Skalierbarer Elektroantrieb für Trucks und Rennwagen
Mit einem Baukastensystem wollen Fraunhofer-Forscher den Bau von Elektrofahrzeugen beschleunigen. Sie haben eine Achse mit integriertem Elektromotor entwickelt, die sich in verschiedenen Größen herstellen lässt. So kann sie einen Rennwagen genauso antreiben wie einen Elektro-Bus.
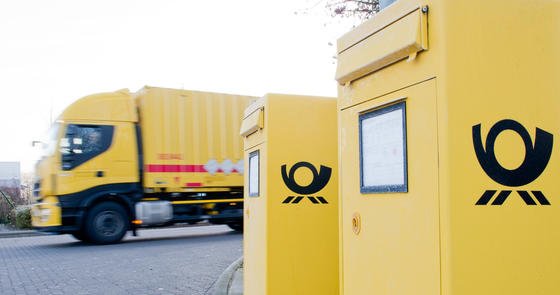
Lkw und Briefkästen der Deutschen Post: Die Post testet in Bonn in einem Großversuch Lkw mit Elektroantrieb. Jetzt haben Forscher in Chemnitz einen Elektroantrieb entwickelt, der die Kosten für E-Laster stark senken soll.
Foto: Julian Stratenschulte/dpa
Elektrisch betriebenen Lastwagen könnte die Zukunft gehören. Viele Städte bemühen sich verzweifelt, die Grenzwerte für Feinstaubemissionen einzuhalten, an denen Diesel-Lkw einen erheblichen Anteil haben. Außerdem soll der Lärm gemindert werden.
Doch Elektrotransporter sind sehr viel teurer als dieselbetriebene, was nicht nur an den Batterien oder Brennstoffzellen liegt, die die Motoren mit Strom versorgen. Wichtige Komponenten lassen sich noch nicht in Serie und damit kostensparend herstellen.
Prototyp soll noch in diesem Jahr fertig werden
Das soll sich jetzt ändern. Wissenschaftler aus elf Institutionen haben unter Führung des Fraunhofer-Instituts für Werkzeugmaschinen und Umformtechnik (IWU) in Chemnitz eine Achse entwickelt, die alles enthält, was für den Antrieb nötig ist: Motor, Getriebe, Leistungselektronik, mit der die Drehzahl geregelt wird, und die Bremsanlagen. Das kompakte Bauteil lässt sich in drei Größen herstellen: für Leichttransporter, schwere Lkw und sogar für Rennwagen. Im Laufe dieses Jahres wollen die IWU-Wissenschaftler einen Prototypen mit einer solchen Achse ausstatten.
Das System eines zentralen Elektromotors halten die Chemnitzer Forscher gegenüber den Radnabenantrieben für überlegen. „Das Modul ist skalierbar, wir können es sowohl bei einem kleinen Transporter oder Kommunalfahrzeug einsetzen als auch bei einem Bus oder Truck«, sagt Hans Bräunlich, Projektleiter am IWU. Bei einem Radnabenmotor wäre das nicht möglich. „Zwar bietet dieser durchaus Vorteile – etwa einen größeren Lenkungswinkel und direkteres Ansprechverhalten – allerdings eignet er sich nicht für Nutzfahrzeuge: Denn er leistet kaum mehr als 2000 Umdrehungen pro Minute.“
Außerdem seien die Kosten höher, da für jedes Rad eine eigene Leistungselektronik erforderlich ist, so Bäumer. „Beide entwickelten Varianten haben durchaus ihre Daseinsberechtigung und müssen zielgerichtet für den geplanten Fahrzeugtyp ausgewählt werden.“
Große Kräfte statt Fräsen und Bohren
Der eingesetzte Motor schafft bis zu 20.000 Umdrehungen pro Minute, was auch Rennwagen zugute käme. „Als wir vor drei Jahren mit dem Projekt begannen, waren wir die einzigen, die eine so hohe Drehzahl erreichen konnten“, erinnert sich Bräunlich. Mittlerweile arbeiteten auch andere Forscherteams mit solchen flott drehenden Motoren. Doch Bräunlich glaubt, einen entwicklungstechnischen Vorsprung zu haben, „den wir weiter ausbauen wollen“. Die hohe Umdrehungsrate sorgt, in Verbindung mit dem Getriebe, für eine starke Beschleunigung.
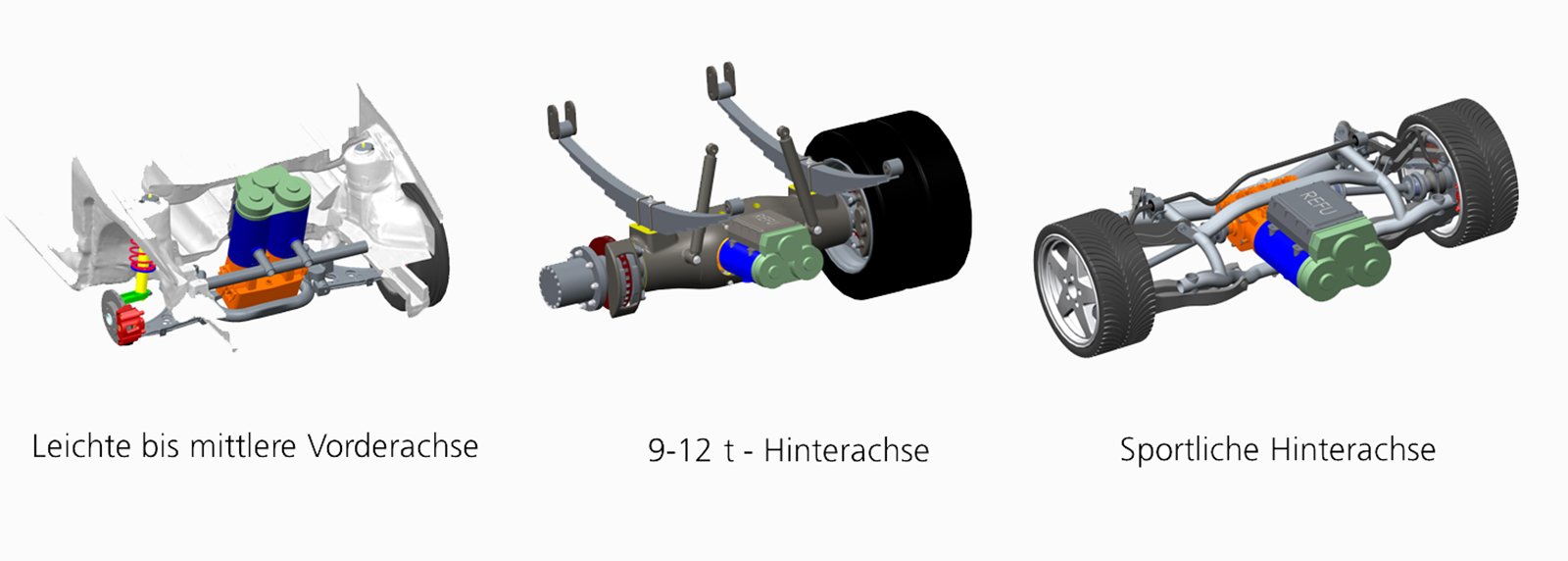
In elektrisch angetriebenen Nutzfahrzeugen der Zukunft ist der Antrieb in die Achse integriert, glauben die Forscher des Fraunhofer-Instituts in Chemnitz. Sie haben einen Antrieb entwickelt, der skalierbar ist je nach Fahrzeuggröße.
Quelle: Fraunhofer IWU / Hochschule für Wirtschaft und Technik, Aalen
Die Chemnitzer Forscher haben einen ganz speziellen Zusatzbeitrag zu dem Projekt geleistet. Sie entwickelten, gemäß der Institutsbezeichnung, Kosten sparende Techniken zur Herstellung einzelner Komponenten. Zahnräder fürs Getriebe, die üblicherweise aus Stahlblöcken herausgefräst werden, sodass sehr viel Abfall entsteht, stellen sie mit einer neuen Technik her, die das gesamte Material nutzt. Beim so genannten Verzahnungsfräsen wird eine Stahlscheibe von gegenläufigen Werkzeugen, auf denen Negativ-Abbilder der gewünschten Zähne sitzen, mit großen Kräften bearbeitet. Nach und nach überträgt sich das Zahnmuster auf die Stahlscheibe.
Ähnlich Material sparend stellen sie Wellen her, auf denen die Zahnräder sitzen. Normalerweise werden sie durch Bohren aus Stahlstangen hergestellt. Auch hier ist die Abfallmenge groß. Die Chemnitzer nehmen eine kurze Stahlstange und treiben einen Dorn ein, der einen inneren Hohlraum schafft. Das herausgedrückte Material verlängert das Rohr. Eine stabile Hülle sorgt dafür, dass die Außenwand glatt bleibt. All das geschieht bei Zimmertemperatur, verbraucht also keine zusätzliche Energie. Und die Materialkosten sinken um 30 Prozent, so Bräunlich.
Ein Beitrag von: