Hybridrohre machen Autos leichter
Rohre, die nur an stark belasteten Stellen aus Stahl, an den übrigen aus Aluminium bestehen, reduzieren das Fahrzeuggewicht. Bisher ließen sich solche Rohre nicht umformen. Hannoveraner Forscher haben jetzt doch einen Weg gefunden: Es funktioniert mit Laserlöten.
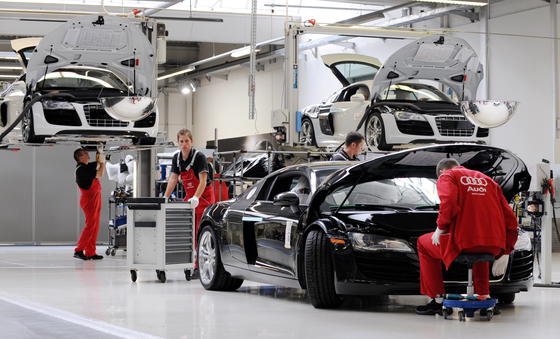
Leichtbau ist ein großes Thema in der Autoindustrie. Forscher aus Hannover haben jetzt ein Verfahren gefunden, mit denen sich Hybridrohre aus Stahl und Alu umformen lassen. Der Einsatz soller Rohre trägt zur Gewichtsreduzierung bei.
Foto: Bernd Weißbrod/dpa
Eine Gitterstruktur aus Rohren, die mit Blech- oder faserverstärktem Kunststoff verkleidet wird, ist leichter als eine Karosserie ohne diese Stützkonstruktion. Noch leichter wird eine solche Autohülle, wenn die Rohre nicht aus Stahl, sondern aus Aluminium sind. Dieser Werkstoff ist allerdings zu weich, um beispielsweise Kräfte abzufangen, wie sie bei Unfällen auftreten.
Spröde Nähte durch Schweißen
Der Kompromiss heißt Hybridrohr. Dort, wo schwache Kräfte auftreten, reicht das leichtere Metall. Ansonsten muss es eben Stahl sein. Derartige Rohre lassen sich durchaus fertigen. Doch bei der gängigen Hochdruckinnenverformung, mit der diese Rohre verformt werden, reißt die Schweißstelle, an der die beiden Materialien aneinanderstoßen, weil sie spröde ist.
Die Lösung haben jetzt Wissenschaftler am Institut für Integrierte Produktion Hannover der Universität und des Laser Zentrums Hannover gefunden. Sie fügen die Rohre mit Aluminium-Silizium-Lot zusammen. Das Lot wird per Laser verflüssigt, sodass es sich mit den Rohrenden verbindet. Selbst bei einem Druck von 900 bar, das ist mehr als 400 Mal so viel wie in einem Pkw-Reifen, bleibt die Lötstelle dicht.
Wasser bringt die Rohre in Form
Muss sie auch, denn ein solch gigantischer Druck ist nötig, um die Hybridrohre – so genannt, weil sie aus zwei Werkstoffen bestehen – in die benötigte Form zu bringen. Dazu werden sie in ein massives Werkzeug mit der gewünschten Form gelegt.
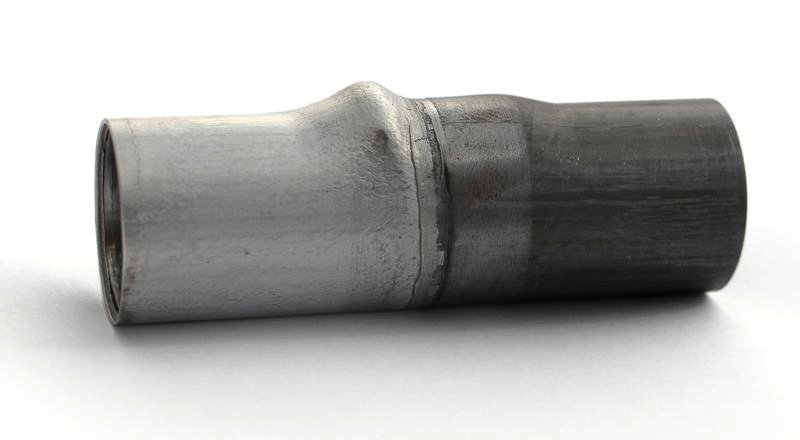
Erfolgreicher Umformversuch: Dieses Rohr besteht zur Hälfte aus Aluminium und zur Hälfte aus Stahl. Die lasergelötete Fügezone hielt der Innenhochdruckumformung stand.
Quelle: IPH
Eine Seite des Rohrs wird abgedichtet, in die zweite Öffnung presst eine Pumpe Wasser oder ein Gemisch aus Öl und Wasser. Bei einem Druck von 900 bar – für andere Anwendungen sind Drücke von bis zu 3000 bar nötig – schmiegt sich das Rohr an die Werkzeugform.
Autohersteller sparen einen Arbeitsschritt ein
Das Verfahren der Hannoveraner Wissenschaftler ist aus zwei Gründen wichtig. Eingesetzt in der Automobilherstellung spart es einen Arbeitsschritt ein, weil sich zwei Werkstoffe, die auf die Kräfte, die beim Innendruckumformen auftreten, im Prinzip unterschiedlich reagieren, gleichzeitig verformen lassen. Außerdem sind Fahrzeuge, die mit solchen Hybridrohren ausgestattet werden, leichter, verbrauchen also weniger Treibstoff und entlasten damit die Umwelt.
Ihre Forschungsergebnisse stellen die Wissenschaftler auf der EuroBLECH vor, die vom 25. bis 29. Oktober 2016 auf dem Messegelände in Hannover stattfindet.
Auch bei Zügen spielt das Thema Leichtbau in Hinblick auf den Energieverbrauch eine immer größere Rolle. Im Zusammenhang damit tüfteln Ingenieure des DLR an einem neuartigen Crashkonzept für Züge. Herzstück sind Deformationszonen. Sie sollen Passagiere bei einem Zusammenstoß schützen. Mehr dazu lesen hier.
Ein Beitrag von: