Ein Drittel des neuen GE-Triebwerks stammt aus dem 3D-Drucker
Der amerikanische Flugzeugmotoren-Hersteller General Electric setzt stärker auf 3D Druck als bislang jeder Konkurrent in der Welt: Vom neuen ATP-Turboprop-Triebwerk kommt mehr als ein Drittel aus dem 3D Drucker. Dieser Motor wird in das ebenfalls neue Business-Flugzeug Denali des amerikanischen Herstellers Textron Aviation eingebaut.
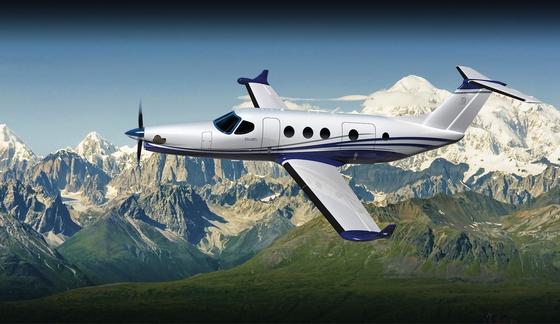
In die neue Cessna Denali des amerikanischen Herstellers Textron Aviation kommt ein ATP-Turboprop-Triebwerk von General Electric. Das Besondere: Ein Drittel der Komponenten stammt aus dem 3D-Druck mit Metallpulver.
Foto: Textron Aviaton
General Electric Aviation, der größte Flugtriebwerk-Hersteller der Welt, beschäftigt sich schon seit 2010 mit dem 3D Druck von Motor-Komponenten. Zu den ersten in großer Serie produzierten Teilen gehören die Einspritzdüsen aus Kobalt-Chrom für die neuen “Leap”-Motoren, die von General Electric im Rahmen des Joint Ventures CFM mit Safran in Frankreich für den Antrieb von Verkehrsflugzeugen – darunter auch der Airbus A320neo – hergestellt werden. Bei dem neuen ATP-Motor für sehr viel kleinere Flugzeuge ist General Electric einen anderen Weg gegangen und hat dabei den 3D Druck von Beginn an in die Entwicklung des Motors mit einbezogen. Das begann schon beim Design.
Dieser neue Motor wird gegenwärtig im GE-Testzentrum in Prag in Tschechien ausgiebig getestet. Dort hat General Electric den größten Teil der Entwicklung von Turboprop-Triebwerken konzentriert. Zugleich ist Prag auch der Sitz des Geschäftsbereichs ATP-Motoren (Advanced Turboprop) geworden.
Ungleich weniger einzelne Teile im Motor
Wie Chefingenieur Mohamed Ehteshami von ATP erläutert, ist es durch den 3D Druck möglich geworden, in diesem Motor mit sehr viel weniger nicht-beweglichen Komponenten auszukommen. Die Zahl dieser Teile ist zunächst von mehr als 900 auf nur noch 16 reduziert worden.
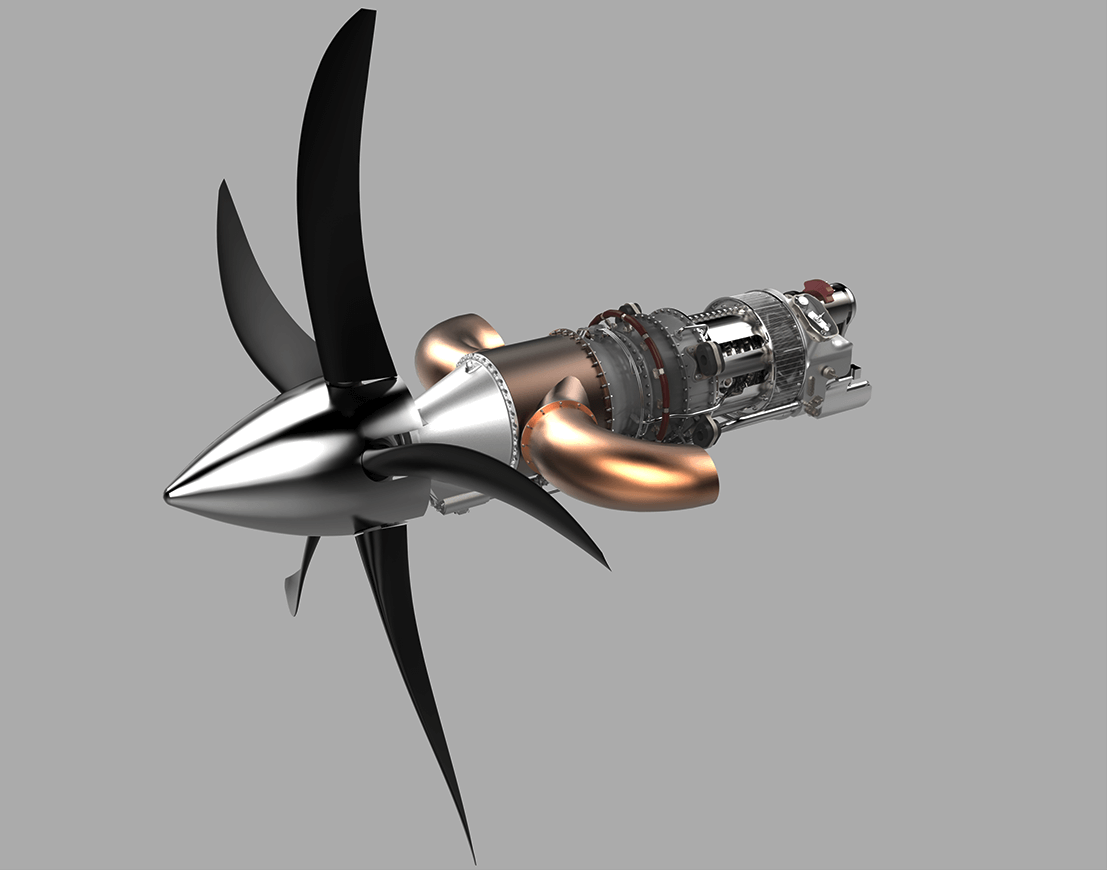
Beim neuen Turboprop für die Cessna Denali setzt der amerikanische Triebwerkshersteller GE Aviation noch mehr als bisher auf additive Fertigung.
Quelle: GE Aviation
Das hat für diese Teile zu einer Gewichtseinsparung von 35 % geführt. Während der Entwicklung erwies sich diese Möglichkeit zur Komponenten- und damit auch Gewichtseinsparung als so gravierend, dass General Electric kurzerhand den Entwicklungsprozess temporär stoppte, um den Motor im Design noch stärker in Richtung auf gedruckte Teile auszurichten.
Dabei gelang es schließlich insgesamt 855 Einzelteile durch nur noch zwölf gedruckte Komponenten zu ersetzen. Das reicht vom Motor-Rahmen über die Brennkammer-Auskleidung und über den Ölsumpf-Behälter bis hin zu den Wärmetauschern und der Abgas-Anlage.
Motor und Flugzeug sind insgesamt leichter geworden
Die Konzentration auf sehr viel weniger und damit schließlich auch insgesamt leichtere Komponenten hat dann dazu geführt, dass das komplette Denali-Flugzeug von Cessna Textron allein durch den sehr viel leichteren Motor insgesamt fünf Prozent weniger wiegt. Wie Ehteshami anfügt, führt das wiederum als Konsequenz zu einem Rückgang des spezifischen Treibstoffverbrauchs des Denali-Flugzeugs um ein Prozent.
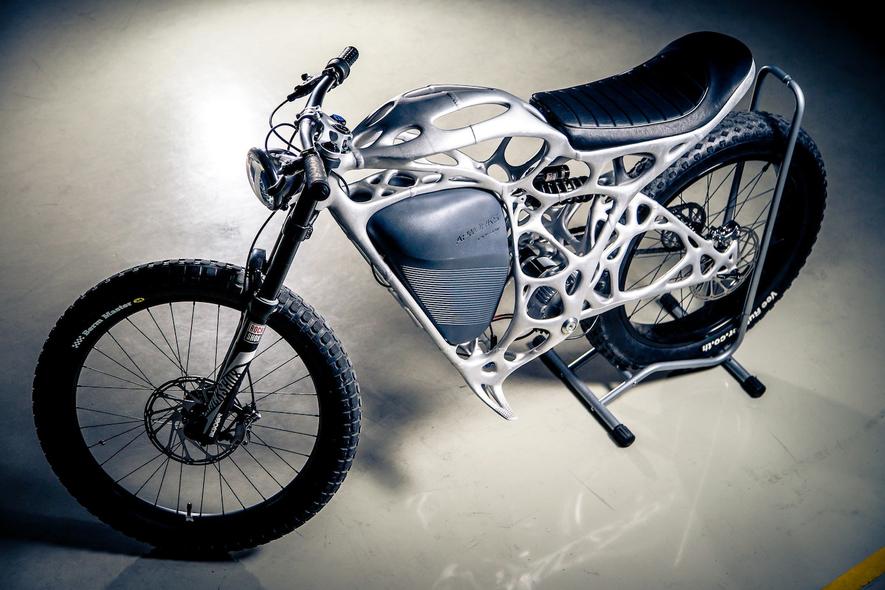
Das Light Rider der Airbus-Tochter APWorks ist ein Elektromotorrad, dessen Rahmen im 3D-Drucker entstanden ist und ganze 6 kg wiegt.
Quelle: APWorks
Auch Rolls-Royce nutzt den 3D-Druck für die Herstellung großer Triebwerkteile. Einen Artikel dazu finden Sie hier. Und viele spannende Geschichten rund um den 3D-Druck verbergen sich hinter diesem Link.
Ein Beitrag von: