Autoproduktion nach dem Baukasten-Prinzip
Nach Gleichteileprinzip und Plattformkonzepten kündigt sich nun eine neues Konzept zur modell- und markenübergreifenden Vereinheitlichung in der Automobilproduktion an. Der Volkswagen-Konzern hat jetzt eine Modulstrategie für Motoren und Karosseriebauteile entwickelt, die weltweit Maßstäbe setzen soll.
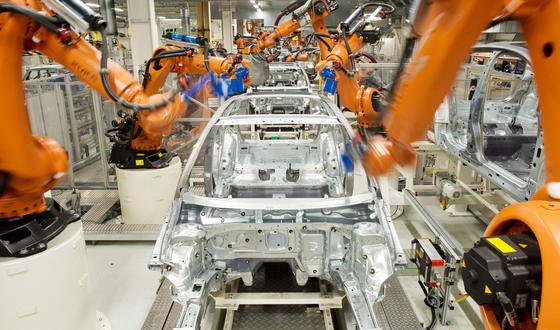
Der Volkswagen-Konzern hat eine Modulstrategie für Motoren und Karosseriebauteile entwickelt, die Maßstäbe setzt.
Foto: dpa
Eine möglichst große Zahl gleicher Teile für verschiedene Modelle und teilweise auch Marken zu verwenden, ist schon länger Ziel der Automobilindustrie. Mit dem nun von Volkswagen vorgestellten Modulbaukasten wird die bisherige Gleichteile- und Plattformstrategie noch erweitert. Damit will der Wolfsburger Konzern bei der Automobilproduktion hinsichtlich Flexibilität und Reduzierung der Bauteilvielfalt neue Maßstäbe setzen. Das gilt sowohl für Motoren- als auch Karosserievarianten. Zugutekommen sollen die Änderungen den mehr als 90 Fertigungsstätten von VW in aller Welt, die in dieses System eingebunden sind.
Karosserieseitig löst sich das Baukastensystem dabei von der starren Plattform und erlaubt es, sowohl Radstand und Spurweiten zu verändern. Einheitlich ist nun nur noch der Abstand von Vorderradmitte bis etwa zur A-Säule. Damit sind auch Breite und Länge der Karosserie variabel. Alle Karosseriebauteile wurden unter die Lupe genommen und wenn immer möglich vereinheitlicht. Als Beispiel dient der Halter der Armaturentafel, der bisher für jedes Modell anders ausfiel. Mit der Einführung des Modulbaukastens gibt es quer über alle Modelle nur noch eine Ausführung, die nun in sehr hohen Stückzahlen hergestellt werden kann.
Baukasten-Prinzip: Großflächige Bauteile aus einem Stück
Um die Fahrzeuggewichte trotz noch höherer Anforderungen an die Crashsicherheit abzusenken, zogen Konstrukteure und Werkstoffspezialisten alle Register. So werden sicherheitsrelevante Teile wie etwa die B-Säule aus hochfestem, dünnwandigem, warm umgeformtem Stahl hergestellt, während für andere nun Blechbahnen mit drei unterschiedlichen Dicken verarbeitet werden können. Sie erlauben es, großflächige Bauteile aus einem Stück zu pressen, die früher durch angeschweißte verstärkt werden mussten. Viele dieser Maßnahmen wurden bisher bereits bei Oberklasseautomobilen verwendet und haben sich dort bewährt.
Motorseitig schuf VW für alle Wagen mit vier oder weniger Zylindern den modularen Querbaukasten (MQB), während für Audi und die Oberklassemodelle mit Motoren über vier Zylinder der modulare Längsbaukasten (MLB) entwickelt wurde. Alle Motoren werden nun so ausgelegt, dass sie im Wagen um 12 Grad nach hinten geneigt eingebaut werden, wobei die „kalte“ Seite nach vorn, die „warme“ nach hinten weist. Alle aufgeladenen Motoren erhalten wassergekühlte Ladeluftkühler direkt am Zylinderkopf innerhalb eines Ansaugmoduls, während die Diesel den erheblich vergrößerten Oxidationskatalysator direkt hinter der Turbine tragen und den Partikelfilter unmittelbar darunter. Bei allen neuen Motoren wird das Temperaturmanagement wesentlich verbessert, um die Warmlaufzeit zu verkürzen. Wichtiger Nebeneffekt ist die schnellere Aufheizung des Kfz-Innenraums nach dem Kaltstart.
Autoproduktion nach dem Baukasten-Prinzip macht Radstand und Spurweiten veränderbar
Erste Auswirkungen der Einbaulage sind ein verlängerter Radstand und ein verkürzter vorderer Überhang bei zugleich verbesserter Gewichtsverteilung. Erster Nutznießer ist das neue Cross Coupé von VW auf der Basis des Tiguan. Das Auto wurde im März erstmals in Europa auf dem Genfer Automobilsalon ausgestellt. Als Hauptvorteil aber ist anzusehen, dass die Motoren für alle Marken in der jeweils gleichen Ausstattung einbaufertig geliefert werden, wobei die Zahl der Anschlüsse reduziert werden konnte und die Zahl der gleichen Bauteile erheblich anstieg. Das ergibt größere Losgrößen, geringere Stückkosten, aber auch Vorteile bei Wartung und Reparatur. Durch die Verlegung der „warmen“ Seite nach hinten wird der Anschluss an das Abgassystem erheblich vereinfacht.
Gegenwärtig stehen zwei neu konstruierte Motoren zur Einführung bereit, der 1,4 l TSI (Benziner) und der 2 l TDI (Diesel). Besonders interessant ist der 1,4 TSI mit Zylinderabschaltung, intern der Motorenreihe EA211 zugehörig, bei dem die beiden inneren Zylinder abgeschaltet werden, wenn vom Fahrer nur wenig Leistung gefordert wird. Damit wurde erstmalig die Zylinderabschaltung bei einem kleinen Vierzylinder zur Serienreife entwickelt. Da die beiden äußeren Zylinder um 360 Grad versetzt gezündet werden, läuft der Motor so rund wie mit vier Zylindern.
Hatte der Vorgänger gleichen Hubraums einen Zylinderblock aus Grauguss, so besitzt der aktuelle Motor einen solchen aus Aluminiumdruckguss. Der Antrieb der beiden Nockenwellen erfolgt nun mit einem Zahnriemen, nicht mehr durch eine Kette. Alle Bauteile wurden gewichtsoptimiert, sodass der Motor 22 kg leichter ist als der Vorgänger – und etwas kürzer ist er auch.
Die beiden Diesel mit 1,6 l und 2,0 l Hubraum sind bis auf den Hub identisch, zuerst wird jedoch der 2,0 l im Audi A 3 eingeführt. Danach erhält ihn der VW Golf im Frühherbst, anschließend der Skoda Oktavia – und schließlich rund 40 weitere Modelle. Neu ist auch bei beiden Dieseln der Wasser-Ladeluftkühler direkt vor den Einlassventilen, die Einführung der Niederdruck-Abgasrückführung sowie die Voraussetzungen für die Nockenwellenverstellung. Sie wird voraussichtlich erst für die Abgasnorm Euro 6 benötigt.
Die Gesamtgewichte der neuen Wagen sinken nach VW-Angaben durch leichtere Motoren und verbesserte Karosseriebauteile im Mittel um 50 kg. Daraus wird ersichtlich, dass auch die Produktion in den Modulbaukasten einbezogen ist und ihren Teil sowohl zur Verbesserung der Fahrzeuge als auch zur Kostensenkung beiträgt. Zugleich wurde eine Art Fabrikbaukasten entwickelt, der überall in der Welt aus den gleichen Gebäuden und der gleichen, erprobten Gebäudeanordnung besteht. Reicht die Fertigungskapazität nicht aus, wird eine zweite Fabrik spiegelbildlich daneben gesetzt.
Ein Beitrag von: