Die Geschichte hinter Hondas Kultmotor VTEC
Mit der Entwicklung des VTEC-Systems zeigte Honda vor rund 40 Jahren, wie man einen Motor leistungsfähiger und zugleich sparsamer machen kann.
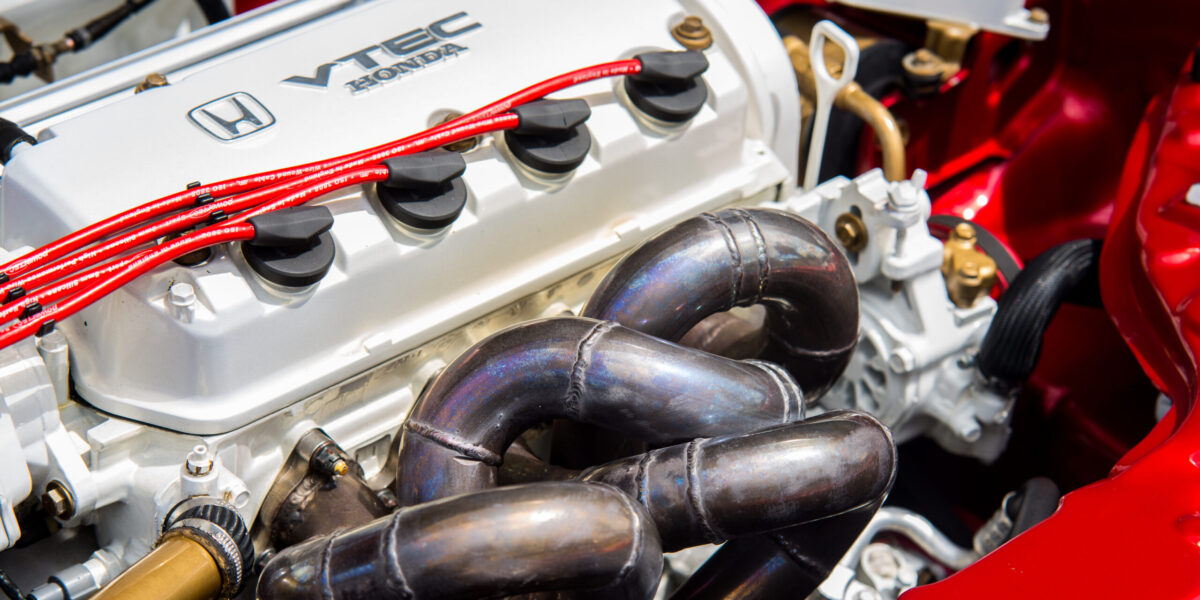
Mit dem VTEC-Motor gelang Honda eine Husarenstück. Der Hersteller konnte zeigen, dass Motoren leistungsfähiger und zugleich sparsamer sein können.
Foto: PantherMedia / Tomasz Trybus
In den 1980er-Jahren setzte sich Honda ein ambitioniertes Ziel: Ein Motor, der bei niedrigen und hohen Drehzahlen gleichermaßen stark performt – ohne Kompromisse beim Verbrauch. Heißt übersetzt: Der Motor sollte leistungsfähiger werden und dabei gleichzeitig weniger Sprit verbrauchen. Was sich nach einer Quadratur des Kreises anhört, führte zum VTEC-System. Es veränderte die Art, wie Motoren denken – oder besser gesagt: wie sie atmen. Wir haben uns die Entwicklung des Motors und seine Besonderheiten genauer angeschaut.
Inhaltsverzeichnis
- Der Anfang einer neuen Idee
- Warum Ventile über Leistung entscheiden
- Von der Idee zur Lösung
- Das ambitionierte Ziel: 100 PS pro Liter
- Technische Herausforderungen
- Die Technik hinter dem VTEC-System
- Vom Prototyp zur Serienproduktion
- Marktstart und Serienerfolg
- Varianten der VTEC-Technologie
- Fahrzeuge mit VTEC-Motoren
- Vergleichbare Systeme anderer Hersteller
Der Anfang einer neuen Idee
Im März 1984 rief Honda das sogenannte NCE-Programm ins Leben. „NCE“ steht für „New Concept Engine“. Ziel war es, eine Motorengeneration zu entwickeln, die kraftvoll, drehfreudig und dennoch sparsam ist. Eine Herausforderung, denn in der Regel steht eine hohe Leistung bei hohen Drehzahlen im Gegensatz zu einem guten Drehmoment im unteren Bereich – insbesondere bei kleinvolumigen Motoren.
Ikuo Kajitani, ein erfahrener Entwickler im Tochigi R&D Center, war überzeugt: Ein variabler Ventilmechanismus musste her. Denn: „Vierventilmotoren gelten als Hochdrehzahlmaschinen. Aber genau deshalb ist es schwer, bei geringem Hubraum ein starkes Drehmoment bei niedrigen Drehzahlen zu erreichen.“
Warum Ventile über Leistung entscheiden
Die Ventilsteuerung spielt beim Motor eine zentrale Rolle. Sie bestimmt, wann wie viel Luft und Kraftstoff in den Brennraum strömt – und wann die Abgase entweichen. Bei herkömmlichen Motoren ist diese Steuerung fix. Doch was bei niedriger Drehzahl optimal ist, limitiert die Leistung obenrum – und umgekehrt.
Kajitani und sein Team standen daher vor einem Dilemma: Wie kombiniert man zwei widersprüchliche Anforderungen in einem einzigen Antriebskonzept?
Die Antwort: Ein Mechanismus, der je nach Drehzahl die Ventilsteuerzeiten und den Hub anpasst. Damit lässt sich der Motor an verschiedene Betriebszustände anpassen – ein Konzept, das später als VTEC (Variable Valve Timing & Lift Electronic Control) bekannt wurde.
Von der Idee zur Lösung
Bereits 1983 – also noch vor dem offiziellen Start des NCE-Programms – begann ein Forschungsteam, sich mit der Möglichkeit einer variablen Ventilsteuerung zu beschäftigen. Die erste Idee war simpel: Zusätzliche Nocken für höhere Drehzahlen und ein Mechanismus, der je nach Last zwischen verschiedenen Profilen wechselt.
Das Prinzip: Bei niedriger Drehzahl wird ein schonendes Nockenprofil genutzt, das Verbrauch und Emissionen optimiert. Steigt die Drehzahl, schaltet der Mechanismus auf ein aggressiveres Profil um, das die Ventile länger und weiter öffnet – mehr Luft, mehr Leistung.
Honda nannte dieses Konzept zunächst „Ventilstopp + variable Ventilsteuerung“. Es wurde zum Herzstück der zukünftigen VTEC-Technologie. Die Grundlagenforschung begann, erste Funktionsmuster wurden getestet und weiterentwickelt.
Das ambitionierte Ziel: 100 PS pro Liter
Als 1986 das D-Projekt zur Umsetzung des VTEC-Motors offiziell gestartet wurde, gab es eine klare Vorgabe: Ein neuer 1,6-Liter-Motor für den kommenden Honda Integra sollte 140 PS leisten. Das entsprach 87,5 PS pro Liter – bereits ein hoher Wert.
Doch das genügte nicht. Hondas Entwicklungschef Nobuhiko Kawamoto stellte eine entscheidende Frage: „Warum erhöhen Sie Ihr Ziel nicht auf 100 PS pro Liter?“ Eine Zahl, die damals für Saugmotoren fast als unerreichbar galt.
Kajitani nahm die Herausforderung an. „Ich verstehe“, sagte er. „Das machen wir zu unserem Ziel.“ Damit waren die Anforderungen klar: 160 PS aus einem 1,6-Liter-Motor, drehfreudig bis 8.000 U/min und gleichzeitig zuverlässig genug für den Alltagseinsatz.
Technische Herausforderungen
Die neue Zielvorgabe stieß bei vielen Teammitgliedern zunächst auf Skepsis. Denn die Erhöhung der Maximaldrehzahl um 20 % bedeutete auch deutlich höhere mechanische Belastungen. Die Trägheitskräfte einzelner Motorteile würden um bis zu 40 % steigen. Um die Belastung zu reduzieren, mussten Komponenten leichter, gleichzeitig aber auch stabiler werden.
Zudem stellte sich die Frage: Wie lässt sich der variable Ventilmechanismus technisch zuverlässig umsetzen? Schließlich sollten bei jeder Umschaltung keine Fehler passieren – bei bis zu 8.000 Umdrehungen pro Minute.
Nach monatelangen Diskussionen, Tests und Rückschlägen kam das Team zu einem Entschluss: Es würde das Ventilsteuersystem komplett neu konzipieren.
Die Technik hinter dem VTEC-System
Kern des Systems ist ein spezieller Kipphebelmechanismus mit hydraulisch betätigtem Sperrbolzen. Dieser verbindet oder trennt je nach Motordrehzahl verschiedene Nockenprofile. Bei niedriger Drehzahl arbeitet der Motor mit einem sparsamen Profil. Ab etwa 5.000 U/min schaltet der Mechanismus auf das leistungsorientierte Profil um.
Zusätzlich setzte das Team auf weitere technische Maßnahmen:
- Größere Einlassventile (von 30 auf 33 mm)
- Optimierte Ventilsteuerzeiten basierend auf Rennmotor-Know-how
- Gewichtsreduktion beweglicher Teile
- Hochfeste Sinterlegierungen für Zahnriemenscheiben
- Neue Gussstähle für die Nockenwelle
- Hitzebeständige Materialien für die Auslassventile
Diese Maßnahmen führten zu einer Reduktion des Trägheitsmoments um 10 % und ermöglichten stabile Leistung bei 8.000 U/min.
Vom Prototyp zur Serienproduktion
Auch nach dem erfolgreichen Funktionstest des ersten Prototyps standen viele Hürden bevor. Schließlich musste sichergestellt werden, dass alle Bauteile – insbesondere der sensible Schaltmechanismus – über die gesamte Lebensdauer zuverlässig funktionierten.
Die Lösung war ein rigoroses Testprogramm. Der sogenannte „bösartige Test“ ging weit über die zu erwartenden Betriebsbedingungen hinaus. Bis zu 400.000 Schaltvorgänge simulierten die Belastung eines Motorlebens. Auch das Zusammenspiel von Hydraulik und Elektronik wurde wiederholt geprüft.
Erst als sämtliche Belastungstests bestanden waren, gab Honda grünes Licht für die Serienproduktion.
Marktstart und Serienerfolg
Im April 1989 war es dann so weit: Der Integra DOHC VTEC kam auf den Markt. Er vereinte 160 PS bei 7.600 U/min mit einem harmonischen Drehmomentverlauf über den gesamten Bereich. Das System ermöglichte nicht nur eine hohe Endleistung, sondern auch ruhigen Leerlauf und gute Fahrbarkeit bei niedrigen Drehzahlen.
Die Kombination aus Alltagstauglichkeit und Sportlichkeit machte den VTEC-Motor schnell beliebt – nicht nur bei Technikfans. In den Folgejahren wurde das System kontinuierlich weiterentwickelt: vom SOHC/VTEC über den VTEC-E bis hin zum dreistufigen VTEC, der ab 1995 für noch feinere Leistungsanpassungen sorgte. Schauen wir uns die verschiedenen Varianten genauer an.
Varianten der VTEC-Technologie
Seit der Einführung von VTEC hat Honda mehrere Varianten entwickelt, um unterschiedlichen Anforderungen gerecht zu werden:
DOHC-VTEC
Das „Double Overhead Camshaft“-VTEC ist die ursprüngliche Form des Systems. Es ermöglicht den Wechsel zwischen zwei Nockenprofilen für Ein- und Auslassventile, um sowohl bei niedrigen als auch bei hohen Drehzahlen optimale Leistung zu erzielen. Dieses System wurde erstmals 1989 im Honda Integra eingeführt.
SOHC-VTEC
Bei der „Single Overhead Camshaft“-Variante steuert eine einzelne Nockenwelle sowohl die Ein- als auch die Auslassventile. Aufgrund von Platzbeschränkungen beeinflusst das VTEC-System hier hauptsächlich die Einlassventile. Diese Variante findet sich häufig in kompakteren und kraftstoffeffizienten Modellen.Reddit
SOHC VTEC-E
Das „VTEC-E“ (Economy) zielt darauf ab, den Kraftstoffverbrauch zu reduzieren und die Effizienz zu steigern. Es ermöglicht einen mageren Kraftstoff-Luft-Mix bei niedrigen Drehzahlen, indem es zunächst nur ein Einlassventil vollständig öffnet und das zweite nur teilweise. Bei höheren Drehzahlen werden beide Ventile vollständig geöffnet, um die Leistung zu erhöhen.
3-Stufen-VTEC
Diese Variante kombiniert die Vorteile von VTEC und VTEC-E, indem sie drei Betriebsmodi bietet: einen für niedrige Drehzahlen mit Schwerpunkt auf Kraftstoffeffizienz, einen für mittlere Drehzahlen und einen für hohe Drehzahlen mit maximaler Leistung.
i-VTEC
Das „intelligente“ VTEC integriert die variable Ventilsteuerung mit der kontinuierlichen Verstellung der Ventilsteuerzeiten (Variable Timing Control, VTC). Dadurch wird eine noch feinere Anpassung der Motorleistung über den gesamten Drehzahlbereich ermöglicht. Dieses System wird in vielen modernen Honda-Modellen eingesetzt.
Fahrzeuge mit VTEC-Motoren
Hondas VTEC-Technologie wurde in einer Vielzahl von Fahrzeugen implementiert:
- Honda Civic: Mehrere Generationen des Civic, insbesondere die sportlichen Si- und Type R-Modelle, nutzen VTEC für gesteigerte Leistung.
- Honda Accord: VTEC-Motoren wurden in verschiedenen Accord-Modellen eingesetzt, um ein Gleichgewicht zwischen Leistung und Kraftstoffeffizienz zu erreichen.
- Honda Integra: Bekannt für seine sportliche Ausrichtung, profitierte der Integra früh von der DOHC-VTEC-Technologie.
- Honda CR-V: Dieses kompakte SUV nutzt VTEC, um sowohl Stadtfahrten als auch Autobahnfahrten effizient zu gestalten.
- Honda S2000: Der Roadster ist berühmt für seinen hochdrehenden VTEC-Motor, der beeindruckende Leistung aus einem 2,0-Liter-Aggregat liefert.
- Honda Prelude: Dieses Sportcoupé integrierte VTEC, um Fahrspaß mit Alltagstauglichkeit zu verbinden.
Diese Liste ist nicht abschließend; viele weitere Honda-Modelle, einschließlich Motorräder wie die Honda VFR 800, nutzen die Vorteile der VTEC-Technologie.
Vergleichbare Systeme anderer Hersteller
Mehrere Automobilhersteller haben eigene Systeme zur variablen Ventilsteuerung entwickelt, die ähnliche Ziele wie VTEC verfolgen:
- BMW VANOS und Valvetronic: BMWs VANOS-System passt die Nockenwellensteuerzeiten an, während Valvetronic zusätzlich den Ventilhub variiert, um die Motorleistung und Effizienz zu optimieren.
- Toyota VVT-i: Das „Variable Valve Timing with intelligence“ passt die Steuerzeiten der Nockenwelle kontinuierlich an, um die Motorleistung und den Kraftstoffverbrauch zu verbessern.
- Mitsubishi MIVEC: „Mitsubishi Innovative Valve timing Electronic Control“ kombiniert variable Ventilsteuerung mit variabler Ventilhubsteuerung, um Leistung und Effizienz zu maximieren.
- Fiat MultiAir: Dieses System steuert den Einlassventilhub elektrohydraulisch, was eine präzise Kontrolle des Luftstroms und eine Verbesserung der Verbrennungseffizienz ermöglicht.
- Nissan VVL: „Variable Valve Lift and Timing“ ermöglicht es, sowohl den Ventilhub als auch die Steuerzeiten anzupassen, um die Motorleistung zu optimieren.
Ein Beitrag von: