Elektroauto-Recycling: Warum effiziente Demontage von Batterien und Motoren wichtig ist
Ein wichtiger Aspekt des Elektroauto-Recyclings ist die effiziente Demontage von Batterien und Motoren. Erfahren Sie, warum dies so wichtig ist und wie neue Technologien dazu beitragen können, den Recyclingprozess zu verbessern.
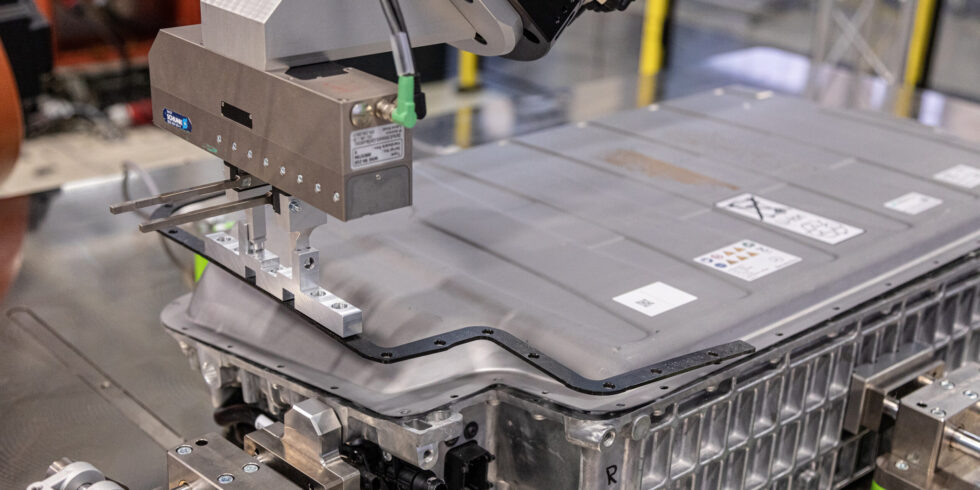
Die automatisierte Demontage mit einem extra entwickelten Kleinteilegreifer.
Foto: © Fraunhofer IPA/
Foto: Rainer Bez
Die Elektromobilität wird zunehmend zur Zukunft der Automobilbranche. Immer mehr Elektrofahrzeuge sind bereits auf den Straßen unterwegs. Allerdings haben Batteriesysteme im Durchschnitt nur eine Lebensdauer von etwa zehn Jahren. Und das heißt: der Anstieg an ausgedienten Batterien ist nicht zu vermeiden, was uns stets vor neuen Herausforderungen in Bezug auf deren Entsorgung und Recycling der elektrischen Komponenten stellt.
Zwölf Forschungspartner haben im Rahmen des baden-württembergischen Projekts DeMoBat (Industrielle Demontage von Batterien und E-Motoren) gearbeitet und neue Konzepte und Technologien entwickelt, um die elektrischen Komponenten so zu handhaben und aufzubereiten, dass möglichst wenig Abfall entsteht und wenig verwendete Rohstoffe verloren gehen. Insbesondere für Baden-Württemberg, das sehr stark von der Automobilindustrie geprägt ist, ist ein solches Forschungsvorhaben entscheidend. Das Fraunhofer IPA hatte die Koordination des Projekts inne, welches vom Ministerium für Umwelt, Klima und Energiewirtschaft Baden-Württemberg finanziell gefördert wurde. Im Projekt waren acp systems AG, BTU Cottbus – Fachgebiet Physikalische Chemie, CTC battery technology GmbH, CUTEC Clausthaler Umwelttechnik Forschungszentrum, ERLOS GmbH, Greening GmbH & Co. KG, Hochschule Esslingen, KIT – Institute for Industrial Production (IIP), KIT – wbk Institut für Produkti onstechnik, Mercedes Benz AG, Siemens AG, Silberland Sondermaschinenbau GmbH beteiligt.
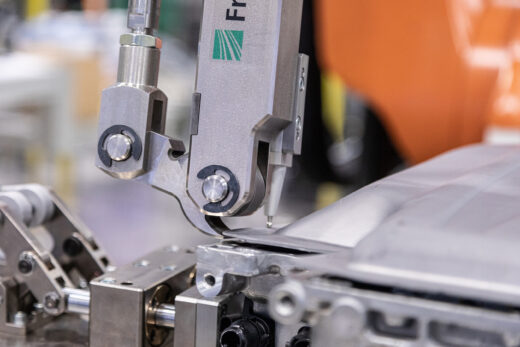
Es wurde ein Werkzeug namens „Knacker“ entwickelt, um Klebeverbindungen zwischen der Ober- und Unterschale einer Batterie zu lösen. © Fraunhofer IPA/
Foto: Rainer Bez
Das neue Life-Cycle-Datenmanagement entwickelt
„Ein entscheidender Faktor, um im Wettbewerb bestehen zu können, sind die Verfügbarkeit und Kosten der Rohstoffe, die für Batterien und E-Motoren nötig sind“, erklärte Professor Alexander Sauer, Leiter des Fraunhofer IPA sowie des Projekts. „Umso wichtiger ist es, ausgediente Batterien, die noch wertvolle Rohstoffe enthalten, nicht einfach zu schreddern, wie es bisher üblich ist.“ Die Grundvoraussetzung, um Batteriekomponenten wiederverwenden zu können, sei, dass die Bestandteile einer Batterie sortenrein demontiert werden können.
Das Projekt hat das Ziel, die Nachhaltigkeit im Bereich der Elektromobilität zu fördern, wirtschaftsstrategische Rohstoffe zu sichern und den Wirtschaftsstandort Baden-Württemberg und Deutschland zu stärken. Zu diesem Zweck haben die Projektbeteiligten zunächst die rechtlichen Rahmenbedingungen untersucht und eine Analyse der Marktpotenziale und Rücklaufmengen von Autobatterien durchgeführt. Darauf aufbauend wurden mögliche Geschäftsmodelle abgeleitet und bewertet. Die Arbeiten wurden durch ein neu entwickeltes Life-Cycle-Datenmanagement sowie durch eine Kostenanalyse von Demontage- und Recyclingnetzwerken bis ins Jahr 2050 ergänzt.
Design der Batterien ist für eine erfolgreiche industrielle Demontage wichtig
Ein wesentlicher Faktor für eine erfolgreiche industrielle Demontage von Batterien ist auch das entsprechende Design der Batterien. Wie sollte eine Batterie am besten gestaltet werden, um eine manuelle oder robotergestützte Reparatur oder Demontage zu ermöglichen? Eine Herausforderung besteht dabei in den zahlreichen unterschiedlichen Batteriemodellen der verschiedenen Automarken und -modelle, deren Bauweise derzeit noch nicht für ein Recycling oder alternative Kreislaufwirtschaftsstrategien geeignet ist. Deshalb wurde im Rahmen des Projekts auch ein recycelfreundliches Design konzipiert und eine demontagegerechte Batterie prototypisch aufgebaut und umfassend untersucht.
Flexibles Demontagesystem entwickelt
Zudem wurden spezielle Werkzeuge entworfen, die Objekte greifen und Schrauben und Verbindungen lösen können. Wichtig dabei ist eine leistungsstarke Bildverarbeitung, um eine Vielzahl an Schrauben, Kabeln und anderen Komponenten zu erkennen. Es muss auch berücksichtigt werden, dass manche Komponenten aufgrund von Alterungseffekten nicht immer leicht zu erkennen sind.
Insgesamt wurden im Rahmen des Projekts 25 Technologien entworfen und erprobt. Acht davon wurden vollständig als Demonstrations- und Erprobungsroboterwerkzeuge umgesetzt und könnten für den Dauerbetrieb in der Industrie eingesetzt werden. Das flexible Demontagesystem, das im Projekt entwickelt wurde, ermöglicht eine zerstörungsfreie Demontage bis auf Zellebene. Ein wichtiger Bestandteil des Sicherheitskonzepts ist die Verwendung von Temperatur als möglicher Indikator für eine Kettenreaktion im Falle eines Brandes in einer Batterie.
Wasserbasierte Recycling und Einsatz von Industrierobotern
Die Projektpartner strebten auch die Schaffung eines effizienten Wertschöpfungskreislaufs an, der durch die mechanische Trennung und Rückführung der Bestandteile im Batteriepack realisiert werden sollte. Eine neuartige Form der direkten Wiedergewinnung von Schwarzmasse erfolgt durch das eingesetzte wasserbasierte Recycling. Eine teilautomatisierte Öffnung und Separierung der Zellbestandteile wird durch den Einsatz von Hochdruckwasserstrahl ermöglicht, um die Elektrodenbeschichtung von den Trägerfolien abzulösen. Eine ökobilanzielle Untersuchung ergab einen Effizienzgewinn von Faktor 10 bis 20 im Vergleich zu herkömmlichen Verfahren. Dies führt dazu, dass Rezyklate mit einem geringen CO2-Fußabdruck bereitgestellt werden können, was bei hoher Beimengung die produktionsbezogenen Treibhausgasemissionen deutlich reduziert.
Darüber hinaus wurden Technologien für den Einsatz von Industrierobotern mit speziellen Werkzeugen entwickelt, um elektrische Antriebsaggregate automatisch demontieren zu können. Auch hier werden Bildverarbeitungssysteme eingesetzt, um Schrauben und Bauteile zu erkennen und das manuelle Programmieren des Roboters für jeden einzelnen Schritt zu vermeiden. Zur Vermeidung von Kollisionen des Roboters mit Bauteilen wird nach jedem Demontageschritt eine Überprüfung mit Sensoren und 3D-Kameras durchgeführt. Eine sichere Signalübertragung an die zentrale Prozesssteuerung gewährleistet einen sicheren Prozessablauf.
Aufbau eines Erprobungszentrums
Die in DeMoBat entwickelten Technologien dienen als Grundlage für den Aufbau eines Erprobungszentrums, in dem neue Formen der Batterieproduktion entwickelt und getestet werden können. Außerdem wird das Recycling von E-Komponenten weiterentwickelt.
„Damit trägt das Projekt dem essenziellen Technologietransfer Rechnung, mithilfe dessen Baden-Württemberg wie auch Deutschland beim Thema E-Komponenten-Recycling in eine Spitzenposition gebracht werden sollen“, resümierte Professor Kai Peter Birke, der am Fraunhofer IPA das Zentrum für digitalisierte Batteriezellenproduktion leitet.
Ein Beitrag von: