Mercedes-Benz startet CO₂-neutrales Recycling von E-Auto-Batterien
Mercedes-Benz eröffnet eine CO₂-neutrale Recyclingfabrik für E-Auto-Batterien. Ziel ist es, wertvolle Rohstoffe wie Lithium, Nickel und Kobalt wiederzuverwerten.
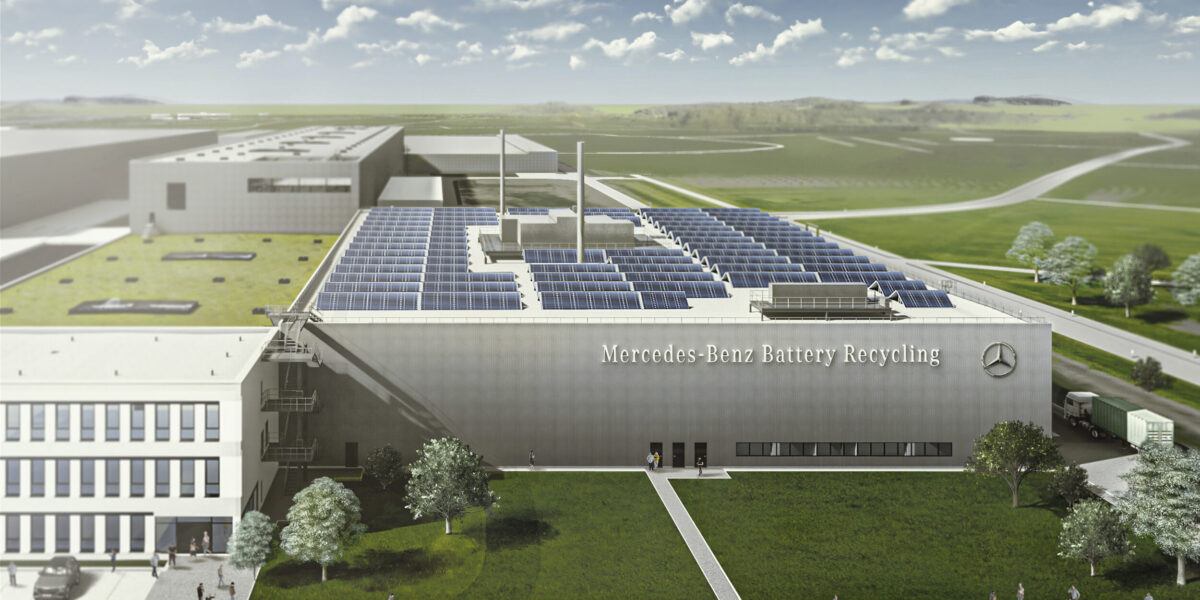
Mit der neuen Batterie-Recyclingfabrik möchte Mercedes-Benz E-Autos umweltfreundlicher machen.
Foto: Mercedes-Benz
Am 21. Oktober eröffnete Mercedes-Benz in Kuppenheim (Kreis Rastatt) seine erste Recyclingfabrik für Elektroauto-Batterien. In der neuen Anlage sollen Rohstoffe wie Lithium, Nickel und Kobalt aus alten Batterien gewonnen werden. Die Fabrik soll CO₂-neutral arbeiten und mithilfe von Solarenergie und externem Ökostrom betrieben werden. Bundeskanzler Olaf Scholz und Baden-Württembergs Umweltministerin Thekla Walker waren bei der Eröffnung anwesend.
Inhaltsverzeichnis
- Batterie-Recycling ein komplexer Prozess
- Technische Herausforderung des Recyclings
- Nachhaltige Recyclingtechnologie setzt neue Maßstäbe
- Pioniere des Batterie-Recyclings in Deutschland
- Recycling wird sich erst ab 2030 lohnen
- Recycling als Schlüssel zur Rohstoffsicherung
- VDI sieht Eröffnung der Recyclingfabrik als Meilenstein
Batterie-Recycling ein komplexer Prozess
Das Batterie-Recycling ist ein komplexer Prozess, der für die Elektromobilität von zentraler Bedeutung ist. Die Automobilindustrie sucht nach Lösungen, um die Umweltbelastung durch den steigenden Bedarf an Batterierohstoffen zu verringern. Mercedes-Benz hat hierfür einen zweistelligen Millionenbetrag investiert. Zudem wird das Projekt vom Bund mit knapp 17 Millionen Euro gefördert.
Ziel der neuen Recyclinganlage ist es, den wertvollen Rohstoffkreislauf zu schließen und die Abhängigkeit von neuen Ressourcen zu verringern. Dies ist nicht nur ökologisch sinnvoll, sondern auch strategisch wichtig, da Europa stark von der Rohstoffversorgung aus Asien abhängig ist. Nickel, Lithium und Kobalt werden in der Region kaum abgebaut, während Europa jährlich rund 800.000 Tonnen Auto-Batterien importiert.
Technische Herausforderung des Recyclings
Das Recycling von Batterien ist technisch herausfordernd. Ein Grund dafür sind die unterschiedlichen Bauformen und Größen der Akkus. Diese machen eine vollautomatische Verarbeitung schwierig, weshalb der Zerlegeprozess oft manuell erfolgt.
Traditionelle Verfahren nutzen Energie-intensive Methoden, bei denen die Batterien zerkleinert und erhitzt werden, um die Metalle herauszufiltern. Bei dieser Methode beträgt die Recyclingquote maximal 70 %. Fortschrittlichere Ansätze, wie das Baden der Batterien in Säure, erhöhen die Recyclingquote auf bis zu 96 %. Mercedes-Benz strebt an, diese effizienteren Technologien in ihrer neuen Fabrik zu nutzen.
Nachhaltige Recyclingtechnologie setzt neue Maßstäbe
Die Recyclingtechnologie, die in der neuen Mercedes-Benz Fabrik eingesetzt wird, gilt als wegweisend für die Branche. Zum ersten Mal werden in Europa alle Schritte von der Zerkleinerung der Batteriemodule bis hin zur Trocknung und Aufbereitung der wertvollen Rohstoffe abgedeckt. Im mechanischen Teil des Prozesses werden Materialien wie Kunststoffe, Kupfer, Aluminium und Eisen sauber voneinander getrennt.
Anschließend wird im hydrometallurgischen Verfahren die sogenannte „schwarze Masse“ verarbeitet, die die aktiven Materialien der Batteriezellen enthält. In einem mehrstufigen chemischen Prozess werden Metalle wie Kobalt, Nickel und Lithium extrahiert und für den Einsatz in neuen Batterien aufbereitet. Im Vergleich zu herkömmlichen Methoden, die meist auf pyrometallurgische Verfahren setzen, ist das hydrometallurgische Verfahren von Mercedes-Benz energieeffizienter und produziert weniger Abfall. Es arbeitet bei Temperaturen von bis zu 80 Grad Celsius und verbraucht deutlich weniger Energie. Die Recyclinganlage wird bilanziell CO₂-neutral betrieben und vollständig mit Grünstrom versorgt.
Ola Källenius, Vorstandsvorsitzender der Mercedes-Benz Group AG, betonte die strategische Bedeutung des Projekts: „Mercedes-Benz hat sich das ambitionierte Ziel gesetzt, die begehrenswertesten Autos der Welt auf die nachhaltigste Art und Weise zu bauen. Mit der Eröffnung der ersten mechanisch-hydrometallurgischen Recyclingfabrik in Europa setzen wir einen bedeutenden Meilenstein auf dem Weg zu mehr Nachhaltigkeit im Umgang mit Rohstoffen. Gemeinsam mit unseren Partnern aus der Wirtschaft und Wissenschaft machen wir deutlich, dass Innovation und Nachhaltigkeit Hand in Hand gehen, um die Elektromobilität der Zukunft voranzutreiben.“
Pioniere des Batterie-Recyclings in Deutschland
Deutschland hat bereits eine Vorreiterrolle beim Thema Batterie-Recycling übernommen. Volkswagen betreibt seit 2021 eine Pilotanlage in Salzgitter, und auch BASF hat kürzlich eine Recyclinganlage in Schwarzheide eröffnet. Zudem arbeitet Mercedes-Benz mit Primobius, einem spezialisierten Recyclingunternehmen, zusammen. Die größte Anlage in Europa befindet sich jedoch in Magdeburg und wird von einer kanadischen Firma betrieben.
Laut einer Statistik werden weltweit 24 % aller Lithium-Ionen-Batterien in Deutschland recycelt – ein Spitzenwert im Vergleich zu anderen Regionen wie den USA oder Asien.
Recycling wird sich erst ab 2030 lohnen
Derzeit ist das Recycling von Batterien noch nicht wirtschaftlich lukrativ. Ein Grund dafür ist die Langlebigkeit der Akkus. Diese halten in Elektrofahrzeugen bis zu 15 Jahre und haben danach noch etwa 80 % ihrer Kapazität. Statt sie sofort zu recyceln, werden sie oft als Speicher für Solaranlagen weiterverwendet. Erst wenn ihre Leistungsfähigkeit stark nachlässt, werden sie zur Wiederverwertung gebracht. Das Fraunhofer-Institut prognostiziert, dass ab 2030 größere Mengen an Altbatterien auf den Markt kommen werden – schätzungsweise 420.000 Tonnen allein in Europa.
Recycling als Schlüssel zur Rohstoffsicherung
Die wachsende Nachfrage nach Elektrofahrzeugen führt zu einem steigenden Bedarf an seltenen Rohstoffen. Gleichzeitig nehmen die Vorräte an neuen Rohstoffen ab. Die Bundesanstalt für Geowissenschaften und Rohstoffe warnt davor, dass es bereits Ende des Jahrzehnts zu Engpässen bei der Lithiumversorgung kommen könnte. Daher ist es entscheidend, die Recyclingquoten zu erhöhen, um den Rohstoffbedarf langfristig zu decken.
Ein weiterer Vorteil des Recyclings ist die Reduktion der CO₂-Emissionen. Die Rückgewinnung von Lithium aus alten Batterien ist deutlich umweltschonender als der Abbau neuer Rohstoffe. Zudem hat die EU strenge Vorgaben für die Wiederverwertung von Batterien gesetzt. Ab 2031 müssen neue Akkus bestimmte Recyclingquoten erfüllen.
VDI sieht Eröffnung der Recyclingfabrik als Meilenstein
VDI-Direktor Adrian Willig begrüßt die Eröffnung der Batterie-Recyclingfabrik in Kuppenheim und fordert mehr solcher Initiativen, um technologisch vorne zu bleiben: „Die Batterie-Recyclingfabrik von Mercedes-Benz ist ein Meilenstein, weil sie durch eine hohe Recyclingquote Rohstoffe effizient zurückführt und somit die Abhängigkeit vom globalen Markt verringert. Dies senkt Treibhausgasemissionen und stärkt die nachhaltige Mobilität“, erklärt Willig.
Der VDI-Direktor weiter: „Der VDI betont, dass E-Mobilität nur dann klimafreundlich wird, wenn sowohl die Produktion als auch das Recycling „grün“ sind. Nun muss diese Technologie auf industriellen Maßstab skaliert werden, um die volle Wirkung zu entfalten und langfristige Nachhaltigkeit zu sichern“. Der VDI hat bereits in seiner Ökobilanzstudie aus 2023 betont, dass E-Mobilität erst dann klimafreundlich ist, wenn die gesamte Batterieproduktion und -verwertung ‚grün‘ wird. Recycling spielt dabei eine zentrale Rolle. „Jetzt wird es auf eine Skalierung auf einen industriellen Maßstab ankommen“, meint Willig.
Weiterführende Links:
Publikation Metastudie Zukunft Deutschland 2050 | VDI
Deutschland 2050: innovative Wege zum Zukunftsstandort | VDI
Erst die grüne Batterie macht die E-Mobilität klimafreundlich | VDI
Ein Beitrag von: