Statoil und Siemens entwickeln Fabriken zur Öl- und Gasförderung auf dem Meeresgrund
Nicht mehr Bohrinseln mit all ihren Gefahren, sondern Fabriken direkt auf dem Meeresgrund der Tiefsee sollen künftig Öl und Gas fördern. Daran arbeiten der norwegische Ölkonzern Statoil und der Siemenskonzern. Die Technik muss ungeheure Drucke über sehr lange Zeit aushalten. Derzeit laufen die Test im norwegischen Siemens-Labor.
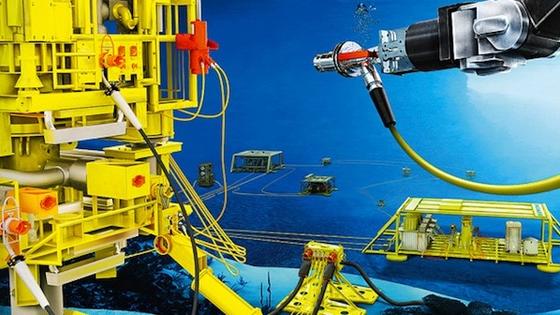
Ab 2020 will der norwegische Energiekonzern Statoil Öl und Gas mit einer autarken Unterwasserfabrik in der Tiefsee fördern.
Foto: Siemens
Der norwegische Energiekonzern Statoil will ab dem Jahr 2020 in einer Unterwasserfabrik auf dem Meeresboden völlig autark Öl und Gas fördern. In einer Tiefe von 3000 Metern oder mehr sollen diese Anlagen mit einer eigenen Stromversorgung arbeiten, die der Siemens-Konzern entwickelt.
Siemens-Ingenieure testen derzeit im norwegischen Labor in Trondheim sämtliche Teile der neuen Technik unter extremsten Bedingungen. Transformatoren und andere Netzkomponenten müssen langfristig einen Druck von bis zu 460 Bar aushalten können. Diesen Herausforderungen mussten sich bisher noch keine technischen Teile stellen. „Transformatoren, Frequenzumrichter und Schaltanlagen müssen in dieser Umgebung einwandfrei funktionieren und das über einen Zeitraum von 30 Jahren, weil sie dort unten schlecht gewartet werden können“, erklärt der norwegische Siemens-Ingenieur Jan Erik Lystad.
Bauteile müssen 460 Bar Druck aushalten
Die Bauteile werden in 19 Kammern aus Stahlbeton auf ihre Haltbarkeit getestet. Dabei werden die Behälter mit Öl gefüllt und einem Druck von 460 Bar ausgesetzt. Das Öl spielt eine wichtige Rolle für die neue Stromtechnik. Das gesamte Gehäuse soll später mit Öl gefüllt werden, bevor es auf den Meeresgrund abgelassen wird. Mit dem Öl wird Wärme abgeleitet, auf Kühlsysteme kann deshalb verzichtet werden kann.
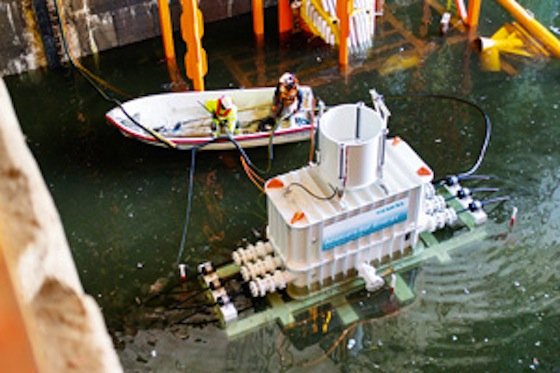
Den Flachwassertest hat der Transformator bereits absolviert. Demnächst stehen Test am Meeresboden auf dem Programm.
Quelle: Siemens
Ob die Bauteile auch nach 20 Jahren noch arbeiten oder verschleißen, wird in einem sogenannten Haltbarkeitstest untersucht. Dafür wird ein Alterungsprozess simuliert, in dem der Zylinder mit einer Heizschleife versehen wird. Diese beheizt das Bauteil dauerhaft mit 95 Grad Celsius. Nach der Testreihe werden die Komponenten genau auf Risse und Verformungen untersucht.
Tiefseetauglich sind die Komponenten erst, wenn keine Makel gefunden werden. „Es ist eine Herausforderung, Bauteile zu finden, die solche Extrembedingungen aushalten, denn kein Komponentenhersteller hat speziell für diese Tiefe ausgelegte Produkte“, so Lystad. „Wir betreten hier also ständig Neuland.“
Erster Tiefsee-Transformator im Trondheimer Hafenbecken getestet
Haben die Bauteile die Tests bestanden, werden sie zu einem Transformator zusammengesetzt und auf einen Träger verschraubt. Zinkplatten sollen das riesige Bauteil vor Korrosion schützen. Nachdem das Bauteil, das die Größe eines Containers hat, im Hafenbecken von Trondheim getestet wurde, soll noch dieses Jahr die Schaltanlage montiert werden.
Ziel der norwegischen Ingenieure ist es, bis Ende 2014 den Frequenzumrichter zu entwickeln. Dieser versorgt sämtliche Bauteile wie Ölpumpen und Gasverdichter mit Strom. Alleine der Frequenzumrichter wird ein Gewicht von 100 Tonnen haben. Nun werden Frequenzumrichter, Ölpumpen und Gasverdichter zu einem Netzwerk zusammengeschlossen. Es folgt der Finaltest: Erstmals kommen die Systeme auf den Meeresgrund.
Subsea-Anlagen sind bislang noch per Kabel mit Plattformen verbunden
Manche Bohrinseln arbeiten schon heute direkt auf dem Meeresboden. Sie sind jedoch nicht autark, sondern es besteht immer eine Verbindung zu einer Plattform, die die Anlage mit Energie versorgt. Dafür werden die auf dem Meeresboden liegenden Pumpen mit einer großen Anzahl an elektrischen Kabeln und Rohleitungen zur schwimmenden Plattform verbunden.
Diese sogenannten Subsea-Anlagen funktionieren nur in flachem Wasser. Die Verarbeitung der Rohstoffe erfolgt an der Oberfläche. Die Förderung ist sehr aufwändig und mit hohen Kosten verbunden. Aus diesem Grund werden Öl und Gas weiterhin auf klassischen Bohrinseln gefördert.
Ein Beitrag von: