Rolls-Royce liefert innovative Technik für moderne Triebwerke
Ein Schlüssel zu immer leistungsfähigeren und spritsparenderen Flugzeugen sind die Triebwerke. Unternehmen aus Deutschland liefern zentrale Teile für diese Triebwerke. Bei Rolls-Royce in Oberursel werden komplexe Blisks und Verdichtertrommeln hergestellt – auch für die Triebwerke der geplanten A350 von Airbus, die ab Mitte 2014 ausgeliefert werden soll.
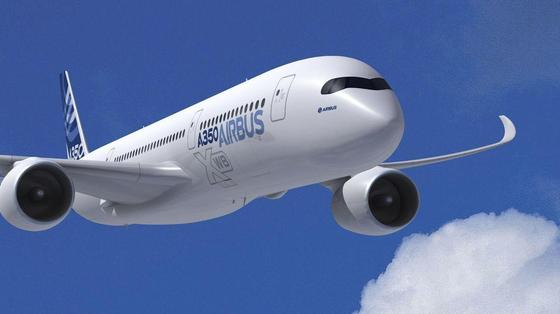
Airbus A350: Weitere Effizienzsteigerung durch neue Triebwerke.
Foto: Airbus
„Das ist ein wichtiges Element unseres Zukunftsgeschäfts.“ Gregor Kappmeyer, Spezialist für Zerspanungstechnik bei Rolls-Royce Deutschland, zeigt vorsichtig auf eine Hochdruck-Verdichtertrommel. Das Bauteil besteht aus drei miteinander verschweißten Scheiben mit integrierten Triebwerksschaufeln, in der Mitte läuft später die Triebwerkswelle. Solche Hochdruck-Verdichtertrommeln werden in naher Zukunft auch in den Triebwerken der neuen A350 von Airbus arbeiten.
Das Besondere an diesen Trommeln sind die Schaufeln: Sie sind nicht, wie es im Triebwerksbau lange die Regel war und teilweise auch noch ist, in die Scheibe eingesetzt und damit auswechselbar, sondern Schaufeln und Scheibe sind aus einem Stück gefertigt.
Blisks verbessern Aerodynamik und Effizienz der Triebwerke
Diese Blisks (Blade Integrated Disks), sind ein neuer Schritt in der Triebwerksentwicklung: Sie machen die Kombination Schaufel/Scheibe nicht nur um bis zu 30 % leichter, sie verbessern, so Kappmeyer, auch die Aerodynamik an den Verdichterschaufeln und erhöhen so zusätzlich die Leistungsfähigkeit des gesamten Triebwerks.
Weltweit arbeiten alle großen Triebwerkshersteller an innovativen Technologien, um ihre Triebwerke leichter und effizienter zu machen und den Treibstoffverbrauch weiter zu senken.
Ein Triebwerk hat mehrere Elemente. Der große Fan ist Teil des Niederdruckverdichters, es folgen der Hochdruckverdichter, die Brennkammer, die Hochdruckturbine und die Niederdruckturbine. Alle Komponenten des Triebwerks sind Gegenstand intensiver Forschung und Entwicklung. Dabei geht es um neue Geometrien, neue Herstellungsverfahren, Effizienzsteigerungen und neue Materialien. Ziel ist immer, die Leistungsfähigkeit der Triebwerke zu erhöhen – über die letzten Jahre gerechnet, sank der Spritverbrauch neuer Triebwerke um ca. 1 % pro Jahr.
Die Blisks im Bereich des Hochdruckverdichters gelten in diesem Rennen um sparsame Triebwerke als eine wichtige Etappe. Und innerhalb Rolls-Royce ist der Standort Oberursel mit seinen 1200 Mitarbeitern das Kompetenzzentrum für die Fertigung von Blisks und Hochdruckverdichtertrommeln.
Der Hochdruckverdichter besteht aus mehreren hintereinander angeordneten Scheiben mit Schaufeln, die die Luft ansaugen und verdichten, bevor sie in die Brennkammer gelangt. Aber Blisks im Hochdruckverdichter, auf denen bis zu 80 Schaufeln sitzen, sind ein komplexes und teures Produkt, dessen Fertigungsprozess permanent optimiert wird.
Neben den Blisks werden im Rolls-Royce Werk in Oberursel aber auch klassische Verdichtertrommeln gefertigt, in die die Schaufeln montiert werden, etwa für die A320 von Airbus. Erste Blisks aus Titan liefert das Oberurseler Werk für kleinere Triebwerke und die Verdichtertrommeln des militärischen Airbus A400M.
Rolls-Royce verzeichnet steigende Nachfrage nach Verdichtertrommeln
Gut 60 Verdichtertrommeln mit und ohne Blisks verlassen pro Woche das Werk. Und die Nachfrage steigt. „Wir haben die Auslastung des Werks in den letzten Jahren um gut 40 % gesteigert“, so Holger Cartsburg, Director Operations in Oberursel.
Doch die Zukunft gehört vor allem Triebwerken wie dem Trent XWB, dem Triebwerk für die A350. An die 550 Bestellungen für das Flugzeug liegen vor, 1200 für die Triebwerke. In der 2. Hälfte 2014 soll das Flugzeug ausgeliefert werden.
Das Werk in Oberursel ist derzeit der einzige Lieferant der Blisk-Hochdruck-Verdichtertrommel für das Trent XWB. Die ersten 15 Verdichtertrommeln für Test-Triebwerke haben das Werk bereits verlassen. Im Gegensatz zu den Titanblisks für die A400M-Triebwerke sind die Blisks für das Trent XWB aus einer Nickelbasis-Legierung gefertigt.
Die Rohlinge für die Bliskfertigung bezieht Rolls-Royce von Zulieferern. Die gesamte Fertigungskette von der Zerspanung über die Vorrichtungssysteme bis zur Messtechnologie hat Rolls-Royce in Oberursel entwickelt und zur Serienreife gebracht. Die fertigen Blisks werden in einer Elektronenstrahl-Schweißanlage zu Verdichtertrommeln zusammengeschweißt. Geplant ist zudem, so Cartsburg, auch neue, verbesserte Versionen bereits existierender Triebwerkstypen mit Blisks im Hochdruckverdichter auszustatten.
Ein Vorteil der klassischen Schaufeln war, dass sie nur eingehängt und so im Reparaturfall einfach auszuwechseln waren. Bei den Blisks geht das nicht mehr. Repariert werden sie deshalb – insbesondere bei Beschädigungen der vorderen und oberen Schaufelkanten – mittels Laserauftragschweißen. Bei größeren Schäden, so Cartsburg, ließe sich so „auch eine ganze Schaufel wieder neu aufbauen“. Da stelle sich allerdings die Frage, „ob das wirtschaftlich Sinn macht“. Eine Blisk kann auch aus der Trommel herausgelöst und durch eine neue ersetzt werden.
Blisks-Fertigung: Bei Rolls-Royce noch viel Handarbeit
Die Fertigung der Blisks, ihre Zusammensetzung zu Verdichtertrommeln und die Reparaturprozesse machen noch immer eine Menge Handarbeit notwendig, so etwa beim Ausrichten der Blisks, bevor sie in die Elektronenstrahl-Schweißanlage kommen. Dabei tragen die Mitarbeiter einiges an Verantwortung: Eine Blisk für einen Hochdruckverdichter der Trent XWB-Triebwerke kostet ungefähr so viel wie zwei bessere Mittelklassewagen.
„Wir arbeiten deshalb permanent daran“, so Kappmeyer, „diesen Prozess weiter zu automatisieren und damit auch die Kosten zu reduzieren“ – zumal im kommenden Jahr der Hochlauf der Bliskfertigung für die A350 beginnt.
In der aktuellen Diskussion um die Triebwerke der Zukunft sehen Cartsburg und Kappmeyer den Oberurseler Standort gut positioniert: „Ob die kommenden Triebwerke Open-Rotor-Triebwerke sind oder einen Getriebefan haben, einen leistungsfähigen Hochdruckverdichter brauchen sie immer“, so Cartsburg. „Die Zukunft“, ergänzt Kappmeyer, „geht ganz klar in Richtung Integralbauteile wie die Blisks. Die große Herausforderung wird sein, wie wir in diesen Bauteilen immer leistungsfähigere Materialien miteinander kombinieren können.“
Ein Beitrag von: