Neue Technologie für eine bessere Beschichtung von Triebwerken
Ideale Schutzschichten sind extrem dünn und trotzdem lange haltbar. Ein Forscherteam hat ein neues Spritzverfahren entwickelt, um diese Bedingungen erfüllen zu können. Die Anwendung soll mit verhältnismäßig geringen Kosten verbunden sein.
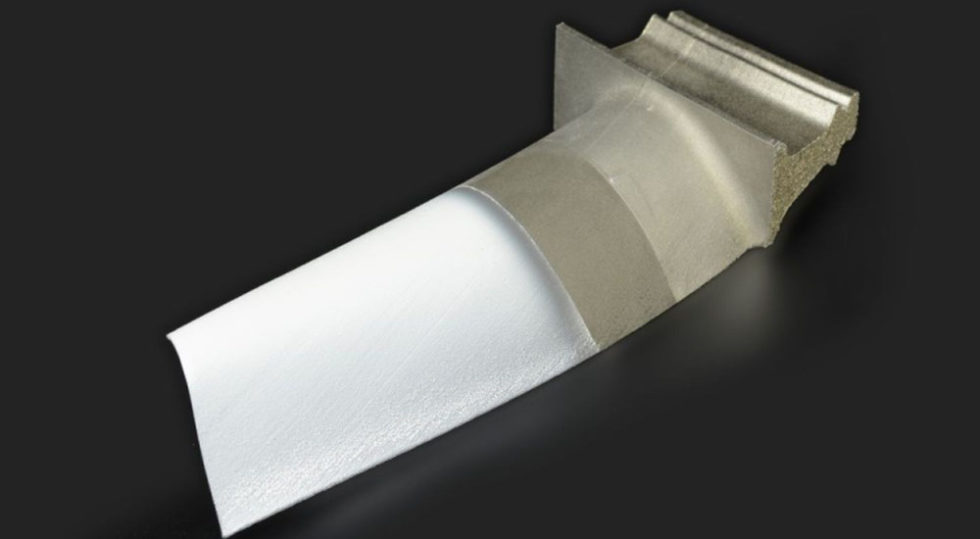
Die Beschichtung ist extrem dünn, schützt aber vor großer Hitze.
Foto: Fraunhofer IWS Dresden
Die Flugbranche boomt – gut für die Umwelt ist diese Entwicklung nicht. Umso mehr Aufmerksamkeit erfahren Entwicklungen, die das Fliegen effizienter gestalten könnten. Denn ein geringerer Kraftstoffverbrauch ist natürlich auch mit weniger Emissionen verbunden. Dazu möchte ein Team von Forschern des Fraunhofer-Instituts für Werkstoff- und Strahltechnik (IWS) in Dresden beitragen. Die Wissenschaftler haben eine neue Technologie entwickelt, um Bauteile zu beschichten. Sie soll nicht nur besonders günstig sein, sondern auch dazu führen, dass die Komponenten mehr Hitze vertragen, was eine höhere Temperatur der Turbinen ermöglichen würde und damit einen größeren Wirkungsgrad. Gemeinsam mit dem Schweizer Anlagenbauer AMT haben die Forscher das neue Verfahren in der Praxis getestet. Anwendungspotenzial sehen sie unter anderem in der Flugzeugindustrie, in der Luft- und Raumfahrt sowie in der Halbleiterbranche.
Suspension verhindert Verklumpungen des Pulvers
Bisher wurden in erster Linie 2 Methoden eingesetzt, um Wärmedämmschichten zu erzeugen: Auf der einen Seite gibt es die Möglichkeit, Bauteile mit Elektronenstrahlverdampfern in Vakuumkammern zu bearbeiten. Bei diesem thermischen Verdampfungsverfahren entstehen qualitativ hochwertige Schichten, die lange halten. Allerdings ist die Durchführung teuer, vor allem, wenn es sich um große Bauteile handelt. Auf der anderen Seite wird das atmosphärische Plasmaspritzen eingesetzt. Vereinfacht gesagt, wird dafür Pulver in einem Plasmastrahl geschmolzen und auf das Bauteil geschleudert. Die Anwendung ist zwar verhältnismäßig günstig, aber die so erzeugten Schutzschichten sind in der Regel nicht sehr langlebig.
Das Team vom Fraunhofer IWS hat nun ein neues Verfahren vorgestellt. Es nennt sich YSZ-Suspensionsspritzen. Dabei steht YSZ für ein feines Keramikpulver aus Yttrium-stabilisiertem Zirkoniumoxid. Die Körner darin sind extrem fein, mit einem Durchmesser von maximal 1 Mikrometer. Damit sie nicht verklumpen und die Schläuche der Maschinen verstopfen, werden sie mit Wasser oder Alkohol zu einer Suspension angerührt, also einer Flüssigkeit, in der Festkörper in äußerst feiner Verteilung vorkommen. So gelingt es den Wissenschaftlern, die Partikel in einem Spritzverfahren zu verwenden und dabei eine Schicht aufzutragen, die gerade einmal 500 Mikrometer dünn ist. Ein Vakuum ist nicht nötig, was die Kosten im Vergleich zum Elektronenstrahlverdampfen erheblich senkt. Auch das Verarbeitungstempo ist hoch.
Turbinen vertragen mehr Hitze
Für eine größere Effizienz der Flugzeuge sorgt der Schutzeffekt der Beschichtung in Bezug auf die Temperatur. Nach Angabe der Wissenschaftler führt ihr Verfahren dazu, dass eine entsprechend beschichtete Turbine eine um etwa 150 Grad höhere Betriebstemperatur verträgt. Das verbessere den Wirkungsgrad und reduziere parallel den Kühlaufwand. Im Ergebnis sinke der Kraftstoffverbrauch. „Auch die Umwelt wird weniger belastet, weil der Treibstoff in den verbesserten Triebwerken effizienter verbrennt, was den Kraftstoffverbrauch zusätzlich reduziert und entsprechend weniger Schadstoffe ausstößt“, sagt Forschungsleiterin Maria Barbosa.
Das Verfahren des YSZ-Suspensionsspritzens lässt sich natürlich auch mit alternativen Pulvermischungen durchführen. Die Fraunhofer-Wissenschaftler haben daher schon das nächste Ziel vor Augen. Gemeinsam mit dem Deutschen Zentrum für Luft- und Raumfahrt und der TU Dresden wollen sie eine hochwertige Schutzschicht entwickeln, die Turbinen von Flugzeugen in einer ganz besonderen Situation vor gefährlichen Schäden bewahren soll: Wenn es durch einen Vulkanausbruch wie im Jahr 2010 auf Island zu einer Ansammlung von Asche und Sand in der Luft kommt. „Wir wollen gemeinsam eine ,Opferschicht’ entwickeln, damit Asche und Sand nicht gleich die Turbinenschaufel selbst angreifen können. Die Flugzeuge sollen dadurch auch nach einem Vulkanausbruch noch sicher ihr Ziel erreichen“, sagt Barbosa.
Maschinen vor Korrosion schützen
Einen weiteren Anwendungsbereich sehen die Forscher in der Halbleiterbranche. Bislang setzen Mikroelektronikhersteller für die Chipproduktion unter anderem Plasma-Ätzkammern ein, in denen aggressive Fluorverbindungen die Kammerwände angreifen. Die Dresdner Wissenschaftler wollen ihr neues Verfahren daher dafür nutzen, mit einer entsprechenden Beschichtung das Innere der Maschinen besser vor Korrosion zu bewahren.
Weitere Beiträge zum Thema Flugzeugbau:
Ein Beitrag von: