Batterieforschung in Deutschland läuft auf Hochtouren
Manche Beobachter stimmen bereits Abgesänge auf die Elektromobilität an. Dabei nimmt die Entwicklung gerade erst Fahrt auf. Ein Schwerpunkt ist die Produktion großformatiger Lithium-Ionen-Zellen. Forscher ringen um beschleunigte Prozesse. Systematisch analysieren sie Einflüsse von Produktionsparametern auf Qualität, Lebensdauer und Betriebssicherheit der Akkus. Neue Verfahren zur Prozessüberwachung sind gefragt.
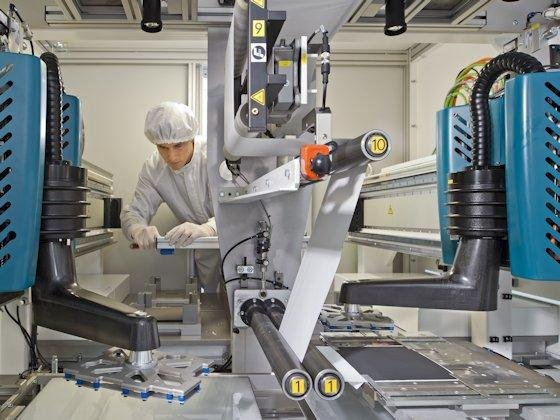
Winzige, für das Auge nicht sichtbare Metallpartikel können in Lithium-Ionen-Akkus zum Kurzschluss führen. Gelangen sie z. B. beim Laserzuschnitt der Elektrodenfolien aufs Aktivmaterial und bleiben unentdeckt, wird der damit gefertigte Hochvolt-Akku kaum die Qualität und Lebensdauer erreichen, die in der Automobilindustrie gefragt ist.
Doch wie lassen sich Partikel auf Materialbahnen aufspüren, die sich aus µm-Partikeln zusammensetzen? „Mit rein optischen Verfahren ist das kaum zu machen“, erklärt Christoph Tammer, der am Augsburger Fraunhofer-Institut für Werkzeugmaschinen und Umformtechnik (IWU) in der Projektgruppe für ressourceneffiziente mechatronische Verarbeitungsmaschinen (RMV) neue Verfahren zur Qualitätssicherung in der Produktion großer Lithium-Ionen-Zellen erforscht.
Wie Tammer arbeiten hierzulande inzwischen Dutzende Forscher an der Optimierung der Fertigungstechnik für Hochvolt-Batterien. Denn mit den Kosten und der Qualität dieser Schlüsselkomponente steht und fällt der Markterfolg der Elektromobilität. Auf Batterien wird sich künftig ein Gutteil der Wertschöpfung im Fahrzeugbau verschieben.
Deutschland von Führungsrolle noch entfernt
Doch der selbsternannte „Leitanbieter“ Deutschland nimmt bei seiner Produktion beileibe noch keine Führungsrolle ein. „Unsere Chancen liegen auf dem Gebiet der Qualität“, sagt Tammer. Verfahren müssen her, die bei hochfrequenter automatisierter Fertigung verlässliche Qualität gewährleisten. Um etwa die winzigen Partikel aufzuspüren, experimentieren die Forscher mit aktiver Thermografie. Sie regen die Elektroden mit Wärme an künftig könnte das per Linienlaser geschehen.
Während die Wärme im leitenden Aktivmaterialverbund schnell abgeführt wird, sammelt sie sich in aufliegenden Partikeln und lässt diese im Wärmebild leuchten. Noch funktioniert das laut Tammer erst im Labormaßstab. Doch schon bald will sein Team das Verfahren zusammen mit Kollegen des Stuttgarter Thermografiespezialisten Edevis und Forschern des Instituts für Werkzeugmaschinen und Betriebswissenschaften (iwb) der TU München in deren Garchinger Batterieproduktions-Technikum erproben.
Parallel lotet Tammers Forschungsgruppe im Labor aus, wie weit sich die thermografische Partikeldiagnostik treiben lässt. Denkbar wäre es, vom Abkühlverhalten darauf zu schließen, ob es sich um Metall, Staub oder abgebröckeltes Aktivmaterial handelt. Das würde helfen, die Fehlerquelle einzugrenzen und abzustellen. Sei es eine fehlerhafte Mischung des Aktivmaterial-Slurrys, der aus Metallfolien Elektroden macht, sei es Staub-Eintrag durch unachtsame Mitarbeiter oder seien es Metallspritzer vom Laserzuschnitt der Elektroden.
„Es ist nicht gesagt, dass solche Diagnoseverfahren in Fertigungslinien integriert werden“, sagt der Fraunhofer-Forscher. Denkbar sei, sie nur vorab zur Optimierung der Prozessparameter einzusetzen. Weil Partikel auf den Elektroden bisher kaum aufspürbar sind, ist unklar, wie der Schneideprozess der Anoden- und Kathodenfolien optimal zu führen ist. Noch wird auf gerade glatte Kanten und zügige Takte hin optimiert. Die Partikelproblematik ist außen vor, obwohl sie fatale Folgen für die Lebensdauer und Sicherheit der Batterien haben kann.
Einerseits wollen die Forscher die Produktionsprozesse in Abhängigkeit der eingesetzten Zellchemie besser verstehen und dafür mit immer feineren Mess- und Kontrollverfahren durchleuchten. Andererseits bemühen sich die Forscher um Klärung, wo Inline-Messungen in den Fertigungslinien Sinn machen werden, und wo sie entbehrlich sind. Denn neben der Qualität gilt es die Kosten zu optimieren.
Ein wichtiger Kostenfaktor ist der Durchsatz der Elektroden-Beschichtungsanlagen. Am Karlsruher Institut für Technologie (KIT) ist es einem Forscherteam gelungen, diesen auf 100 m/min zu verdoppeln und dabei die hohen Anforderungen an die Homogenität des Aktivmaterial-Slurrys und die Präzision der Schichtdicken zu wahren.
Batteriekosten sollen auf 250 € pro Kilowattstunde sinken
„Aktuell arbeiten wir daran, die anschließende Trocknung an die Geschwindigkeit anzupassen“, so KIT-Forscher Olaf Wollersheim. Dafür baut das KIT mit Förderung des Bundeswirtschaftsministeriums eine Forschungsfabrik zur Kleinserienfertigung von Lithium-Zellen auf. Das Ziel ist klar definiert: Bis 2018 sollen Batteriesysteme mit einer Energiedichte von 250 Wh/kg zu Kosten von 250 €/kWh produziert werden. Die KIT-Forscher wollen ihren Teil dazu beitragen.
Um die hohen Prozessgeschwindigkeiten realisieren zu können, müssen Hunderte Parameter stimmen. „Wir erforschen dafür unter anderem systematisch, mit welchen Verfahren sich die Qualität des Slurrys bestimmen lässt“, erläutert Wollersheim. Es gilt, die Gemische der unterschiedlichen Zellchemien komplett zu charakterisieren und geeignete Messparameter zu finden.
„Noch ist die Slurry-Analytik unterentwickelt“, sagt er es sei wie der Blick in die berühmte Blackbox. Ziel der Forschung ist es auch hier, wichtige von unwichtigen Parametern unterscheiden zu lernen. Intelligente, mit Datenbanken hinterlegte Verfahren zur Qualitätssicherung sollen dann den Weg zu voll vernetzten automatisierten Fertigungslinien für Lithium-Ionen-Zellen ebnen.
Noch findet deren Fertigung Schritt für Schritt statt. Nach Beschichten und Trocknen wird zwischengelagert, später gewalzt, zugeschnitten, gestapelt. Fernziel ist ein durchlaufender Prozess vom Anrühren des Slurrys bis zum Befüllen der Zellen mit Elektrolyt, dem Formieren, Altern und finalen Aufladen.
Voraussetzung dafür ist das Wissen, wie und vor allem an welchen Stationen ein solcher fortlaufender Prozess sinnvoll überwacht wird. Die Basis dafür soll in Forschungsfabriken gelegt werden etwa durch gezielte Verunreinigungen der Zellen und Fertigungsfehler, um die Effekte der Defekte kennen und nutzen zu lernen.
Während erste Beobachter schon Abgesänge auf die Elektromobilität anstimmen, mühen sich Forscher in diversen staatlich geförderten Verbundforschungsprojekten, die Blackbox-Batterie systematisch auszuleuchten. Das braucht Zeit. Doch Wollersheim sieht diese Arbeit als Chance für den Batteriestandort Deutschland. „Wir haben den Vorteil, dass Industrie, Hochschulen und Forschungsinstitute Hand in Hand arbeiten“, sagt er. Dieser Draht sei bei vielen internationalen Konkurrenten sehr viel länger.
Ein Beitrag von: