Turbinenschaufel aus Zellulose statt aus Metall
Forschern in Singapur ist es erstmals gelungen, ein großes Bauteil aus Zellulose und einem natürlichen Kleber per 3D-Druck herzustellen. Es ist so fest, dass es als Schaufel in einer Turbine eingesetzt werden kann.
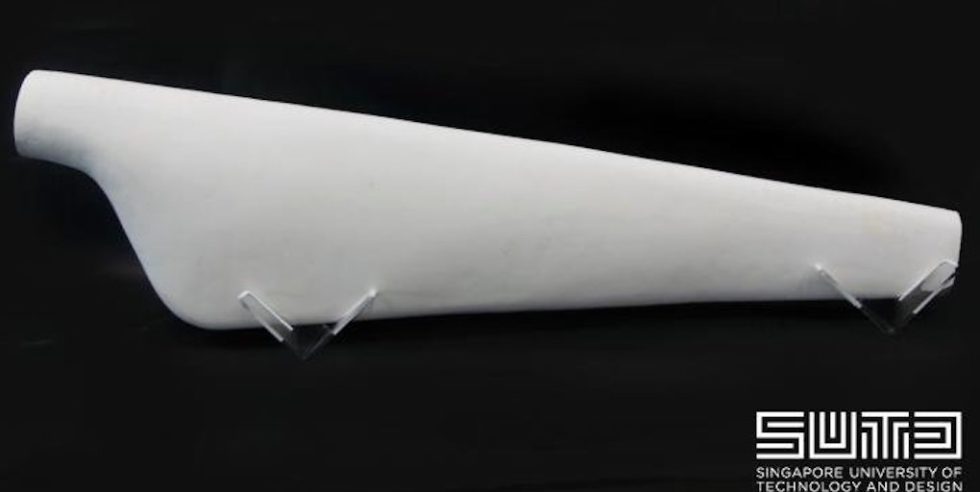
Umweltfreundlich: Die 1,2 m große, 5,2 kg schwere Turbinenschaufel besteht vollständig aus Zellulose und Chitosan, einem Kleber, der in den Zellwänden von Pilzen vorkommt.
Foto: SUTD
Turbinenschaufeln von Wasserkraftwerken und andere große Bauteile, die heute aus massivem Metall herausgefräst werden, bestehen künftig möglicherweise aus Zellulose. Das ist das faserige Naturmaterial, das Bäumen in Kombination mit dem Kleber Lignin ihre Festigkeit verleiht.
Turbinenschaufel ist 1,2 Meter lang
Was etwas utopisch klingt, weil man Zellulose eher mit Papier als mit einem hochfesten Material in Verbindung bringt, ist jedoch Wirklichkeit. Forscher der Singapore University of Technology and Design haben eine Turbinenschaufel hergestellt, die 1,2 m lang und nur 5,2 kg schwer ist. Die nötige Festigkeit verleiht dem Bauteil Chitosan, ein hochwirksamer Kleber aus dem Reich der Natur. Das Biopolymer kommt in den Zellwänden von Pilzen vor. Es wird aus einem anderen Naturprodukt gewonnen, das ebenfalls in Pilzen vorkommt: aus Chitin.
Bauteile lassen sich wie Holz bearbeiten
FLAM nennen die Forscher aus Singapur ihren Werkstoff, das steht für Fungal-like adhesive material, also pilzähnliches haftendes Material. Wie schon die Turbinenschaufel zeigt, ist FLAM sehr leicht, jedoch äußerst fest. Es lässt sich preisgünstig herstellen, weil die verwendeten Werkstoffe im Überfluss vorhanden sind. Von den Kosten her soll es mit Kunststoffen vergleichbar sein, die allerdings weitaus weniger belastbar sind.
Sollte das Bauteil nicht exakt die gewünschte Form haben, lässt es sich nachträglich wie Holz bearbeiten. Man kann es zersägen, schleifen oder zerspanen. Wenn es nicht mehr gebraucht wird, lässt es sich kompostieren.
Umweltfreundlich und recycelbar
„Wir glauben, dass dieser erste additive Fertigungsprozess für große Bauteile aus einem universell verfügbaren Rohstoff eine Art Katalysator ist für die Hinwendung zu umweltfreundlichen und recycelbaren Produkten“, so Juniorprofessor Javier Gomez Fernandez. Außer Cellulose und Chitosan benötigen die Forscher aus Fernost noch Essigsäure, ebenfalls ein Naturprodukt. Vermutlich ist sie das Lösungsmittel für Chitosan – 3D-Druck benötigt als Ausgangsmaterial ein Pulver oder eine Paste. Es wird Schicht für Schicht aufgebaut und jeweils gehärtet. Wie sie diesen Prozessschritt gelöst haben verraten die Forscher nicht.
„Wir haben mit unserem Verfahren möglicherweise den technisch aussichtsreichsten Vorstoß im Bereich von bionischen Materialien unternommen“, so Fernandez. Bionische Materialien sind Nachbauten natürlicher Strukturen. FLAM könnte einen Teil der Probleme lösen, die Kunststoffe verursachen. Erdöl würde durch nachwachsende Rohstoffe ersetzt. Auch die Vermüllung der Meere ließe sich verlangsamen.
Forscher suchen jetzt einen Industriepartner
Bis dahin ist der Weg allerdings noch weit. „Bisher haben wir ausschließlich Forschungsarbeit geleistet“, sagt Juniorprofessor Stylianos Dritsas, der ebenfalls zum Entwicklungsteam gehört. „Jetzt sind wir an einem Punkt angekommen, an dem wir Industriepartner benötigen, um das Material aus dem Labor in die Welt zu entlassen.“
Mit Zellulose experimentiert wird auch am Hamburger Teilchenbeschleuniger DESY. Dort hat ein Forscherteam jetzt das stärkste Biomaterial hergestellt, das jemals produziert worden ist. Die Superfaser lässt sogar Spinnenseide, die als stärkstes Material auf Erden gilt, alt aussehen. Gleich achtmal stärker ist die Faser, die aus Zellulose-Nanofasern durch Werkstoff-Zaubertricks entsteht.
Ein Beitrag von: