Autos aus Erdölrückständen herstellen – diese verrückte Idee könnte funktionieren
Ein neues Verfahren macht aus Nebenprodukten der Erdöl-Raffinerie zu hochwertige, ultraleichte Strukturmaterialien Autos, Flugzeuge und Raumfahrzeuge. Der Bedarf an preisgünstigen Lösungen ist dringender denn je.
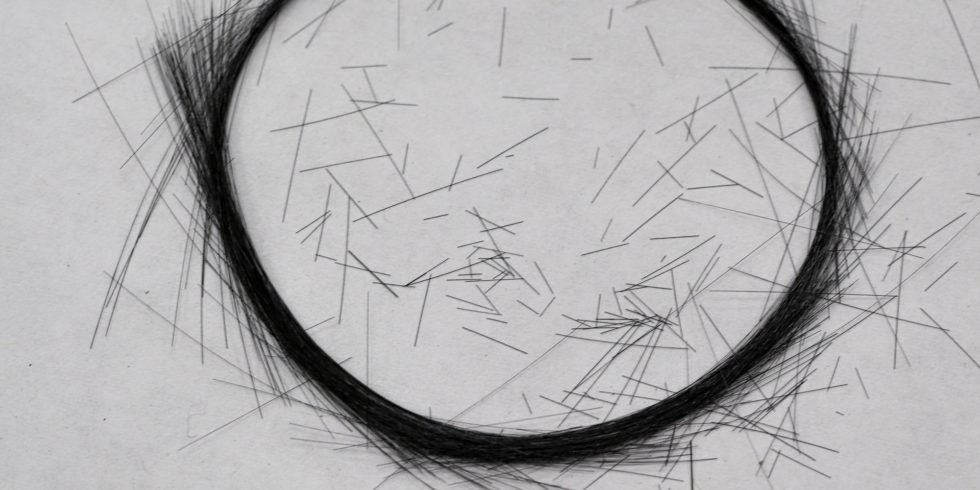
Aus Rückständen der Erdölverarbeitung lassen sich Kohlenstofffasern für Autos herstellen.
Foto: Nicola Ferralis/MIT
Die Rohölpreise explodieren. Gleichzeitig versuchen Firmen weltweit, den Ausstoß von Treibhausgasen zu verringern und die Reichweite von Elektrofahrzeugen zu maximieren. Hersteller machen sich deshalb auf die Suche nach immer leichteren Materialien, die stabil genug sind, um für die Karosserien von Autos eingesetzt zu werden.
Leichte Materialien aus Kohlenstofffasern oder Carbonfasern gelten als große Hoffnungsträger, sind in der Herstellung aber teurer als vergleichbare Strukturelemente aus Stahl oder Aluminium. Nun haben Forscher einen Weg gefunden, diese leichten Fasern aus extrem preisgünstigen Ausgangsmaterialien herzustellen: aus Rückständen der Erdöl-Verarbeitung, die momentan nur für Asphalt verwendet oder entsorgt werden. Ihre neue Kohlenstofffaser hat auch Vorteile gegenüber herkömmlichen Fasern, da sie eine höhere Druckfestigkeit aufweist. Sie eignet sich deshalb sogar für tragende Anwendungen.
Erstaunliche Eigenschaften: Endlich nachhaltiger Kunststoff in Sicht
Die Herausforderungen: Autos werden immer schwerer
Die Forschungsarbeiten begannen vor etwa vier Jahren als Reaktion auf eine Anfrage des US-Energieministeriums, das nach Möglichkeiten gesucht hat, um Autos effizienter zu machen und um den Kraftstoffverbrauch durch ein geringeres Gesamtgewicht zu senken. „Wenn man sich ein Automodell heute ansieht, ist es im Vergleich zu dem gleichen Modell vor 30 Jahren deutlich schwerer“, sagt Nicola Ferralis. Er forscht am Department of Materials Science and Engineering des Massachusetts Institute of Technology (MIT) in Cambridge.
Ein schwereres Auto braucht beispielsweise einen größeren Motor und stärkere Bremsen. Verringert man das Gewicht der Karosserie oder anderer Komponenten, sind Einsparungen an anderer Stelle möglich. Am MIT versuchen Wissenschaftlerinnen und Wissenschaftler deshalb, Leichtbau-Werkstoffe mit der Sicherheit normaler Stahlbleche zu entwickeln, die preisgünstig genug für Serienproduktionen sind.
Verbundwerkstoffe aus Kohlenstofffasern wurden aus Kostengründen in der Automobilbranche nur bei sehr teuren Modellen eingesetzt. Solche Fasern werden in der Regel aus Polymeren wie Polyacrylnitril hergestellt. Grundlage ist Erdöl. „Die Kosten für das Polymer können mehr als 60% der Gesamtkosten der fertigen Faser ausmachen“, sagt Ferralis.
Werkstofftechnik der Zukunft: Leistungsfähige Kunststoffe aus der digitalen Werkstofffabrik
Vom Abfallprodukt aus Erdölraffinerien zu Fasern für Autos
Anstatt ein raffiniertes und verarbeitetes Erdölprodukt zu verwenden, nutzt das MIT-Team bei seinem neuen Ansatz Rückstände aus der Destillation von Erdöl. Die pechartige Masse, bekannt als Bitumen, besteht aus unterschiedlichen langkettigen Kohlenwasserstoffen. Sie ist preisgünstig – und steht in großen Mengen zur Verfügung. Ähnliche Eigenschaften hat Steinkohlenpech. Es bildet sich bei der Verkokung von Steinkohle.
In Zusammenarbeit mit Forschern des Oak Ridge National Laboratory, die über Fachwissen zur Herstellung von Kohlenstofffasern unter verschiedenen Bedingungen verfügen, vom Labormaßstab bis hin zum Maßstab einer Pilotanlage, suchten MIT-Ingenieurinnen und -Ingenieure nach geeigneten Reaktionsbedingungen. Durch sorgfältige Modellierung der Art und Weise, wie sich Bindungen zwischen den einzelnen Molekülen bilden und vernetzen, konnten die Forschenden vorhersagen, wie sich bestimmte Verarbeitungsbedingungen auf die resultierenden Fasereigenschaften auswirken würden. „Wir waren in der Lage, unsere Ergebnisse mit einer verblüffenden Genauigkeit zu reproduzieren“, berichtet Asmita Jana vom MIT.
Durch die Anpassung der Ausgangsbedingungen gelang es, Kohlenstofffasern herzustellen, die nicht nur zugfest sind, wie die meisten dieser Fasern, sondern auch druckfest, was bedeutet, dass sie potenziell in tragenden Anwendungen eingesetzt werden könnten. Dies eröffne völlig neue Möglichkeiten für den Nutzen dieser Materialien, so Jana weiter.
Vom Labor nicht nur ins Auto: Viele Einsatzmöglichkeiten der Faser
Die ursprüngliche Aufforderung des US-Energieministeriums zielte darauf ab, Kosten für Leichtbaumaterialien auf unter zehn US-Dollar (rund neun Euro) pro Kilogramm Material zu drücken, um in breitem Umfang bei der Fertigung von Autos eingesetzt zu werden. Das MIT-Team schätzt, dass seine Methode noch besser abschneiden könnte – und dass sich die Kosten bei etwa sechs US-Dollar (rund 5,40 Euro) bewegen werden.
Die Forschenden sehen aber nicht nur Einsatzmöglichkeiten in der Autoindustrie. Bislang steht dem Einsatz herkömmlicher Faserverbundwerkstoffe im Wege, dass die Fasern zu einem Gewebe verarbeitet und in präzisen, detaillierten Mustern ausgelegt werden müssen. Nicht immer lohnt sich dieser Aufwand. Neue Materialien könnten durch ihre Druckfestigkeit nicht nur in Autos, sondern auch in anderen Bereichen zum Einsatz kommen.
Mehr zum Thema Innovationen der Automobilindustrie:
Ein Beitrag von: