„Leichtbau ist die Königsdisziplin“
Leichtbaustrategien für den Automobilbau – Mit den CO2-Zielen der EU hat für Leichtbauer der Automobilindustrie eine neue Ära begonnen. Erstmals seit Jahrzehnten gelingt es, die Gewichtsspirale umzudrehen.
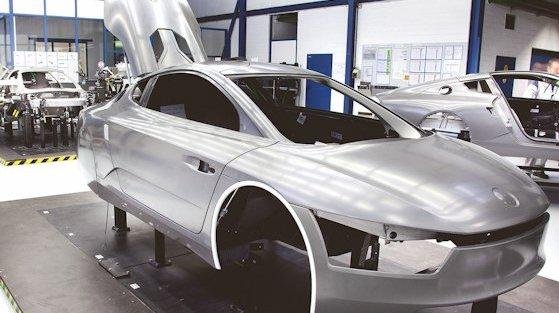
Ein echtes Leichtgewichte: Das 1-Liter-Auto XL1 von VW wiegt gerade einmal 795 Kilogramm.
Foto: VW
„Auch wenn die EU das 95-g-Ziel für 2020 noch nicht in eine Direktive überführt hat, bekennt sich Volkswagen zu diesem Ziel.“ So begann Armin Plath, Verantwortlicher für Werkstoffe und Fertigungsverfahren in der VW-Konzernforschung, seinen Auftaktvortrag zum 3. VDI-Fachkongress „Leichtbaustrategien für den Automobilbau“ in Wolfsburg.
Als Automobil-Leichtbauer kennt Plath die Bedeutung der CO2-Regulierung für seine Disziplin. Bisher hielten Leichtbauer die Gewichtszunahme von einer Modellgeneration zur nächsten im Zaum. „Wir können stolz sein, dass die durchschnittliche Fahrzeugmasse trotz Verbesserungen bei Sicherheit und Komfort in den letzten 30 Jahren nur um 40 % gestiegen ist“, brachte es Boris Shulkin, stellvertretender Forschungschef von Magna International, auf den Punkt.
Neue Ära
Doch mit dem CO2-Flottenziel von 95 g/km in der EU und ähnlichen Zielen in den USA, Japan und China beginnt eine neue Ära. Die Gewichtsspirale wechselt die Richtung. Selbst der VW Golf, das Volumenmodell schlechthin, speckte zuletzt 70 kg ab.
Für Plath erst der Anfang: „Leichtbau kommt eine wichtige Rolle dabei zu, die CO2-Ziele auch über 2020 hinaus zu erreichen.“ Horst Friedrich, Direktor des DLR-Instituts für Fahrzeugkonzepte, Stuttgart, erklärte den Leichtbau gar zur „Königsdisziplin für das Automobil“. Spätestens wenn es um aktuell diskutierte CO2-Ziele von 68 g/km bis 78 g/km gehe, werde Leichtbau ein Muss.
Friedrich mahnte zugleich Realismus an: 100 kg weniger Gewicht liefen auf 0,15 l/100 km Verbrauchssenkung hinaus. Wenn auch Motor und Getriebe angepasst werden, seien maximal 0,4 l/100 km drin. Bei Elektroautos sieht er mehr Potenzial: „Ein Viertel weniger Gewicht steigert die Reichweite in Simulationen typisch städtischer Zyklen um 28 %.“
Der kleine Plug-in-Hybrid VW XL1 nutzt diesen Vorteil. Dank Carbonstofffaserverbunden (CFK) wiegt er nur 795 kg. Bis zu 50 km fährt er elektrisch, ehe sein 0,8-l-Turbodieselmotor einsetzt. Im EU-Normzyklus erreicht er ganze 21 g CO2/km – was dem für 2050 anvisierten CO2-Reduktionsziel um 80 % gegenüber 1990 entspricht.
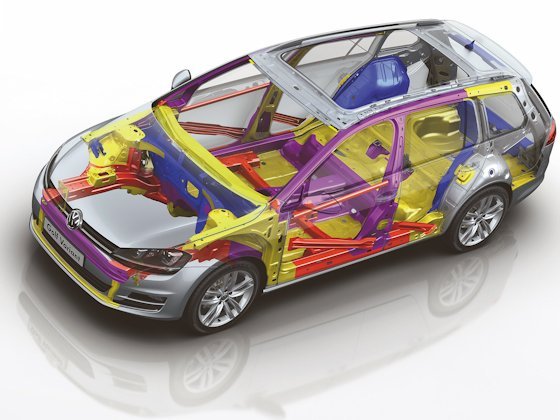
Der VW-Golf Variant wird gebaut mit einem Mix warm umgeformter (lila), ultrahoch- (rot), höchst- (gelb) und hochfester (blau) Stähle.
Quelle: VW
Doch noch ist CFK Kleinserienmodellen vorbehalten. Heinrich Timm, Vordenker der Aluminium-Spaceframe-Bauweise bei Audi, erklärte, warum: „Beim Lamborghini Gallardo Spyder hatten wir die Motorhaube anfangs in Aluminium geplant. Doch waren die Anlagen- und Werkzeugkosten so hoch, dass es bei geplanten sieben Fahrzeugen pro Tag weit günstiger war, die Haube im Manufaktur-Prozess aus CFK zu fertigen.“ Geringere Werkzeugkosten gaben den Ausschlag für den teureren Werkstoff.
VW setzt im Volumenmarkt vorerst auf Stahlleichtbau
Im Volumenmarkt setzt VW aber vorerst auf Stahlleichtbau. Im Golf VII stieg der Anteil warm umgeformter Martensit-Stähle auf 24 % gegenüber 6 % beim Vorgänger. Gewichtsvorteil: 23 kg. Vergleichbare Sicherheit hätte im alten Stahlmix über 50 kg mehr gewogen. „Wir sehen Potenzial, um Stähle zu noch mehr Festigkeit und Duktilität zu entwickeln und weitere Gewichtsvorteile in Großserien zu erzielen“, sagte Plath. Zentraler Vorteil des Stahlleichtbaus: geringere Kosten.
CO2-Ziele werden Materialmix verändern
Doch werden die CO2-Ziele den Materialmix im Volumenmarkt verändern. „Wir arbeiten an optimierten Aluminium-Stahl-Mischbauweisen und wollen sehr gezielt Faserverbundwerkstoffe einsetzen“, berichtete Plath. VW wird künftig mit 30 Industrie- und Wissenschaftspartnern, darunter BASF, Magna, DLR und CFK-Valley Stade, in einer 120 Mio. € teuren Forschungsfabrik in Wolfsburg an solchen Hybrid-Karosserien arbeiten. Die „Open Hybrid Lab Factory“ soll großserientaugliche Leichtbaukonzepte samt Fertigungsprozessen entwickeln.
Bauteile in einem Takt herstellen
„Ziel ist es, Bauteile wie bisher in einem Takt herzustellen“, sagte Plath. Dafür gelte es, neue Technologien zu verbinden: integriertes Fügen, Umformen von Organoblechen und Metallen, textile Halbzeuge für den lastpfadgerechten Einsatz von Hochleistungsfasern oder Injektionsspritzen der thermo- oder duroplastischen Harze. Weitere Forschungsfelder: die unterschiedliche Materialausdehnung, Kontaktkorrosion oder crashfestes Verbinden der Metalle und Kunststoffe.
Zentral bleibt die Kostenfrage. Bisher liegen die Leichtbau-Grenzkosten bei 2,50 €/kg Gewichtssenkung. Mit dem 95-g-Ziel der EU und den drohenden Strafzahlungen werden laut Plath bis zu 10 €/kg akzeptabel.
Ein Beitrag von: