomé. „Das entspricht den besten bisher veröffentlichten Werten für Halb-Heusler-Verbindungen.“ Mit einem eigens entwickelten Lötsystem haben die Forscher zudem eine weitere Schwachstelle der thermoelektrischen Module behoben: die elektrischen Kontakte. Sie können jetzt großen Temperaturunterschieden standhalten, sind langzeitstabil und halten gleichzeitig den elektrischen Widerstand gering.
Isabellenhütte stellt Legierung im Kilomaßstab her
Der nächste Schritt ist es nun, diesen ZT-Wert aus dem Labor auch in der Massenproduktion zu erreichen. Auf diesem Weg sind die Forscher nicht allein. Am Projekt beteiligt sind auch eine Vakuumschmelze aus Hanau und die Isabellenhütte in Dillenburg, Hersteller von Thermo- und Widerstandslegierungen. Diesen beiden Praktikern ist es bereits gelungen, das Halb-Heusler-Material im Kilogrammmaßstab herzustellen. Der deutsche Bergbauingenieur und Chemiker Friedrich Heusler, Namensgeber der Legierung, war vor seinem Tod im Jahr 1947 Besitzer der Isabellenhütte.
Ein Beitrag von: