Siemens entwickelt neues Recyclingverfahren für Carbonfasern
Kohlenfaserverstärkte Kunststoffe lassen sich mit einem neuen Verfahren recyceln, das Siemens-Ingenieure entwickelt haben. Der letzte Schliff fehlt aber noch.
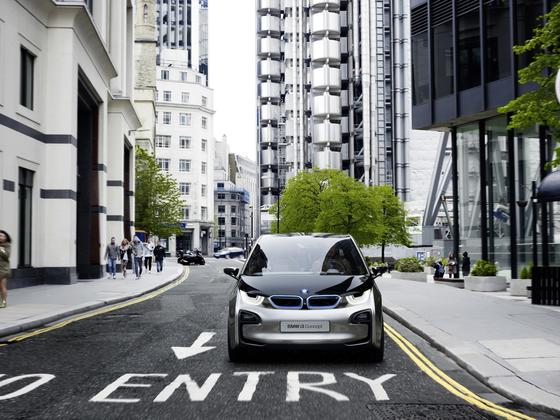
Das Elektroauto i3 von BMW hat eine Karosserie aus Carbon, um Gewicht zu sparen und damit die Reichweite zu vergrößern. Siemens hat jetzt ein neues Recyclingverfahren für Kohlefasern entwickelt, mit dem sich künftig neue Bauteile fertigen lassen.
Foto: BMW
Edle Fahrräder haben ihren Preis – und einen Rahmen aus extrem leichtem kohlenfaserverstärkten Kunststoff. Nach einem Sturz kann dieser allerdings innere Verletzungen davontragen, die von außen nicht sichtbar sind. Die Folge: „Wenn du es am wenigsten erwartest, bricht dir die Gabel und du landest bei 50 Kilometer pro Stunde auf der Fresse.“ So jedenfalls formuliert es ein Anonymus auf einer Radlerplattform im Internet.
Mancher Rahmen landet derzeit nach einem gewöhnlichen Werkstattbesuch im Müll. Denn das Einspannen des CFK-Rahmen in eine Werkstatthalterung braucht ganz viel Gefühl. Einmal die Halterung zu stark angezogen, ist das Rahmenrohr schon beschädigt. Unreparierbar.
Erstmals ein Verfahren zum CFK-Recycling entwickelt
Wenigstens kann man den Rahmen jetzt recyceln. Siemens-Ingenieure um den Recyclingexperten Dr. Heinrich Zeininger haben dazu eine neue Technik entwickelt. Bei diesem solvolytischen Verfahren wird das Harz, das die Kohlenstofffasern umschließt wie Lignin den Zellstoff im Holz bei einer Temperatur von 200 Grad Celsius unter Druck von schlichtem Wasser abgebaut. Dabei entsteht ein Alkoholgemisch. Außerdem bleiben die Fasern zurück, behalten allerdings ihre ursprüngliche Länge und Form, die sie bei der Produktion bekommen hatten. Sogar die Beschichtung, die für eine innige Verbindung mit dem Harz gesorgt hat, bleibt erhalten.
Wenn das Fasergerüst nicht beschädigt ist, kann daraus ein neues Bauteil hergestellt werden, allerdings bislang nur in der gleichen Form. Die Fasern eines beschädigten Fahrradrahmens sind natürlich unbrauchbar. Das Recyclingergebnis wäre erst perfekt, wenn es gelänge, die Fasern zurückzugewinnen, um sie zur Herstellung ganz neuer Bauteile nutzen zu können. Das wollen die Siemens-Entwickler jetzt angehen. Erst wenn sie damit Erfolg haben handelt es sich um echtes Recycling.
Recycelte Fasern oft nur wirre Faserknäuel
Bisher werden ausrangierte Bauteile aus kohlenfaserverstärktem Kunststoff (CFK, Carbonfaserverstärkter Kunststoff) per Pyrolyse recycelt. Sie werden unter Luftabschluss erhitzt, sodass der Kunststoff verschwelt. Die so zurückgewonnenen Fasern bilden meist wirre Knäuel, die nur noch in zerkleinerter Form zur Herstellung leitfähiger Kunststoffe genutzt werden können. Das entstehende Gas lässt sich immerhin zur Wärmeerzeugung nutzen.
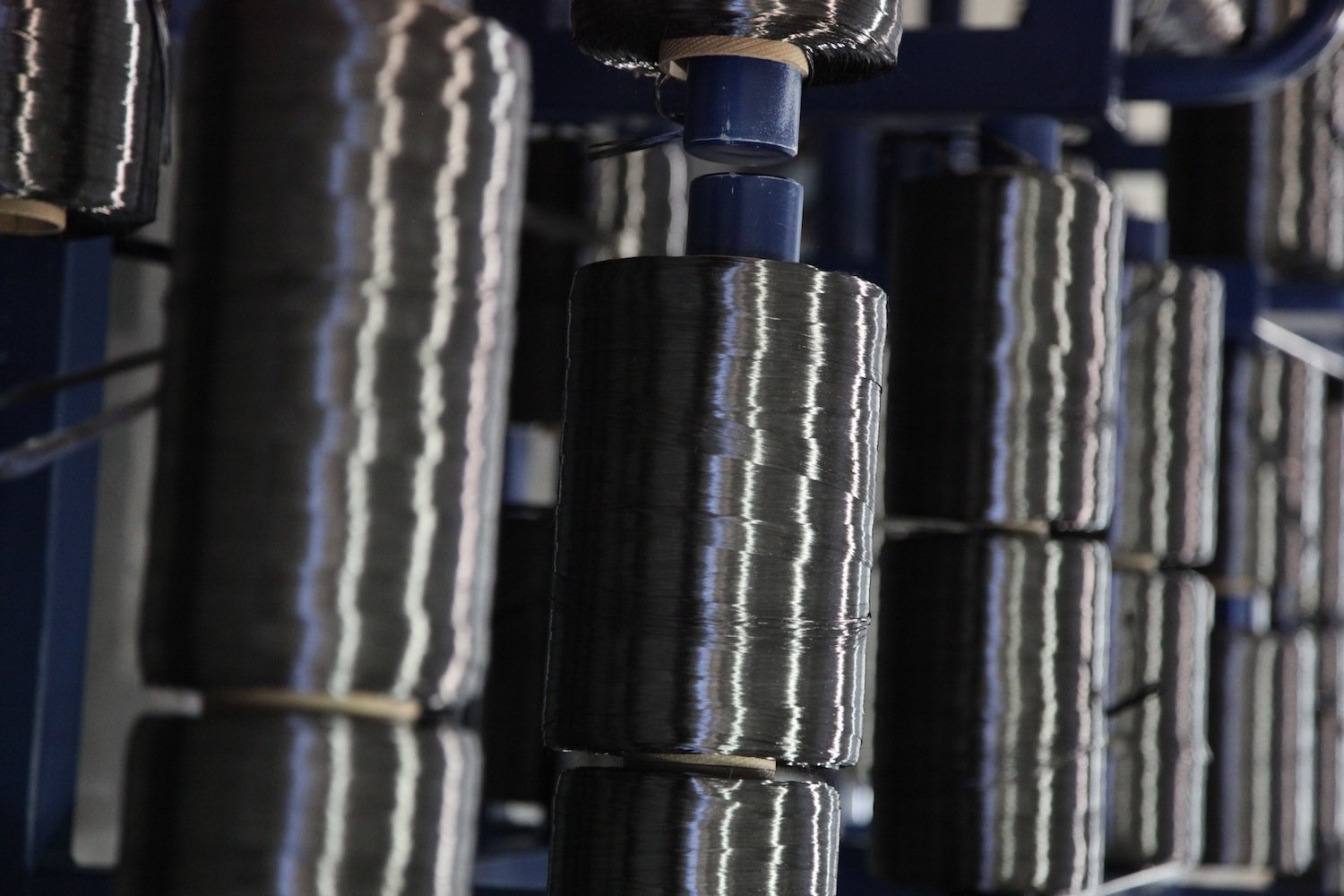
Kohlefasern sind im Leichtbau das Material der Zukunft. Allerdings lassen sich die einmal verbauten Fasern nur schwer recyceln.
Quelle: BMW
CFK-Recycling ist aus zwei Gründen wichtig. Zum einen ist die Herstellung der Fasern sehr energieintensiv, weil dazu eine Temperatur von 2000 Grad Celsius nötig ist. Zum anderen werden immer mehr Bauteile aus diesem Material hergestellt, die irgendwann ausgedient haben. Es begann mit Flugzeugen, die heute bereits zu großen Teilen aus CFK gefertigt werden. In den letzten Jahren wurden immer mehr CFK-Bauteile in Autos eingebaut, um Gewicht und damit Treibstoff zu sparen. Und jetzt kommt mit dem i3 von BMW auch das erste Elektroauto mit CFK-Karosserie auf den Markt. Das wird nur der Anfang sein.
BMW i3 mit Karosserie aus Carbon
Das neue Verfahren ist für Siemens von besonderer Bedeutung, weil der Markt für CFK boomt. „Carbonfaserverstärkte Materialien werden wegen ihrer besonderen Eigenschaften künftig auch von Siemens immer häufiger eingesetzt, etwa in Motoren oder Rotorblättern“, schildert der Siemens-Recyclingexperte Dr. Heinrich Zeininger. „Unser Verfahren ist hier nützlich, da bei der Entwicklung neuer Produkte immer auch ein Recyclingkonzept erforderlich ist. Die nächste Herausforderung wird sein, die wiedergewonnenen Carbonfasern in neue Produkte zu integrieren, auch wenn die Geometrie des neuen Bauteils von der des Ursprungsteils abweicht.“
Ein Beitrag von: