Schub für E-Mobilität dank Leichtbau?
Elektromobilität gilt als Antrieb der Zukunft. Damit die Fahrzeuge mehr Reichweite schaffen, müssen sie möglichst leicht sein. Das könnte mit dem Einsatz kohlenstofffaserverstärkter Kunststoffe (CFK) gelingen.
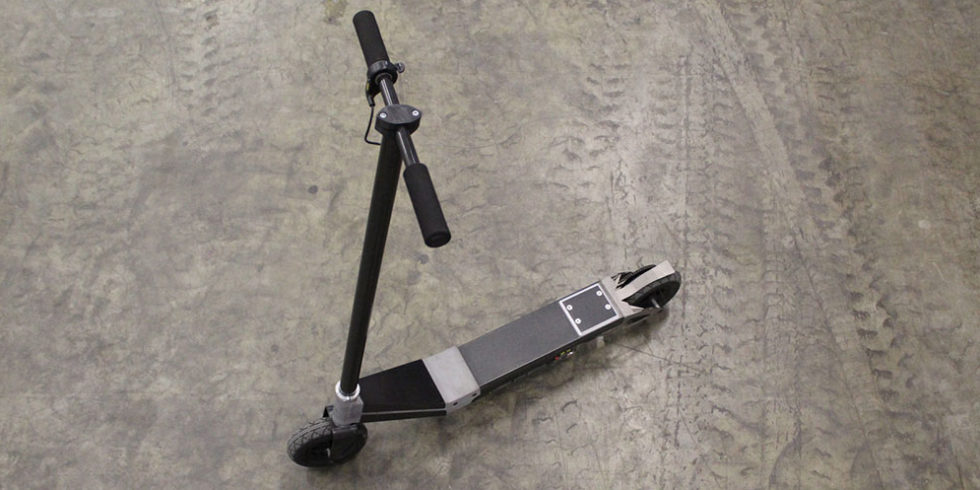
E-Roller in Leichtbauweise aus hybridisierten Metall- und CFK-Bauteilen.
Foto: Fraunhofer IGCV
Busse, Autos, Roller, Fahrräder – sie alle gibt es mit Elektroantrieb. Ihr Manko: die mangelnde Reichweite. Und das liegt hauptsächlich am Gewicht. Da beides zusammenhängt, arbeitet die Forschung daran, möglichst leichte Teile zu entwickeln, die mit den funktionstragenden Metallteilen in den Fahrzeugen verbunden werden können. Denn weniger Gewicht bedeutet, dass das Fahrzeug mit der gespeicherten Energie länger auskommt. Forscher der Fraunhofer-Einrichtung für Gießerei-, Composite- und Verarbeitungstechnik IGCV am Technologiezentrum in Augsburg haben sich deshalb mit kohlenstofffaserverstärkten Kunststoffen (CFK) beschäftigt.
CFK ist ähnlich stabil wie Stahl, dafür aber etwa achtmal leichter und sogar dreimal leichter als Aluminium. Aktuell werden in der Automobilbranche nur einzelne Komponenten aus diesem Rohstoff gefertigt, zum Beispiel Fahrzeugrahmen. Die Teile verbinden Monteure dann über Schrauben oder Klebstoffe mit den sogenannten funktionstragenden Bauteilen aus Metall. Das bedeutet: Teile, die lange Strecken verbinden und Lasten übertragen, können durchaus aus CFK produziert werden. Dagegen bestehen die Funktionsbauteile wie das Lenkrad weiterhin aus Metall.
Drei Bauteile des E-Rollers neu entwickelt
Der Fraunhofer-Forschergruppe ist es gelungen, herkömmliche Gießtechnik-Bauteile mit Komponenten aus CFK zu verbinden. Dabei geholfen haben ihnen moderne Fertigungsverfahren wie die additive Fertigung und der 3D-Druck. Getestet haben sie es in einem Elektro-Roller, in dem sie verschiedene Verbindungsansätze zusammenführten. „Wir wollen die mechanischen Anbindungspunkte reduzieren und die Prozessschritte beim Anbinden minimieren“, erläutert Daniel Günther, zuständiger Projektleiter am Fraunhofer IGCV. Die Forscher schätzen das Potenzial der Kombination von Metall und CFK als extrem hoch ein: „Je nach Bauteil lassen sich bis zu 50 % Gewicht einsparen“, so Günther. An drei verschiedenen Bauteilen eines E-Rollers haben die Forscher ihre Ideen getestet: am Hinterradträger, am Lenkkopf und an der Gabel.
Um den Hinterradträger zu modifizieren, betrachteten sie Lage und Anordnung der einzelnen Teile. Grundsätzlich ist der Hinterradträger ein Bauteil mit hoher Funktionsdichte und wird aus Metall gebaut. Die Forschergruppe fertigt ihn aus hochfestem Stahl und optimiert ihn so, dass nur an den Stellen Material eingesetzt wird, wo es die Funktion erfordert. Sie nutzen dafür die additive Fertigungstechnik, bei der Bauteile durch Bestrahlung mit einem Laser aus Metallpulver hergestellt werden. Anschließend verschrauben sie ihn mit dem Trittbrett aus CFK. Neben dem geringeren Gewicht hat diese Bauweise den Vorteil, dass sich der Hinterradträger leichter zerlegen und warten lässt.
Forscher entschieden sich für geklebten Lenkkopf
Der Lenkkopf des Rollers verbindet Trittbrett mit Lenkstange. Das bedeutet, er überbrückt einen größeren Raum und ist deshalb ein wichtiges funktionales Teil, das besonders steif sein muss in seinen Materialeigenschaften. Der Lenkkopf besteht im Grunde aus Aluminium-Sandguss und ist ein Hybridbauteil. Die nötige Steifigkeit bringt das CFK mit. Mittels einer Klebtechnik verbinden die Forscher beide Materialarten miteinander. „Als Belastungsgrundlage sind wir von einer hundert Kilogramm schweren Person ausgegangen, die mit dem Roller springt. Mit einem reinen Aluminium-Gussteil würde man hier sehr viel mehr Material verbauen müssen, um die notwendige Steifigkeit hinzubekommen“, erklärt Ingenieur Daniel Günther.
Deshalb analysierten die Forscher, welcher Bauraum zur Verfügung steht. Ihnen ging es darum, die Biegesteifigkeit zu optimieren. Sie hängt von der Absenkung eines biegebeanspruchten Bauteils bei gegebener Last ab. Eine höhere Biegesteifigkeit lässt sich erreichen, je größer der Querschnitt des Bauteils ist. Gleichzeitig mussten die Forscher an diesen Stellen sehr dünnes Material einsetzen, damit die Komponente insgesamt nicht zu schwer wird. Gelöst haben sie das durch die Kombination von CFK mit Guss. Um alle Materialien miteinander zu verbinden, entschieden sie sich für Klebestellen. Diese setzten sie an die Stellen, die wenig belastet werden.
Unkompliziertes Verfahren und auf große Serien übertragbar
Der Werkstoff CFK ist extrem belastbar und fest. Das liegt an seinen Fasern. Damit CFK sinnvoll eingesetzt wird, ist es wichtig, die Kraft, die auf das entsprechende Bauteil wirkt, in diese Fasern zu übertragen. Folglich müssen alle Metallteile sehr gut mit denen aus CFK verbunden sein. Es dürfen keine Spalten oder gar Hohlräume dabei entstehen. Gelungen ist den Forschern dies an der Gabel des E-Rollers dank eines Vakuums und hohen Temperaturen.
Die Gabel wird mit dem Lenker verbunden. Das Verbindungsstück ist zylindrisch geformt und aus Stahl. Unten besteht es aus einer Platte mit kleinen Pins, die herausstehen und dann die waagerechten Bretter halten – ähnlich wie bei einem Regal. Die Forscher legten über diese Fuß-Platte Ausgangsplatten für die CFK, die aus mit Kunstharz ummantelten Fasern bestehen. Nun sorgen das Vakuum und die erhöhte Temperatur dafür, dass das Harz zuerst um die Kohlenstofffasern fließt und anschließend der Schwerkraft folgend nach unten Richtung Fuß-Platte. Es schließt damit die Lücke zur Metallplatte und härtet wie ein Kleber aus. Ohne Schrauben ist es den Forschern mit dieser Methode gelungen, die Bauteile formschlüssig und fest miteinander zu verbinden. „Das Verfahren lässt sich unkompliziert auf große Serien übertragen, ist schnell und industrietauglich“, sagt Günther.
Auf der Hannover Messe kann man sich über diese Verbindungstechniken informieren. Die Forschergruppe präsentiert ihren E-Roller vom in Halle 17 an Stand C24. Eine Probefahrt ist möglich.
Weiterführende Links:
Ein Beitrag von: