CFK: Hohe Kosten blockieren Durchbruch am Massenmarkt
Kohlenstofffaserverstärkte Kunststoffe (CFK) haben als Leichtbauwerkstoff nicht nur für Hightech-Anwendungsnischen viel zu bieten, auch die Kfz-Industrie kann durch Carbonfasereinsatz die Ressourceneffizienz ihrer Produkte erheblich steigern. Doch der Durchbruch der leichten Verstärkungsfaser im Massenmarkt wird noch von zu hohen Kosten blockiert.
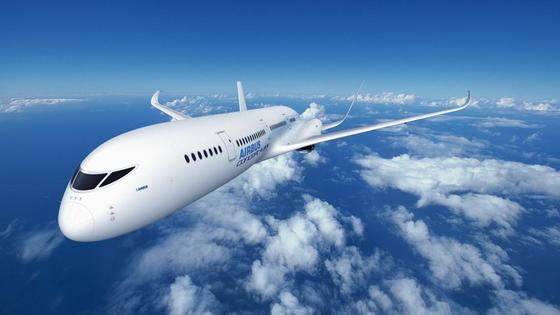
CFK: In der Luftfahrt als Verstärkungsfaser schon lange bewährt.
Foto: Airbus
In der Luftfahrt und im Rennsport bewährt sich die Kohlenstofffaser (Carbonfaser) als Verstärkungsfaser in leichten Verbundwerkstoffen schon seit Langem. Trotzdem steht ihr größtes Zukunftspotenzial noch bevor. Aber wahrscheinlich gar nicht mal im Flugzeugbau, wie etwa der Dreamliner von Boeing mit seinem hohen CFK-Anteil (Kohlenstofffaserverstärkter Kunststoff) vermuten lassen könnte, sondern in der Automobil- und der Windenergiebranche. Denn deren Märkte versprechen erheblich größere Abnahmemengen.
Doch bevor die Faser in diesen Volumenmärkten ankommt, muss noch einiges passieren, denn aktuell kosten auf Basis von Carbonfasern verarbeitete Komponenten etwa 100 €/kg – für Kfz-Hersteller lohnen sie sich aber nur bei einem deutlich niedrigeren Preis bis zu rund 30 €/kg.
CFK: Unternehmen und Forschung arbeiten an effizienteren Verfahren
„Der Einsatz in der Automobilindustrie erfordert völlig neue Herstellerwege, die eine geeignete Produktivität und Qualitätssicherung zu deutlich geringeren Kosten ermöglichen müssen“, erklärt Bernd Wohlmann, Entwicklungsleiter bei Toho Tenax Europe, Wuppertal, einem der weltweit großen Carbonfaserhersteller. Zur Steigerung der Effizienz arbeiten Unternehmen und Forschungsinstitute fieberhaft an neuen Verfahren und Lösungen für einen schonenderen Umgang mit den Ressourcen – ergänzt durch hochwertige Recyclingverfahren.
Vom Rohstoff bis zum fertigen Carbonfaserteil führen drei große Produktionsschritte: Herstellung des Vormaterials, der Carbonfasern selbst und der Fertigteile. „Jeder einzelne Schritt kann dazu beitragen, die Kosten-, Ressourcen- und Energiepotenziale zu heben“, sagt Kersten Christoph Link, Technischer Vorstand der Eisenmann AG, Böblingen. Der Systemanbieter im Anlagenbau hat sich unter anderem auf Produktionsanlagen für Carbonfasern spezialisiert.
Als Rohstoffquelle für das Vormaterial verwenden die Hersteller noch Erdöl, das sie meistens in Polyacrylnitril (PAN) umwandeln. Uwe Kobs, Direktor Geschäftsanalyse und strategische Planung bei SGL Carbon, Wiesbaden, einem führendem Hersteller für Carbonfaserprodukte, sieht in nachwachsenden Rohstoffen momentan keine Alternative. Allerdings sei deren Erforschung langfristig ein erfolgversprechender Prozess. Denn damit Carbonfasern die Volumenmärkte bedienen können, müssten die Hersteller vom Erdöl wegkommen.
Carbonfaser aus Lignin wird weltweit erforscht
„Weltweit arbeiten eine Handvoll Forschergruppen an der Herstellung von Carbonfasern aus Lignin“, so Wohlmann. Doch während die Umwandlung des hoch orientierten Vormaterials PAN zu einem stetigen Aufbau molekularer Ordnung führe, erfülle Lignin diese Voraussetzungen noch nicht. Allerdings ließe sich dieses Seitenprodukt der Zellstoffherstellung reinigen, schmelzen, verspinnen, thermisch stabilisieren und auch karbonisieren. Da diese Prozesse jedoch nicht zu stark orientierten Carbonfasern führten, bedürften sie weiterer Erforschung. Der zweite große Produktionsschritt umfasst die Umwandlung des Vormaterials, aktuell noch PAN, zur Carbonfaser. Dieser erfolgt typischerweise in drei thermischen Prozessen.
„Die für diesen Herstellungsschritt notwendigen Oxidations- und Karbonisierungsanlagen müssen in Bezug auf Temperaturgleichmäßigkeit, Atmosphäre und Strömungshomogenität über den gesamten Prozess höchste Genauigkeit sicherstellen. Nur so unterliegt jede einzelne Faser den gleichen Bedingungen. Damit gewährleisten die Anlagen eine konstante Qualität mit kürzesten Durchlaufzeiten und hoher Effizienz“, erläutert Link.
Der Schlüssel zu nachhaltigen Carbonfasern liegt demnach in hochgenauen Prozessen sowie in effizienter Anlagentechnik, die Bedarfe und Verluste minimiert, aber auch Restwärme effektiv nutzt. Laut Link müssen dafür in der „schwarzen Linie“ die einzelnen Teilprozesse wie Abwickeln der PAN-Fasern, Fadenantrieb, Oxidation, Karbonisierung, Waschen sowie Schlichten und Aufwickeln der Carbonfasern präzise aufeinander abgestimmt und verknüpft sein.
TU München richtet Lehrstuhl für CFK-Teile-Produktion ein
Für den dritten Produktionsschritt, der Fertigung der CFK-Teile, hat die Technische Universität München den Lehrstuhl für Carbon Composites ins Leben gerufen. Denn ein Großteil der Herstellungskosten fällt in der Teilefertigung an. So braucht eine Spezialpresse etwa 8 min, um aus einem vorimprägnierten Kohlenstofffasergewebe und Harz ein CFK-Fertigteil zu machen. Eine Standardpresse formt in dieser Zeit rund 150 Blechkotflügel. „In den Fertigungsprozessen gibt es derzeit keine ausgereifte Automatisierung, jedoch noch hohe Verschnitte der Faserhalbzeuge und eine aufwendige Qualitätssicherung“, bemängelt Elisabeth Ladstätter, stellvertretende Leiterin des Lehrstuhls.
Um solche Verschnitte sowie ausrangierte Carbonfaserkomponenten zu verwerten, treibt das Bifa Umweltinstitut in Augsburg innerhalb des Spitzenclusters „MAI Carbon“ Recyclingverfahren voran. So will Geschäftsführer Wolfgang Rommel eine durchgehende Recycling-Prozesskette entwickeln, die notwendige Verfahrensschritte wie Demontage, Sortierung und eventuelle Zerkleinerung der Carbonfaserkomponenten umfasst. Damit schließt sich der Carbonfaser-Stoffkreislauf.
Ein Beitrag von: