Mikroben verarbeiten Rauchgas von Kohlekraftwerken zu Bioplastik
Die Rauchwolken stehen imposant über den riesigen Kohlekraftwerken am Niederrhein und in der Lausitz: Was wie Wolken aussieht, ist ein Klimakiller. Jetzt haben Ingenieure ein Verfahren entwickelt, das die Abgase als Rohstoff nutzt. Mikroben produzieren aus dem Rauch Bioplastik.
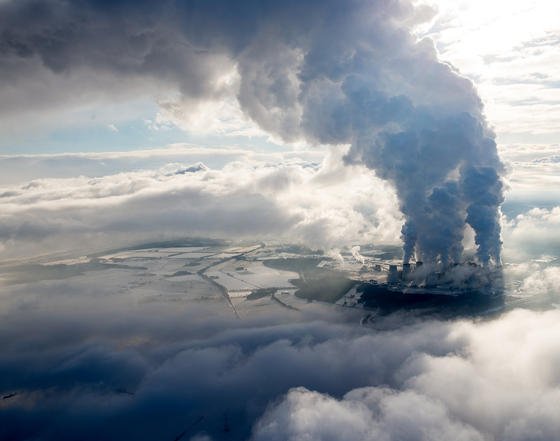
Mächtige Wasserdampfsäulen des Braunkohlekraftwerkes in Janschwalde in der Lausitz: Forscher haben ein neues Verfahren entwickelt, bei dem Mikroben das Rauchgas von Kohlekraftwerken nutzen, um aus dem enthaltenen CO
Foto: Patrick Pleul/dpa
Das Verfahren haben gerade die Forscher des Karlsruher Instituts für Technologie (KIT) vorgestellt. Ihre Idee: Der im Rauchgas enthaltene Kohlenstoff wird als Rohstoff für die Kunststoffproduktion genutzt. Guter Nebeneffekt: Das klimaschädliche CO2 wird beseitigt.
Grundlage des neuen Verfahrens ist eine recht neue Technologie – die mikrobielle Elektrosynthese. Erst vor rund sechs Jahren konnten Forscher in den USA zeigen, wie bestimmte Mikroorganismen auf einer Kathode als alleinige Energie- und Elektronenquelle wachsen und dabei Kohlendioxid fixieren können.
Diese Arbeiten waren der Ausgangspunkt für die Arbeit der Wissenschaftler vom Institut für Angewandte Biowissenschaftler (IAB) am KIT. Mit der mikrobiellen Elektrosynthese war es bisher nur möglich, einfache Substanzen wie die Salze der Essigsäure herzustellen. Eine Kohlenstoffindustrie sieht anders aus.
„Dem menschlichen Atmungsprozess recht ähnlich“
„Wir haben den Prozess dahingehend optimiert, dass wir den Mikroorganismen mehr Energie zur Verfügung stellen, sodass sie komplexere Moleküle – zum Beispiel Polymere – produzieren können“, erklärt Johannes Eberhard Reiner vom IAB. „Dazu mischen wir das CO2 mit Luft. Die Mikroorganismen können dann den Sauerstoff als Elektronenakzeptor nutzen“, erklärt der Forscher.
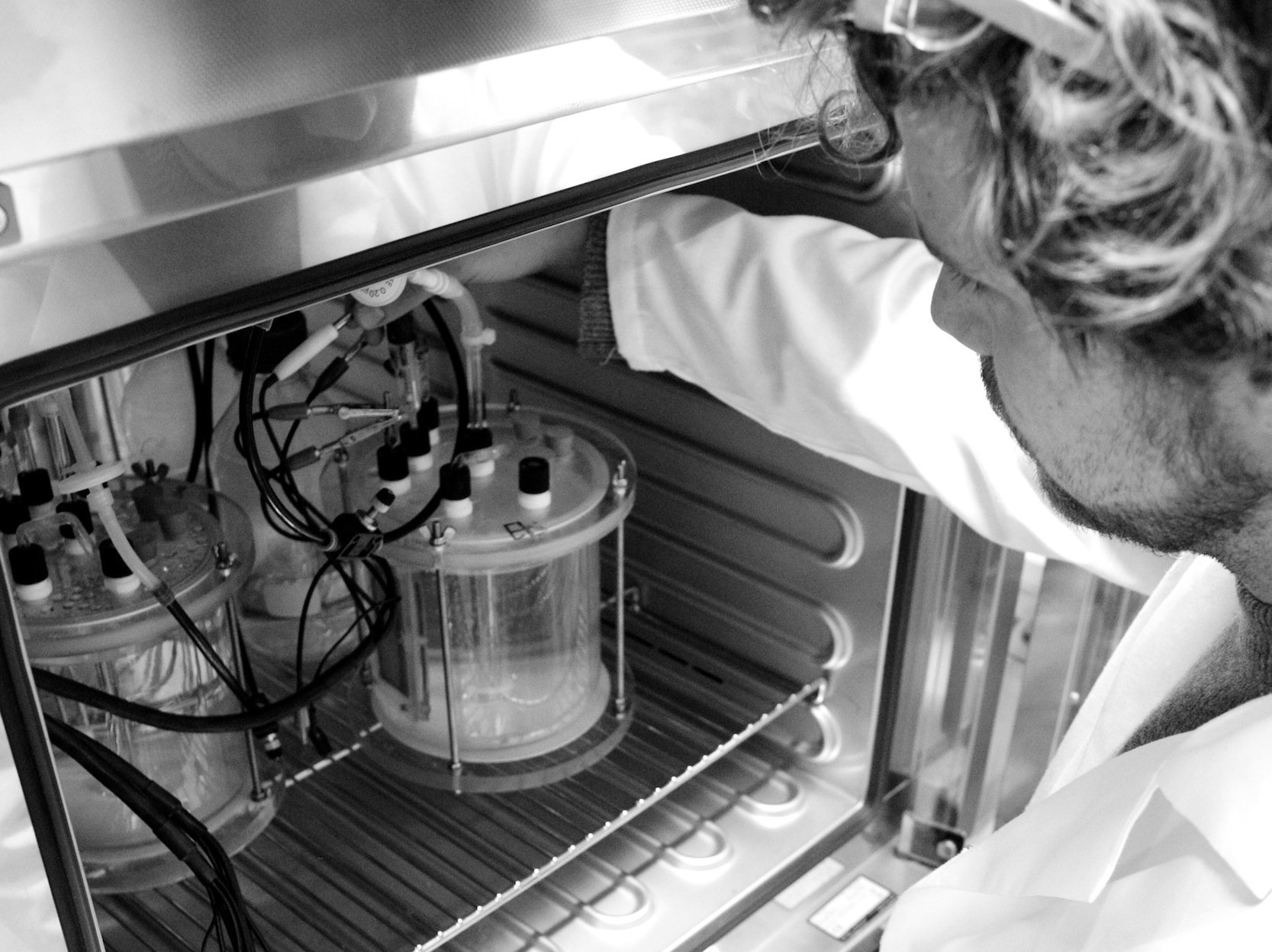
Der Biologe Johannes Eberhard Reiner vom KIT mit den Reaktoren zur mikrobiellen Elektrosynthese: Die Mikroorganismen in den Reaktoren produzieren aus Rauchgas, Luft und Strom das Biopolymer Polyhydroxybuttersäure.
Quelle: Constanze Zacharias/KIT
Das ist beim menschlichen Atmungsprozess ganz ähnlich, bei dem der Sauerstoff ebenfalls als Empfänger von Elektronen dient. „Bei uns Menschen kommen die Elektronen natürlich nicht von einer Kathode, sondern werden durch die Verstoffwechselung der aufgenommenen Nahrung in den Zellen freigesetzt und dort dann zur Energiegewinnung auf Sauerstoff übertragen“, beschreibt Eberhard Reiner.
Verfahren ersetzt Öl als Rohstoff für Kunststoffe
Aus den in diesem Prozess entstehenden Polymeren lassen sich zum Beispiel Einwegbecher, Verpackungen oder kompostierbare Abfallbeutel herstellen. Alles Produkte, die heute noch aus dem Rohstoff Erdöl stammen.
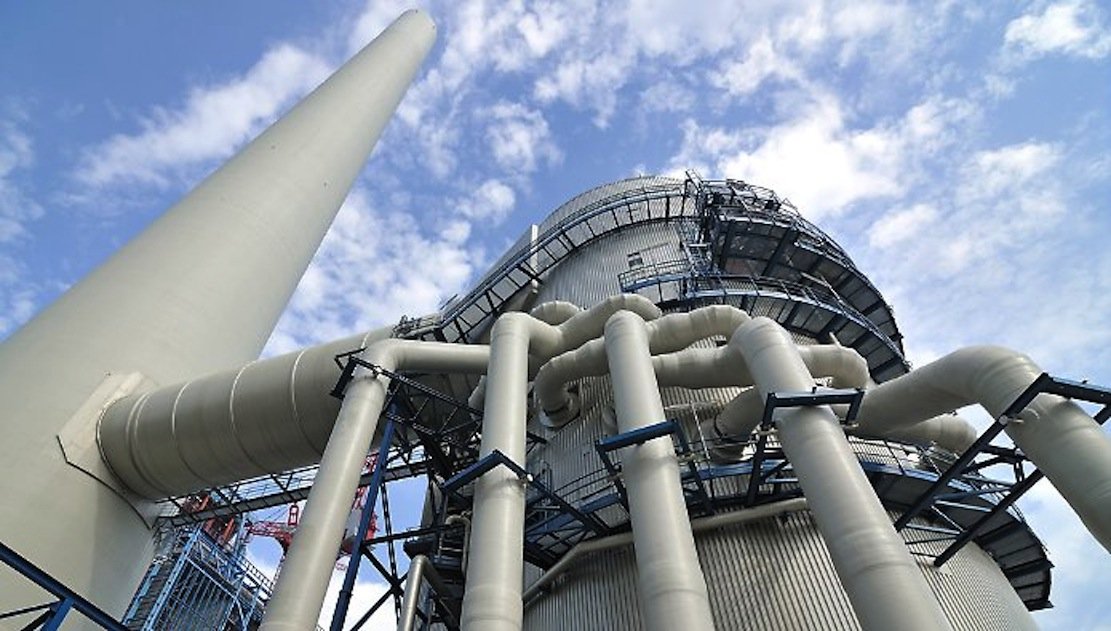
Rauchgasentschwefelungsanlage des EnBW-Steinkohlekraftwerks im Rheinhafen Karlsruhe: In dem Kraftwerk wird die neue Technik erprobt, mithilfe von Mikroben Biokunststoff aus dem im Rauchgas enthaltenen Kohlenstoff zu produzieren.
Quelle: EnBW
Damit der Weg in einen Kohlenstoffkreislauf ein nachhaltiger Weg ist, beziehen die Wissenschaftler die für den Prozess erforderliche elektrische Energie aus regenerativen Quellen. Das benötigte Kohlendioxid als Mikrobenfutter stammt aus dem Rauchgas von Kraftwerken, die mit fossilen Energieträgern arbeiten.
Test mit Abgase aus dem Kohlekraftwerk Karlsruhe
„BioElectroPlast“ heißt das im September 2016 gestartete Forschungsvorhaben des KIT, welches vom Bundesforschungsministerium drei Jahre lang gefördert wird. Neben vielen weiteren Partnern beteiligt sich auch der Energieversorger EnBW. Dem Energiekonzern geht es darum, Möglichkeiten zu finden, den Ausstoß von Kohlendioxid bei der Brückentechnologie Kohleverbrennung weiter zu reduzieren. Praktisch für die KIT-Forscher: Sie können ihre Bioreaktoren direkt im Kohlekraftwerk der EnBW am Rheinhafen Karlsruhe testen und die Abgase des Kraftwerks nutzen.
Schon seit längerem arbeitet auch eine Forschungsallianz mit 21 Partnern, der unter anderem die Technischen Universitäten in Dortmund, Aachen, Karlsruhe und Darmstadt sowie Großunternehmen wie RWE angehören, an der Technik, Mikroorganismen zur Kohlendioxid-Verwertung zu bewegen. Genutzt werden dabei die Rauchgase aus den Braunkohlekraftwerken am Niederrhein.
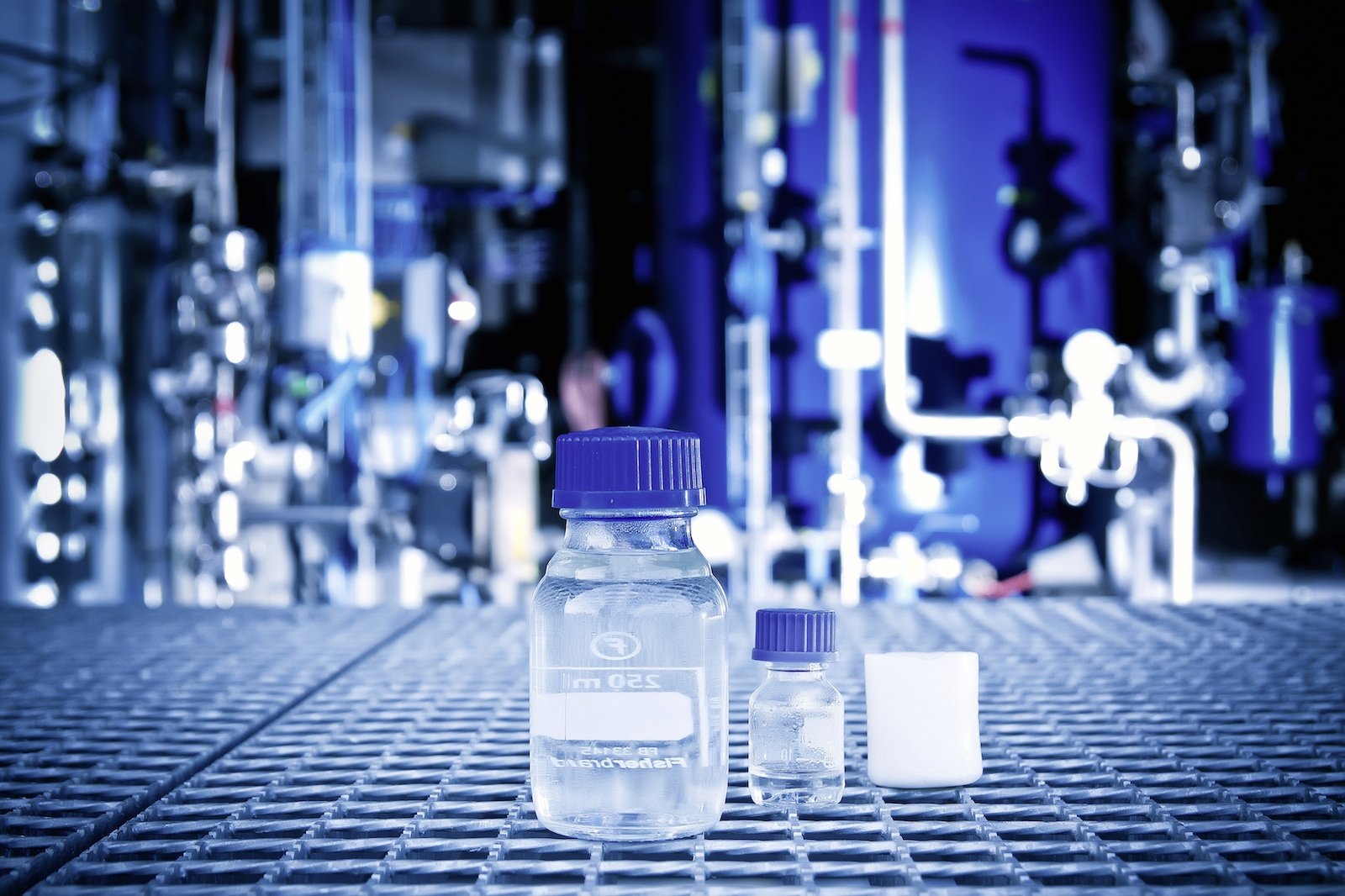
Wasser, CO2 und Ökostrom sind die Grundlagen für Audi e-diesel.
Quelle: Audi
Auch der Autohersteller Audi experimentiert mit CO2 als Rohstoff. Zusammen mit dem Dresdner Energietechnikunternehmen Sunfire hat der Autohersteller ein Verfahren entwickelt, in dem ein synthetischer Diesel auf CO2-Basis entsteht.
Schon im industriellen Maßstab nutzt der Leverkusener Bayer-Konzern CO2 als Rohstoff. Im Werk in Dormagen ist im Sommer eine Anlage in Betrieb gegangen, die aus Kohlendioxid den Schaumstoff für Matratzen herstellt. Sie ist in Deutschland die erste Anlage ihrer Art und soll einen Durchsatz von 5000 t pro Jahr erreichen. An der Entwicklung war auch die RWTH Aachen beteiligt.
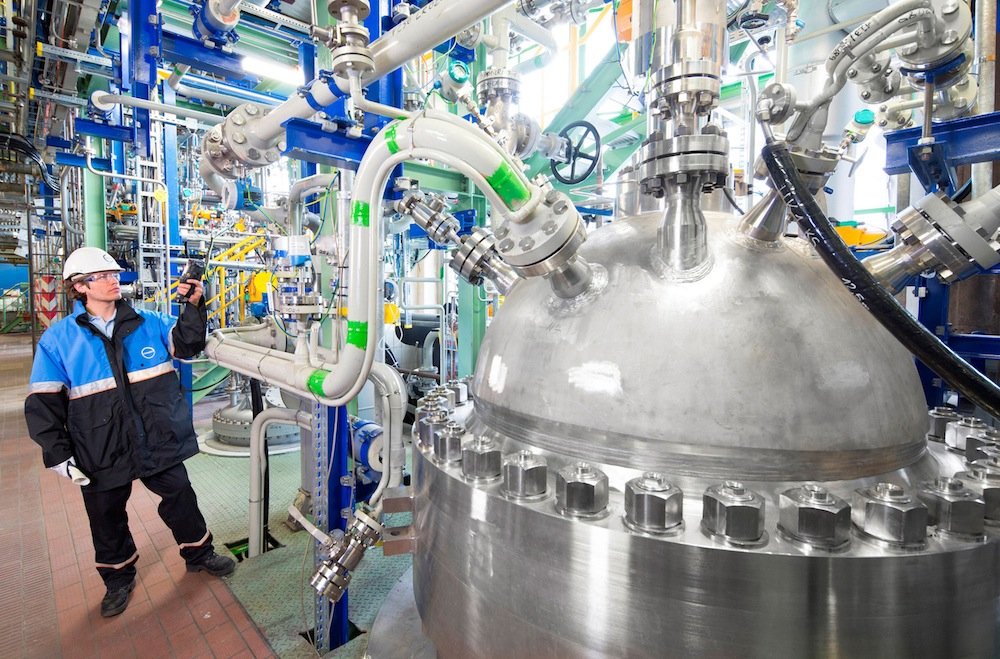
Covestro ist es gelungen, mit CO2 Kunststoff zu produzieren. Das reduziert die Abhängigkeit von Erdöl. Erste Matratzen und Polstermöbel kommen dieses Jahr auf den Markt.
Quelle: Covestro
Ein Beitrag von: