Von Beginn an glatte Flächen: Automotoren halten länger
Das Einfahren von Neuwagen wird in Zukunft deutlich kürzer. Mit von Fraunhofer Forschern entwickelten Werkzeugen werden metallische Oberflächen extrem glatt und widerstandsfähig, so dass Reibung und Verschleiß von Motorkomponenten deutlich gesenkt werden kann.
.
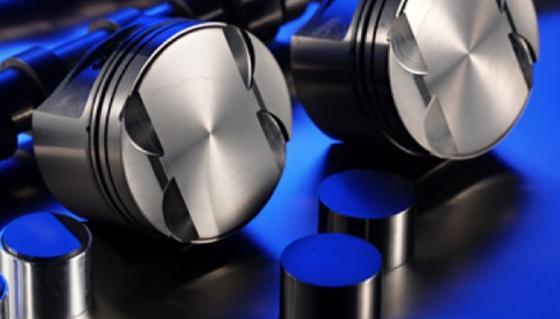
Funktionelle Beschichtung auf Motorkomponenten.
Foto: Fraunhofer IST
Der neue Wagen hat zwar reichlich PS, darf aber nur sanft beschleunigt werden. Und Vollgas auf der Autobahn ist auch nicht drin, noch nicht jedenfalls. Zunächst muss der Motor eingefahren werden. Was früher ein paar 1000 Kilometer brauchte, ist heute schon nach 500 bis 1000 Kilometern erreicht: Zwischen benachbarten Metallflächen hat sich eine Art Schutzschicht gebildet, die zuverlässig vor Reibung und damit Zerstörung schützt.
Diese lästige Prozedur wollen Forscher von gleich fünf Fraunhofer-Instituten im Gemeinschaftsprojekt TriboMan (Tribologie=Reibungstechnik) bereits in die Fertigung von Motorkomponenten vorverlegen. Hoher Reibung ausgesetzte Motorteile wie die Zylinderlaufflächen sollen schon bei der F
Für die Endbearbeitung von Zylinderlaufflächen haben die Forscher eine verbesserte Fertigungstechnologie entwickelt. Für das Präzisionsbohren kommen definierte Schneiden zum Einsatz, deren Geometrie spezifisch ausgelegt wurde. Dadurch kann eine sehr hohe Oberflächengüte erreicht werden. Zudem werden die Kräfte des Zerspanungsprozesses gezielt genutzt, um das Verfestigen der Werkstoffe bereits fertigungsbegleitend zu erreichen.
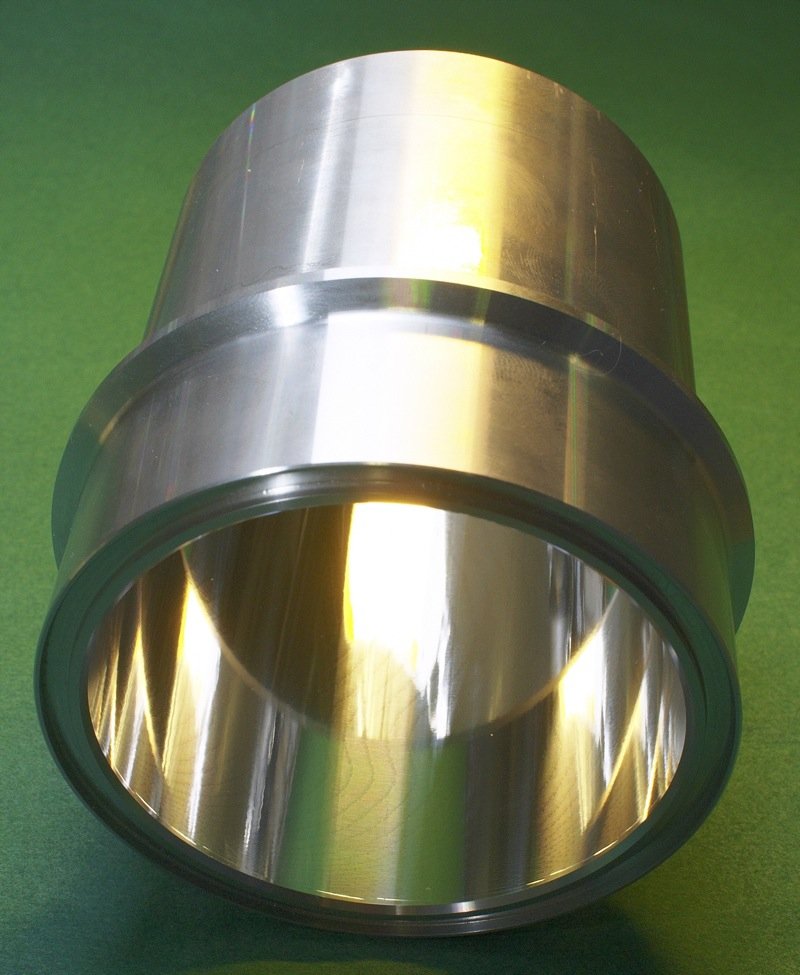
Für das Präzisionsbohren von Zylinderlaufflächen kommen definierte Schneiden zum Einsatz, deren Geometrie spezifisch ausgelegt wurde. Dadurch kann eine sehr hohe Oberflächengüte erreicht werden.
Quelle: Fraunhofer IWU
Zudem erreichen die Forscher, was sonst noch beim Einfahren geschieht. Durch Reibung und Wärmeentwicklung verdichtet sich die Struktur der Oberfläche bis in eine Tiefe von 500 bis 1000 Nanometer (ein Nanometer ist ein Millionstel Millimeter). Es entsteht eine nanokristalline Schicht. An den Schneidflächen der neuartigen Bohrer entstehen die gleichen Kräfte und vergleichbare Temperaturen, sodass die Schicht sich bereits fertigungsbegleitend ausbildet.
Der Spritverbrauch sinkt
Das hat zwei entscheidende Vorteile. Der Motor schluckt in der Anfangsphase nicht übermäßig viel Sprit, weil ja keine Reibung mehr zu überwinden ist. Und der Käufer kann keine Einfahrfehler machen, die die Lebensdauer des Aggregats entscheidend verkürzen können.
Dass es funktioniert haben Forscher des Fraunhofer-Instituts für Werkstoffmechanik in Freiburg schon bewiesen. In den Laufflächen eines Ein-Zylinder-Versuchsmotors, die mit den neuartigen Werkzeugen bearbeitet worden waren, entstand bereits während der Herstellung die gewünschte Nanostruktur.
Die Oberflächen-Mikrogeometrie sei mit der von gut eingelaufenen Zylinderlaufflächen vergleichbar, stellten die Forscher fest. Damit sind die Forscher ihrem Ziel ein ganzes Stück näher gerückt: „Unser gemeinsamer Ansatz ist es, den Prozess der Randschichtbildung in die Fertigung vorzuverlegen“, sagt Torsten Schmidt vom Fraunhofer-Institut für Werkzeugmaschinen und Umformtechnik in Chemnitz. Das scheint zu gelingen.
Ein Beitrag von: