Deutsche Bahn testet Schienen mit weltweit einmaligem Großgerät
Die Deutsche Bahn setzt neuerdings auf ein 1,2 Millionen teures Großgerät der Universität Hannover, um Schienen besser auf Langzeitbelastbarkeit testen zu können. Es regt sie mit Unwuchtmotoren zur Eigenschwingung an. Im Vergleich zu hydraulischen Anlagen werden somit schnellere und stromsparendere Tests möglich.
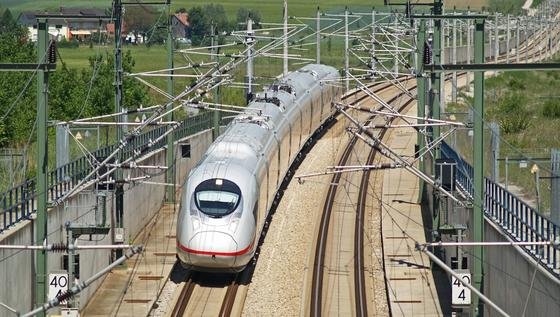
Um Schienen auf ihre Langzeitbelastbarkeit zu testen, setzt die Bahn erstmals auf ein weltweit einmaliges Großgerät der Universität Hannover.
Foto: Deutsche Bahn/Claus Weber
Schienen müssen unglaublichen Kräften standhalten, wenn täglich tausende Züge mit Geschwindigkeiten von bis zu 250 km/h über sie donnern. Damit es im Laufe der Jahre nicht zu Katastrophen kommt, muss die Deutsche Bahn genau wissen, wie lange eine Schiene beansprucht werden kann.
Um Schienen auf ihre Langzeitbelastbarkeit zu testen, setzt die Bahn erstmals auf ein weltweit einmaliges Großgerät der Universität Hannover. Es basiert auf einem riesigen Stahlbetonfundament, das 15 Meter breit und 20 Meter lang ist. In einer eigens gebauten Halle ist es drei Meter tief in den Boden eingelassen. „Mit diesem Gerät können wir erstmalig auch sehr große Konstruktionen mit großen Kräften und Verformungen im Bereich sehr hoher Lastwechselzahlen testen“, erklärt Prof. Steffen Marx vom Institut für Massivbau an der Leibniz Universität Hannover.
Unwuchtmotoren regen Schienen zur Eigenschwingung an
Im sogenannten Federkeller sind 100 Kilogramm schwere Zugfedern installiert. Sie bringen eine Mittellast auf die Schiene, indem sie diese leicht nach unten ziehen. „Auf den Schienen selbst sitzen mehrere Elektromotoren, die sie mit Unwucht zur Eigenschwingung anregen“, erklärt Sebastian Schneider, wissenschaftlicher Mitarbeiter am Institut für Massivbau, im Gespräch mit Ingenieur.de. Ohne Ballast läge die Eigenfrequenz der zwei Meter langen Schiene bei circa 50 Hertz – also bei 50 Schwingungen pro Sekunde. Die Zugfedern senken sie auf etwa 20 Hertz. „Bei dieser Frequenz können die Unwuchtmotoren zuverlässig arbeiten und sind immer noch um ein Vielfaches schneller als Hydraulikzylinder.“
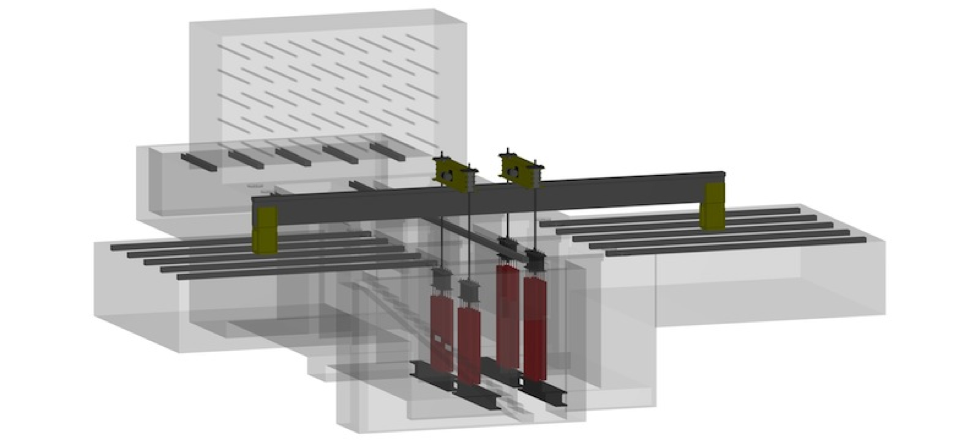
Prüfgerät der Bahn: Die Zugfedern bringen eine Mittellast auf die Schiene. Die Elektromotoren regen sie anschließend zur Eigenschwingung bei circa 20 Hertz an.
Quelle: Leipzig Universität Hannover/Institut für Massivbau)
Das Prinzip für die neue Anlage hat Prof. Marx aus dem Maschinenbau übernommen. Hier arbeiten Ingenieure schon lange mit ähnlichen Anlagen. Sogenannte Resonanzprüfmaschinen sind mit einer Fläche von ein bis zwei Quadratmetern allerdings deutlich kleiner.
Hydraulische Tests sind langsamer und energieintensiver
Um große Bauteile auf ihre Langzeitbelastbarkeit zu testen, kommen bislang meist hydraulische Testverfahren zum Einsatz. Hydraulikzylinder be- und entlasten dabei Bauteile im Wechsel. Das bringt aber einige Probleme mit sich. Meistens lassen sich nur Komponenten testen, die im Maßstab deutlich verkleinert sind. Die Ergebnisse müssen die Tester dann im nächsten Schritt auf das Originalbauteil hochrechnen. Einhundertprozentig genau ist diese Umrechnung nie. Zudem arbeiten die Zylinder verhältnismäßig langsam. Sie sind oft tagelang beschäftigt, um beispielsweise fünf Millionen sogenannte Lastwechsel durchzuführen.
Die neue Großanlage der Wissenschaftler aus Hannover soll nicht nur schneller, sondern auch deutlich energieeffizienter arbeiten als Hydraulikanlagen. Ein hydraulisches Prüfgerät in vergleichbarer Größe würde für die Untersuchung eines kleinen Probekörpers mit zehn Millionen Lastwechseln schnell 10.000 Euro verschlingen. In der neuen Anlage betragen die Energiekosten laut Forscher lediglich 100 Euro.
Die Feuertaufe für das 1,2 Millionen teure Großgerät steht kurz bevor. Im Auftrag der Deutschen Bahn sollen die Forscher 120 Eisenbahnschienen untersuchen, die auf einem Teilabschnitt der neuen Hochleistungstrasse VDE8 von Nürnberg bis Leipzig zum Einsatz kommen sollen. Die neuen Informationen aus den Belastungstests sollen dann auch dem Brückenbau zugutekommen.
Ein Beitrag von: