BMW investiert 60 Millionen Euro: Autos umweltfreundlich lackieren
Die BMW Group geht den nächsten Schritt in Richtung nachhaltige Fahrzeugproduktion. Die Umstellung der Lackiererei hat bereits vor Jahren begonnen. Jetzt wird am Standort Dingolfing weiter umgerüstet, um das Langzeitziel zu erreichen: Bis 2030 sollen die Emissionen um 80% sinken, im Vergleich zum Stand von 2019.
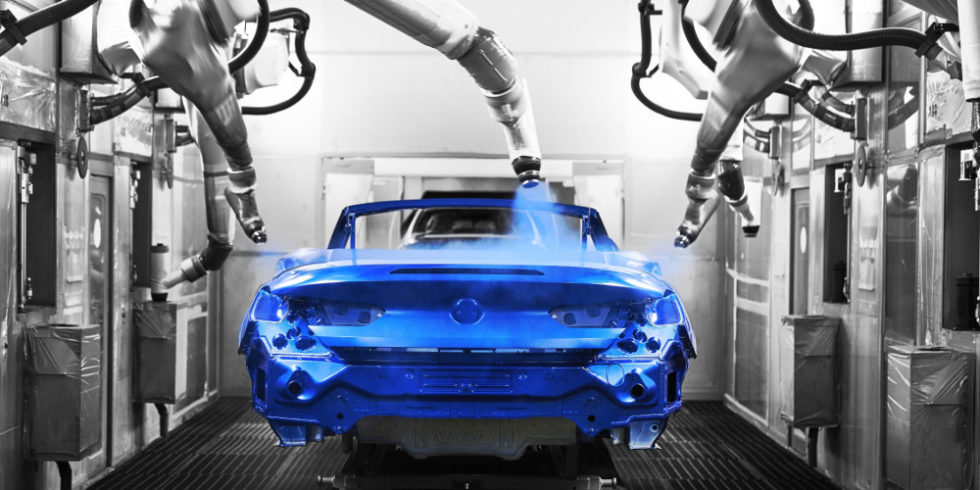
Beim Lackieren der Autos wird etwa ein Drittel der Energie verbraucht, die bei der Fahrzeugproduktion anfällt.
Foto: BMW Group
Die Fahrzeugherstellung ist grundsätzlich eine Branche, die viel Energie benötigt und damit kräftig CO2-Ausstoß produziert. Was nur wenige wissen: Etwa ein Drittel des Energieverbrauchs fällt beim Lackieren an. Deswegen ist das Einsparpotenzial hier auch besonders groß.
In der Lackiererei im BMW-Werk in Dingolfing werden an jedem Arbeitstag etwa 1.600 Fahrzeuge mit Farbe versehen. Nach Angaben des Unternehmens zählt sie bereits zu den innovativsten Anlagen der Branche. Denn das Umrüsten hat hier bereits vor einigen Jahren begonnen. Vor allem die Umstellung auf das Lackierverfahren IPP (Integrated Paint Process) hat einiges dazu beigetragen, den Energieverbrauch zu senken – beim IPP entfällt das Auftragen und Einbrennen der sogenannten Füllerschicht. Sie wird dafür in eine von zwei neu entwickelten Basislackschichten verlagert. Weitere Maßnahmen kamen hinzu, sodass der Energieverbrauch zwischen 2006 und 2020 bereits um etwa 10% abgenommen hat. Die benötigte Wassermenge konnte BMW um ungefähr 25% reduzieren und das Lösemittel um 60%. Mit einer Investitionssumme von 60 Millionen Euro sollen jetzt die nächsten Umrüstungen erfolgen. Das sind die wichtigsten Maßnahmen.
Klimaziele: Es reicht nicht, neue Verbrenner zu verbieten
BMW spart einen Schritt beim Prozess des Lackierens komplett ein
An erster Stelle ist dabei die Umstellung der Lackiererei von einem System der Nassauswaschung auf ein System zur Trockenabscheidung von Lackpartikeln zu nennen. Im Fokus steht das sogenannte Lack-Overspray. Damit ist der Lack gemeint, der beim Versprühen nicht auf dem Fahrzeug landet und bisher mit Wasser aufgefangen wurde. Jetzt passiert das mit Kalksteinmehl. Damit verringert BMW nicht nur den Wasser-, sondern auch den Energieverbrauch, weil im Vergleich zu vorher nur noch 20% der Luft temperiert und befeuchtet werden müssen. Zudem kann das benutzte Steinmehl zum Beispiel von der Zementindustrie weiterverwertet werden. Eine Aufbereitung wie beim Abwasser findet nicht statt.
Voraussichtlich bis zum Jahreswechsel 2022/2023 sollen alle Produktionslinien in Dingolfing entsprechend ausgerüstet sein. „Durch diese Umstellung werden wir voraussichtlich über sechs Millionen Liter Wasser und circa 13.000 Megawattstunden Heizenergie pro Jahr einsparen“, sagt Stefan Dorsch, der die Planung der neuen Anlagen verantwortet. Das Unternehmen rechnet mit CO2-Einsparungen von mehr als 4.000 Tonnen pro Jahr
Neue BMW-Lacke werden entwickelt und noch präziser aufgetragen
Parallel will BMW dafür sorgen, dass von vornherein weniger Overspray entsteht. Dafür wird eine neue Lackiertechnologie getestet, bei der die Strahlen den Lack sehr präzise auftragen. Sie hat sich bereits bei individuellen Lackierungen von BMW M4 Coupés bewährt. Noch im laufenden Jahr soll sie in Serie gehen.
Wie sieht es mit den Lacken selbst aus? Auch hier gibt es Verbesserungspotenzial. Bei der Herstellung der Mattlacke werden beispielsweise erdölbasierte Vorprodukte durch nachwachsende Rohstoffe ersetzt, die aus organischen Abfällen gewonnen werden.
Aus Wärme wird bei BMW nun auch Strom
Im Bereich der Wärmerückgewinnung steht ebenfalls ein Pilotprojekt in den Startlöchern. In der Lackiererei wird sie bereits aufgefangen und weiterverwendet, wenn sie über 180 Grad Celsius heiß ist. Bei niedrigeren Temperaturen war das bislang wirtschaftlich nicht möglich. Auch das soll sich jetzt ändern. Dazu werden zunächst in verschiedenen Bereichen Module installiert, die die Wärme in einem ORC-Prozess (Organic Rankine Circle) über spezielle Turbinen in Strom umwandeln.
BMW geht davon aus, dass auf diese Weise jährlich 1.200 Megawattstunden Strom aus Abwärme ins Werkstromnetz eingespeist werden können, was den CO2-Fußabdruck weiter senkt. „Wir rechnen mit einer Einsparung von bis zu 1.000 Tonnen CO2 im Jahr“, sagt Dorsch. Verläuft der Test erfolgreich, sollen weitere Module folgen.
300 Kilometer Plastikfolie sollen ersetzt werden
Der nächste Blick richtet sich auf die Anlagen selbst, genauer auf die Polyethylenfolie, die ausgelegt wird, um die Anlagen vor Produktionsrückständen wie Lack, Wachs und PVC zu schützen. Das ist keineswegs ein kleiner Posten. Denn jedes Jahr werden etwa 300 Kilometer dieser Folie verlegt. Gemeinsam mit einem Dienstleister sucht das Unternehmen daher nach einem Ersatz. Wahrscheinlich wird es entweder auf eine zu hundertprozentige Recyclingfolie hinauslaufen oder auf eine Folie, die aus biologisch abbaubaren Rohstoffen besteht, etwa Kartoffelstärke.
Mehr lesen über Innovationen in der Automobilproduktion:
Ein Beitrag von: