Dünne Membranen trennen CO2 effizient und günstig ab
Es gibt zahlreiche industrielle Prozesse, bei denen sich CO2 nicht gänzlich vermeiden lässt. Es abzutrennen und zu speichern, ist deshalb ebenso relevant. Forschende der EPFL haben nun einen neuen Weg gefunden, wie mit besonderen Membranen CO2 effizient und günstig abgetrennt werden kann.
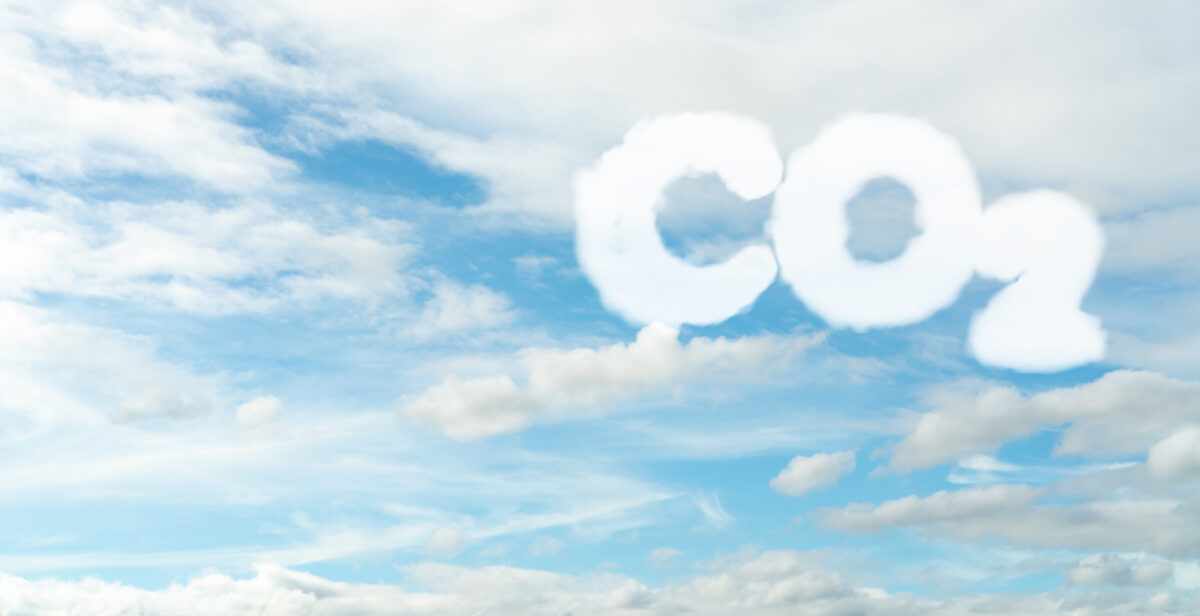
Forschende haben erstmals eine extrem dünne Graphenmembran mit Pyridinstickstoff an den Porenrändern entwickelt, die sehr gut CO2 abtrennt.
Foto: panthermedia.net/ Fahroni
Ein relevantes Mittel gegen den Klimawandel ist die Reduzierung von CO2. Doch da sich nicht in allen Anwendungsbereichen genügend CO2 einsparen lässt, ist auch die Abscheidung, Nutzung und Speicherung dieses Gases von großer Relevanz. Denn dadurch kann es gelingen, die Emissionen vor allem auch dort zu verringern, wo es sonst nur schwer möglich ist – unter anderem in Kraft- und Stahlwerken, Zementfabriken oder Müllverbrennungsanlagen. Die Abscheidung von CO2 gehört in vielen Anlagen bereits heute ganz selbstverständlich dazu. Doch Methoden und Prozess sind in der Regel energieintensiv und damit teuer und wenig nachhaltig. Soll der Kampf gegen den Klimawandel also gelingen, braucht es effiziente und kostengünstige Technologien, mit denen sich Kohlenstoff abscheiden lässt.
Start der ersten großtechnischen Anlage zur CO2-Abscheidung und -Verwertung in der Zementproduktion
Ein Forscherteam an der Ecole polytechnique fédérale de Lausanne (EPFL) hat sich deshalb mit der Entwicklung einer besonderen Membran beschäftigt, die nicht nur CO2 sehr effizient einfängt, sondern dabei auch wenig Energie benötigt und nur geringe Kosten verursacht. Bislang kamen unter anderem dünne Polymermembrane zum Einsatz. Sie sind war hinsichtlich der Kosten überschaubar, dafür aber in ihrer CO2-Durchlässigkeit und -Selektivität beschränkt. Was sie zugleich auch in ihrer Skalierbarkeit hemmt. Genau hier setzte das Forscherteam an. Sie sollten eine Membran mit hoher CO2-Durchlässigkeit und -Selektivität entwickeln, die Kohlenstoff besonders wirksam abscheidet.
Membran, die effizient CO2 abtrennt, ist extrem dünn
Das Forscherteam konzentrierte sich bei der Entwicklung auf eine Membran, die aus einer porösen, zweidimensionalen selektiven Schicht besteht. Eine besondere Rolle spielte dabei die Einlagerung von Pyridinstickstoff an den Rändern der Graphenporen. Zuerst synthetisierte das Team einschichtige Graphenfilme mithilfe chemischer Gasphasenabscheidung auf einer Kupferfolie. Anschließend erfolgte eine kontrollierte Oxidation mit Ozon, wodurch Poren im Graphen entstanden. Durch weitere Sauerstoffatome wurden daraus funktionalisierte Poren. Im nächsten Schritt bauten die Forschenden Stickstoffatome in Form von Pyridin-N am Rand der Poren ein. Dafür mussten sie oxidierte Graphen bei Raumtemperatur mit Ammoniak reagieren lassen.
Das Ergebnis zeigte: Den Forschenden war es gelungen, Pyridinstickstoff erfolgreich einzubauen und so die Bildung von CO2-Komplexen an den Porenrändern auszulösen. Daran hatten auch der Einsatz verschiedener Techniken einen großen Anteil, unter anderem der Röntgen-Photoelektronenspektroskopie und die Rastertunnelmikroskopie. Die Forschenden beobachteten, dass durch den Einbau des Pyridinstickstoffs das CO2 sich besser an die Graphenporen binden konnte. Vor dem Einsatz von Pyridinstickstoff hatten Forschende vor allem die zweidimensionalen Unterschiede der Poren in der Molekülmasse oder -größe ausgenutzt. Die attraktive Kombination, die den EPFL-Forschenden gelang, ist eine absolute Neuheit.
CO2-Trennfaktor der neu entwickelten Membran extrem gut
Nach erfolgreicher Entwicklung testeten die Forschenden die neue Membran. Auch das Ergebnis verlief positiv: Die Membranen wiesen einen hohen CO2/N2-Trennfaktor auf. Der Durchschnitt des Gasstroms lag dabei bei 53 und der CO2-Wert bei 20 Prozent. Bei weiteren Tests ergab sich, dass Ströme mit rund 1 Prozent CO2 sogar Trennfaktoren von über 1.000 erreichten. Das sei aufgrund der konkurrierenden und reversiblen Bindung des CO2 an den Rändern der Poren möglich. Der Pyridinstickstoff erleichtere dabei diese Bindung.
Nun ging es in weiteren Tests noch darum zu zeigen, ob diese besonderen Membranen sich in der Herstellung als skalierbaren Prozess darstellen ließen. Auch das gelang ihnen. Die Hochleistungsmembranen können nach Ansicht der Forschenden im Zentimetermaßstab hergestellt werden. Mit dieser Größe sind sie auch für den Einsatz in großen industriellen Anlagen geeignet.
Erster Schritt, um weitere Lösungen zu entwickeln, CO2 abzutrennen
Entscheidend sei aus Sicht der Forschenden, dass die Graphenmembran extrem leistungsfähig sei und CO2 zuverlässig abscheiden könne. Das gelinge sogar aus verdünnten Gasströmen. Damit ließen sich Kosten und auch Energiebedarf für derartige Abscheidungsprozesse deutlich reduzieren. Die Forschenden sind sich sicher, mit ihrer Innovation nicht nur neue Wege in der Membranwissenschaft eröffnet zu haben, sondern auch den Weg aufgezeigt hätten, wie sich nachhaltigere und wirtschaftlichere CCUS-Lösungen entwickeln ließen. Der nächste Schritt steht auch bereits an. Das Team ist dabei, die Membranen in einem kontinuierlichen Roll-to-Roll-Prozess herzustellen.
Ein Beitrag von: